塑料尾门第一次走进大众的视野应该是2014年初,国产奇骏上市之后。你要是在某车之家论坛里搜索“塑料尾门”四个关键字,首页十条检索结果里六条是来自于奇骏论坛,如图1。大家都是一脸“你逗我呢”的懵逼表情看着这个塑料的尾门,千万个不信任。这玩意儿能抗撞?安全吗?会不会一蹭就烂了?坏了怎么修?更多的,大家偷工减料,糊弄中国人的帽子已经扣出去了。日产也是一脸大写的冤,伦家欧洲,本土,北美都是这样的,也没见这么大的反应啊。我想,可能是,我们的钢板崇拜教众都比较虔诚吧。
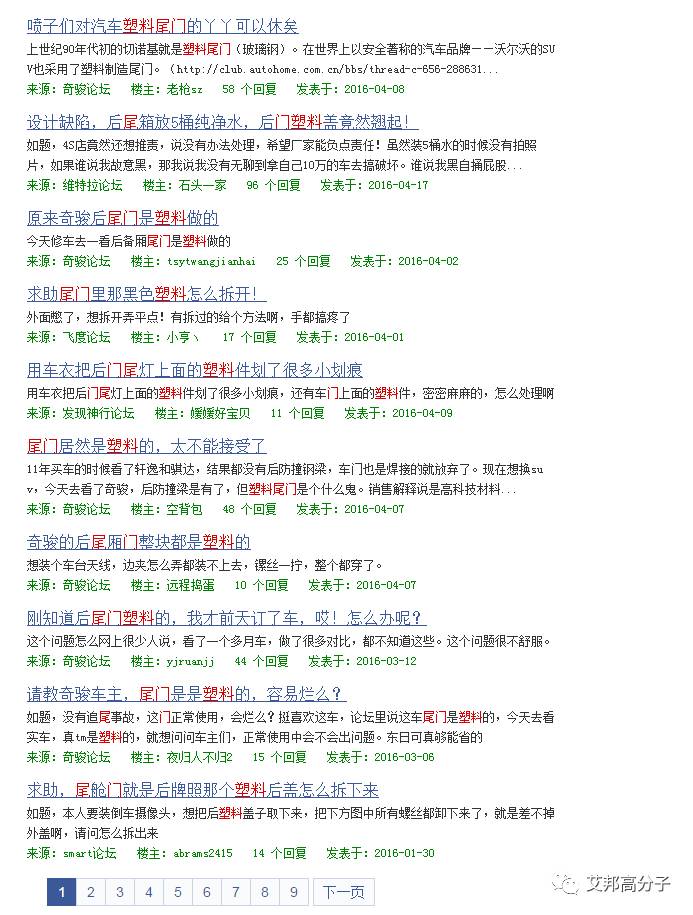
图1
如果我们把时间往回拨,其实2014款的奇骏,第三代奇骏,根本不是国内第一款上市的应用塑料尾门的车型。早在2009年4月份上市的沃尔沃的XC60就是塑料尾门,稍微晚一点的第一款自主品牌配置塑料尾门的车型,荣威E50电动车于2012年底上市,在比奇骏稍微晚一点2014年4月份发布的PSA集团的旗下高端品牌DS的第一款SUV车型DS6,也是塑料尾门。还有就是,2013年初国内上市的五门版路虎极光也是塑料尾门。如果我们去这些车型的论坛看看,也有反馈车型是塑料尾门的,但是远没有奇骏车主的反应强烈。说实话,本人了解到塑料尾门,也是从奇骏开始的。如果我们仔细看上面这几个车型,能发现一些特点,奇骏是这些车型中最畅销,最居家,最大众的车型。