【小编注】早上听“得到”APP《液晶演义》第5集,品控手册、工厂技术、点滴累积、无法复制等关键词让小编本能的联想到了HACCP。危害分析与关键控制点(HACCP)体系就是这么一种帮助企业根据自身特点、高效经济的、不断积累固化经验、形成工厂核心技术的工具。简要摘录文中要点,欢迎有共鸣者交流讨论。
引子
《液晶演义》在分析韩国液晶产业超越日本的原因时提到一个维度:日本在液晶领域的专利数远超韩国,但日本的专利多是“实验室技术”方面的,而韩国的专利多是“工厂技术”方面的……
什么是实验室技术?
说到科学技术的时候,我们脑子里往往会联想到实验室、穿白大褂的科研人员、各种实验设备等等。技术由科研人员在实验室中研发出来,然后拿到工厂中去大规模投产,我们可以把这种技术称为实验室技术。
什么是工厂技术呢?
比如,在液晶生产中,避免灰尘是个很大的问题。而且,液晶生产对无尘的要求非常高,比同为半导体的CPU等还要高。同样是混入10粒尘埃,CPU生产只要剔除那10片CPU即可,其他的还是合格品;液晶屏则是出现了10个不发光的坏点,整块屏因此就算不合格,彻底报废了。
在实验室中很容易小规模做到无尘。但在实验室中做到没什么意义,重要又困难的是在大型厂房中做到。几十米高、各种设备轰轰运转、人来人往的巨大厂房,建成无尘车间,这完全是另一套技术。
重点在于,这种技术只能在当时当地逐渐摸索、改进,不可能事先在实验室中完成,然后简单转移到工厂中。这种只能在当时当地、结合实际生产而积累的技术,就是工厂技术。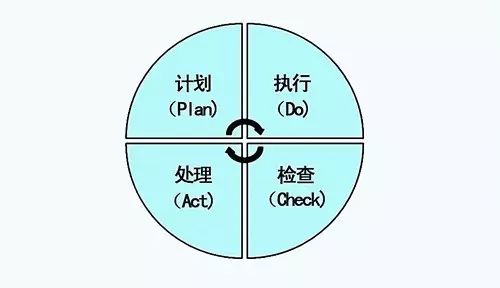
“按比例放大”是思维陷阱
很多人的思维误区是:推崇实验室技术,轻视工厂技术。这其实是缺乏工业思维的表现。
工业思维,是要从规模上去考虑问题。自己家做饭要做到色香味俱全,好好练习问题就不大,但是如何为一万人提供365天、品质一样、口感一样、安全合格的食品?它就是巨大的系统,环节巨多,风险巨大,不是把厨房做饭的技术复制一万次那么简单。
规模上一个量的变化带来的可能是问题指数级的增长,甚至是本质上的变化。
实验室技术 VS 工厂技术
和实验室技术相比,单个的工厂技术或许不那么高深,甚至很不起眼,但大量的细小改进、点滴窍门积累起来,就成为一套竞争对手更难复制和超越的大技术。
工厂技术也并非不能总结和提炼成经验(类似实验室技术的经验),而是技术非常复杂,不容易复制,甚至不可复制。
一旦累积出这样的工厂技术,它不仅仅是存在于说明书上的经验,实际上还存储在每一个同事的脑子里,和他们之间的协作关系中,将成为工厂的核心竞争力。
如何高效的创造工厂技术
对于食品企业,问题当然也得发现一个、解决一个、积累一个,逐渐形成工厂技术。实践证明,在食品企业积累工厂技术,通过运用危害分析与关键控制点(HACCP)的原理和方,能更全面的分析问题,更有效的发现问题,更有针对性的解决问题,并能持续改进。
HACCP可以帮助工厂在已有的基础上,结合本工厂特点,对工艺、原料、环境、过程、受众等因素可能带来的风险和危害进行全面分析,识别出显著危害并加以控制、实时监控、及时纠偏、定期验证、按时记录。通过在加工过程中增加一小部分成本(COST),避免因产品质量安全问题造成巨大代价(COST)。事半功倍。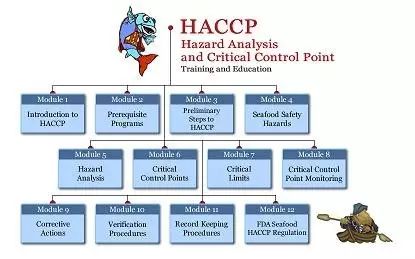
从研发环节就要引入HACCP
创新必须以整体形象才能形成影响力。
畅销的食品离不开研发团队的不懈努力,但就像本文一直提醒的,不能仅满足于形成实验室技术,而是应该从研发开始邀请工厂管理人员、生产人员参与,考虑规模化可能遇到的问题,提前制定解决方案,最终形成“实验室+工厂技术”。
当你在研发时考虑各种成本、风险、管理细节和品控、食品安全等因素时,你离成功更近。
你们工厂的品控手册有多厚?