其他路虎极光、XC60、DS6、E50等。要么高端豪华消费群体,要么是冷门车型,受众都是偏小的,所以这些车主的声音才没有被大家所听见,没有广泛传播。
那你可能会问了,既然已经有这么多车型,而且是高端车型都用塑料尾门了,肯定是由一些好处或者有点的,主机厂为什么要把原来的钢板尾门或者铝板尾门换成塑料尾门呢?这是个很好的问题,我们下面就好好讨论一下。
要开始讨论这个问题,我们先要堆砌几个和汽车无关键词:环境保护,低碳社会,可持续发展,和谐自然……你可能会觉得这些词又红又专的感觉,和我们今天要讨论的问题没什么关系啊。那你就错了,这些我们活着从小就耳熟能详的,或近几年才热起来的词语,也是全球当下都关注的话题。毕竟,地球只有一个,汽车作为现代社会最普遍的交通工具,其使用的是化石燃料,不可再生,产生的气体中又有许多对环境有害的成分,自然是全社会关注的焦点。这些焦点对应到汽车上,也是几个关键词:燃油经济性,碳排放,材料回收再利用,能源回收……在对应到细节的技术上,就是发动机技术的发展与创新,新型燃料的应用,混合动力系统的应用,电动车的开发,怠速起停系统,刹车能量回收系统,排放控制技术的发展,材料循环使用,以及轻量化。
如果我们简单的画一个路线图,塑料尾门的作用会是这样的。
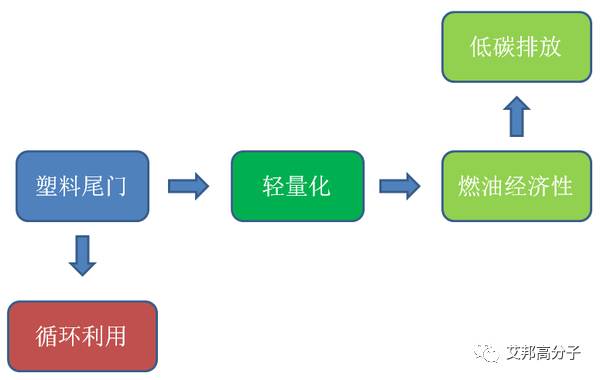
所以说,随着欧美越来越严格的排放法规,诸如欧六法规的实施。而且欧盟在2009年通过了第443号法规,旨在控制CO2的排放,其远期目标是到2020年,CO2排放控制在95 g/km. 面对如此严苛的法规,主机厂自然会使出全身解数去压榨整车各个方面的性能,轻量化也自然成了一个重要的方面。而且根据研究结果,汽车每降重10%,燃油效率能提高6%~8%不等;汽车每降重100kg,CO2排放降低8.5g/km, 如图所示。
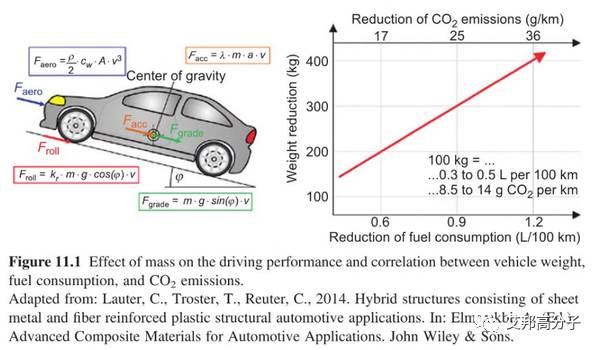
所以,从燃油经济性方面来说,轻量化将是未来的趋势,所以才有了塑料尾门的诞生。
拨开汽车制造史的迷雾,可以对塑料尾门按照其材料分为以下三类:
基本上,我们所说的塑料尾门,就是这内板,外板,加上扰流板这三大件是塑料件,而不是钣金件,如图所示。
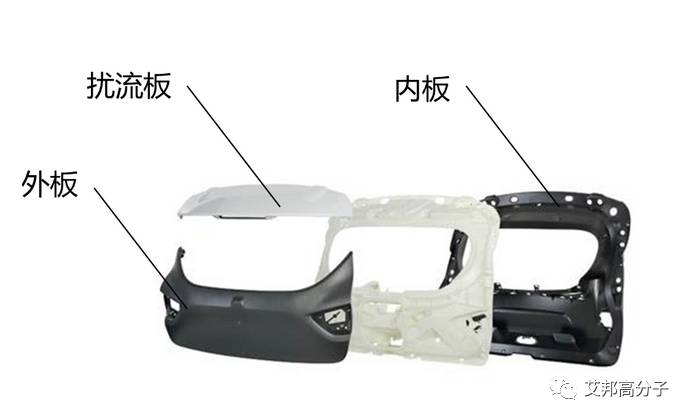
除此之外,尾门上还需要集成很多很多东西,从上大小有:天线,高刹灯,玻璃,挡风板,尾灯,摄像头,电动尾门开关,牌照板,牌照灯等等。总之就是,接口极多。
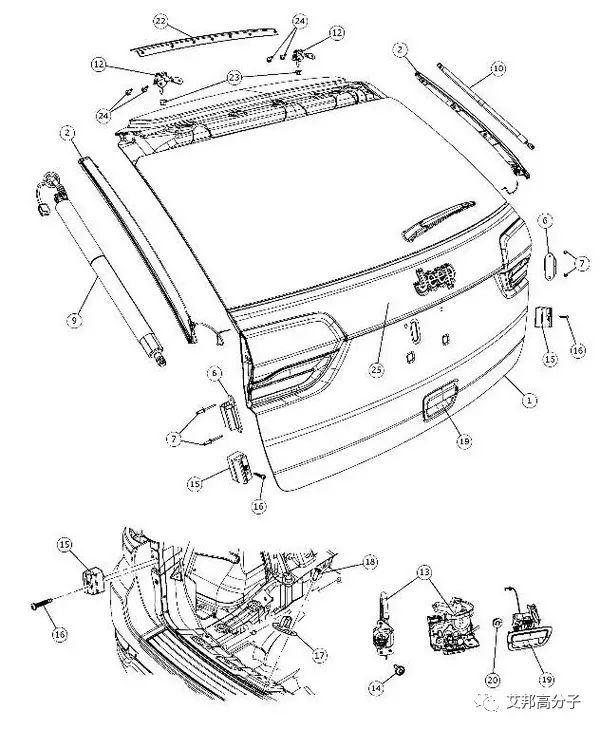