下次如果有领导或国外的检查官到你工厂参观检查时,不要再提“从我爷爷小的时候工厂就是这样生产的,从未发生过质量安全问题,我们是百年老店”。而是应该给他们搬出工厂的质量手册,告诉他们从我爷爷那时到现在,我们的HACCP体系已经升级了81版,并且昨天还在完善中,这套体系与工厂的每一名员工相连,这是我们工厂成为百年老店的核心技术。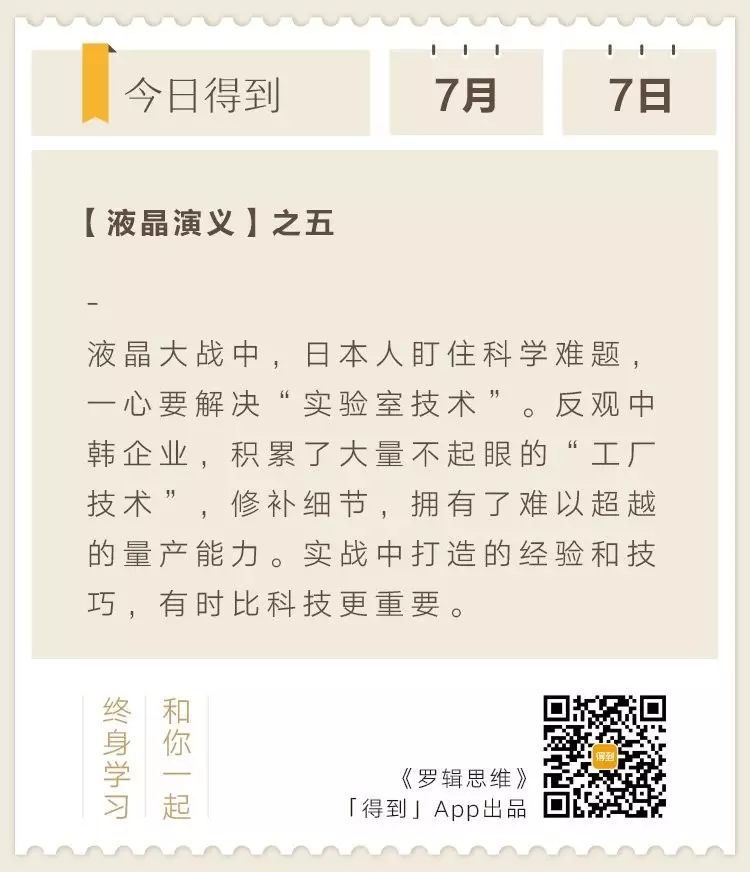
大部分文字来自“得到”APP《液晶演义》之五,深表感谢。
=====HACCP=====
欢迎点击文章左下角的"阅读原文",了解"CHINA-HACCP公众号"更多内容。
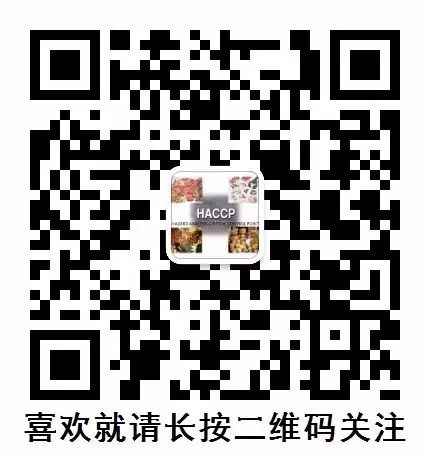