1.尾门 2.防夹传感器 6&15.缓冲块 12.铰链 13&19.门锁 9.电撑杆 10.气弹簧 22.密封条
塑料尾门的发展历史,基本上也是一路从最早的热固性塑料,到热固性塑料,热塑性塑料相结合,再到全热塑性塑料这么发展来的。往前推,我们回到1946年的美国底特律,William Bushnell Stout制造出了世界上第一辆覆盖件均为玻璃纤维复合材料的汽车,Stout Scarab,虽然这台车仅此一台能够使用,但是已经足够将这位福特汽车董事,兼职飞机设计师留名汽车塑料化的历史了。另外,这台车也是世界上第一台装配空气悬架的车型。下图中正是William Bushnell Stout驾驶着Stout Scarab. 虽然这辆车拉风异常,很吸引人研究,可是这台车并没有得到量产。Stout驾驶着它在美国各处旅行,最终行程达到250000英里。
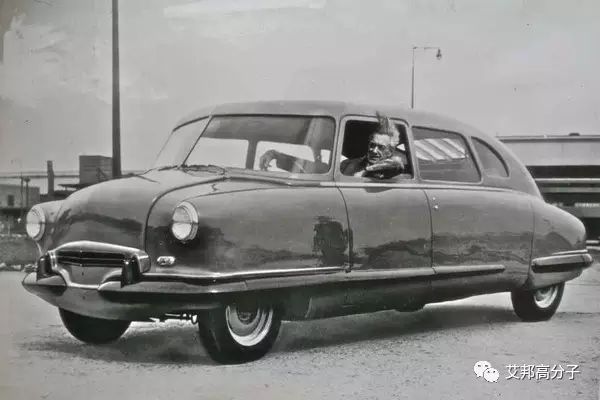
时间来到1953年,通用汽车量产了一款名叫Corvette的超跑,其车身全部使用玻璃纤维复合材料,已达到车身轻量化的目的。这是第一次玻璃纤维复合材料应用在量产车型上,而现在,克尔维特这类超跑都已经开始大量使用碳纤维复合材料来实现车身及其他结构件的轻量化。通过这种轻量化技术,来提升整车的加速性能。下图为克尔维特第一辆车型下线。
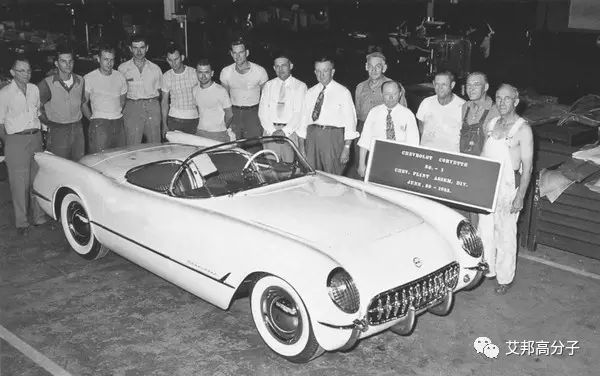
随后的很多年,越来越多的复合材料被应用到汽车上,雷诺 5上第一个SMC保险杠,奥迪Ur-Quattro上的SMC行李箱盖等。直到1982年雪铁论BX上市,才有了真正意义上的第一辆带塑料尾门的车型。
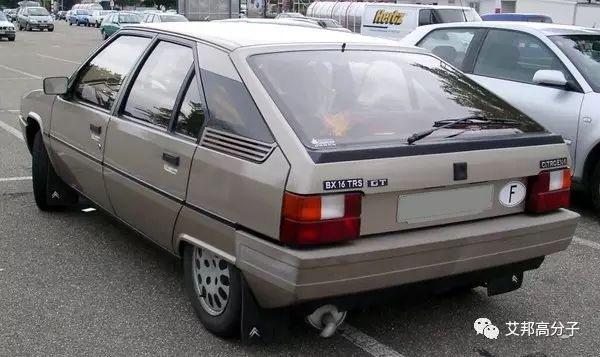
由博通设计的这款掀背车,在发动机盖上使用了SMC材料,而在尾门上使用了BMC材料。这里大概解释一下这两种材料的区别。SMC 是Sheet molding compound的缩写,即片状模塑料。主要原料由SMC专用纱、不饱和树脂、低收缩添加剂,填料及各种助剂组成。而BMC(DMC)材料 是Bulk(Dough) molding compounds的缩写,即团状模塑料。国内常称作不饱和聚酯团状模塑料。其主要原料由GF(短切玻璃纤维)、UP(不饱和树脂)、MD(填料)以及各种添加剂经充分混合而成的料团状预浸料。从名字出发,形态上,SMC材料主要是片状的,而BMC主要是团块状的(真!废话),另外一个主要的区别点是,SMC主要使用长玻纤作为增强纤维而BMC一般是短玻纤。这个带来的效果就是SMC件的物理性能一般比BMC件的要好一点。
雪铁龙BX之后,越来越多的厂商开始尝试使用SMC或者BMC件尾门。比如1993年土星的旅行轿车使用SMC尾门。
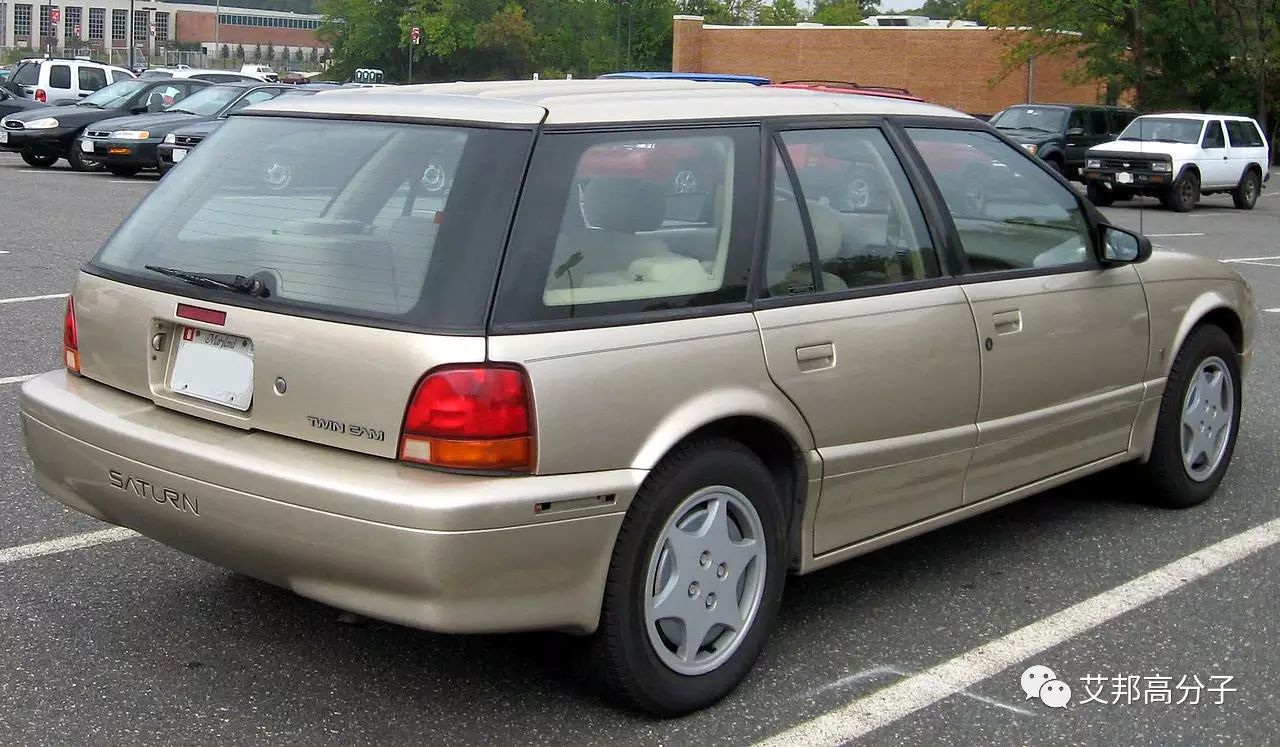
1996年雷诺Espace使用SMC尾门
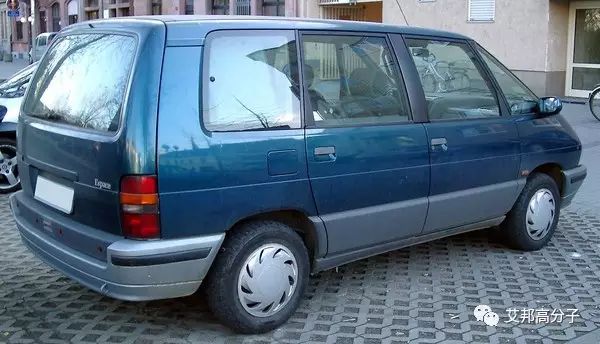
1996年沃尔沃V70使用SMC尾门

2002年梅甘娜II使用SMC尾门
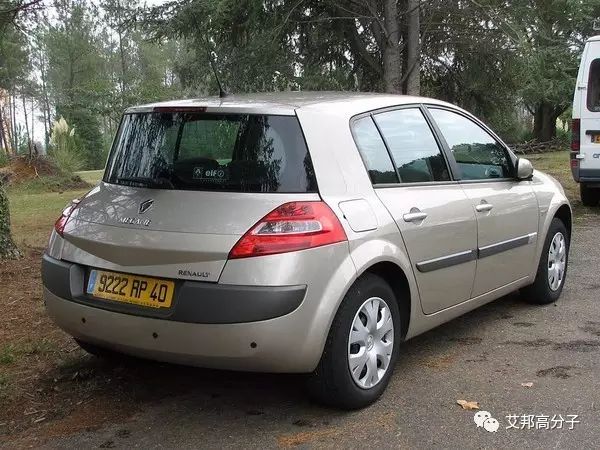
这类尾门,全部使用SMC复合材料,俗称玻璃钢。特点是刚度高,外观效果好,产品收缩率低,缺点是密度还是比较高,降重效果一般,而且材料回收难度高,如果采用掩埋式处理,在土壤中百万年都不会降解,会产生严重的土壤污染。而且复合材料的外板由于玻璃纤维的缘故,脆性比较大,塑性不好,不抗撞,一碰,容易裂。种种原因,就导致了内板使用复合材料,外板扰流板使用塑性材料的第二代尾门的出现。
第二代尾门,内板使用SMC材料,模压工艺成型,外板使用PP或者TPO等热塑性塑料,注塑工艺成型。内板采用模量高,刚度和强度都比较好的复合材料,提供力学支撑;外板使用热塑性塑料,提供更加自由的外形设计空间,良好的弹性,轻微碰撞可复原,降低维修成本。而且热塑性塑料通过注塑成型,方便实现自动化生产,有利于降低生产成本,提高生产效率。尾门系统供应商彼欧称这种尾门为“Higate”(Hybrid Tailgate)。这种技术第一次被应用是在2004年法国雷诺发布的Modus上。而其尾门供应商,正是彼欧,其采用的正是SMC内板,TPO外板的形式,两者通过涂胶工艺进行装配。
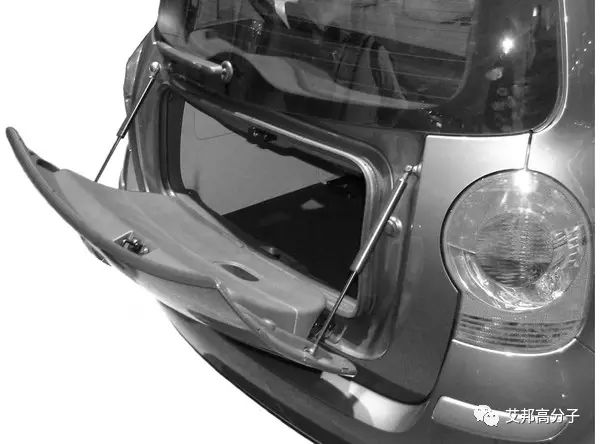
接着2007年马自达5使用了日本本土供应商DaikyoNishikawa为期提供的塑料尾门,也采用了这种技术。
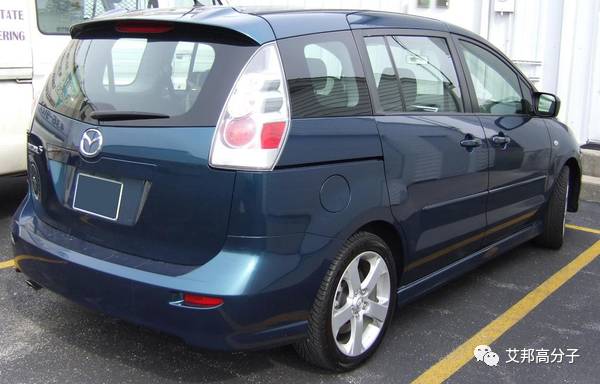
2011年标致508的旅行版也采用了相同的材料和工艺
2012年路虎极光
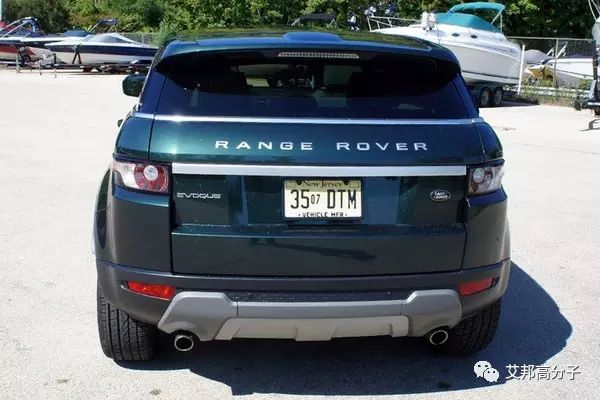
2013年路虎揽胜及揽胜运动版
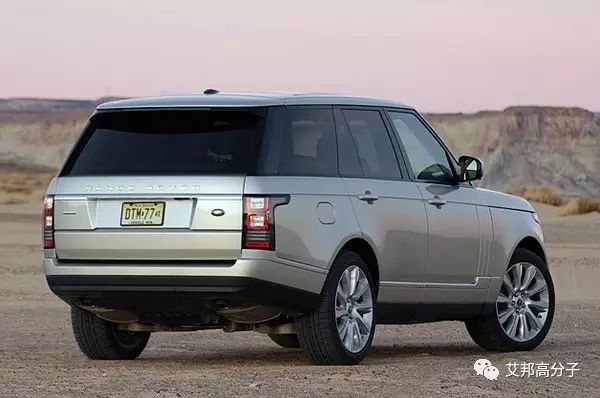
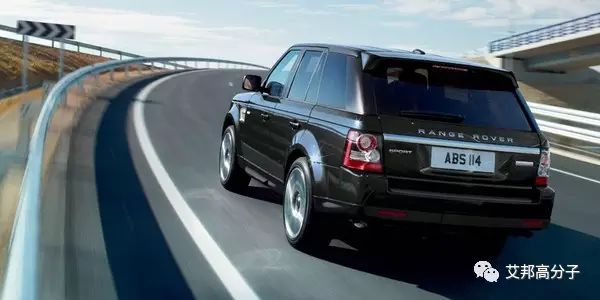
2013年标致C4 毕加索
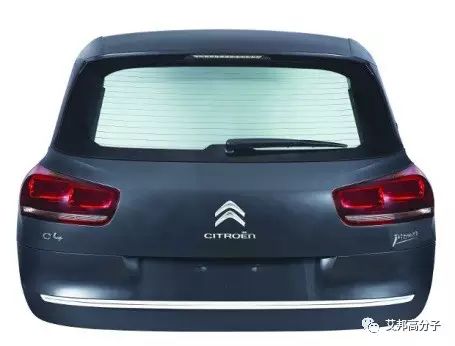
2013年捷豹XF旅行版
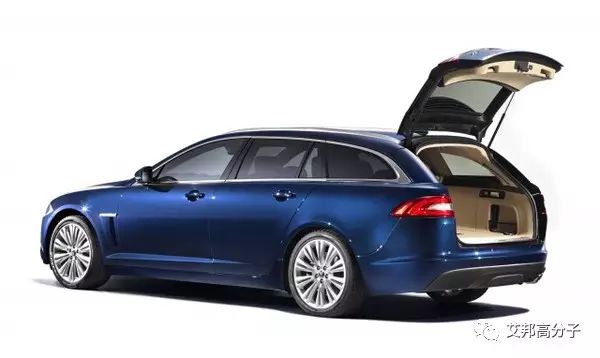
2013年大发Tanto
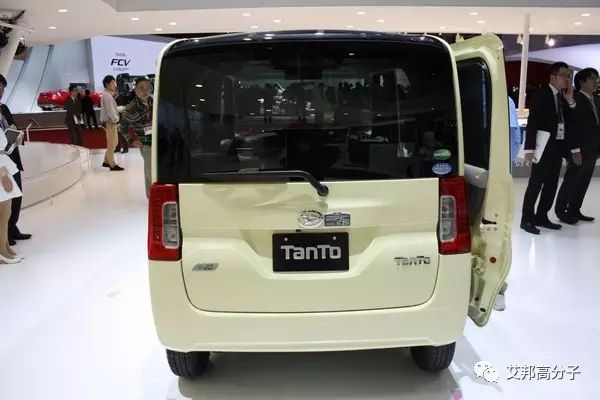
2013年马自达3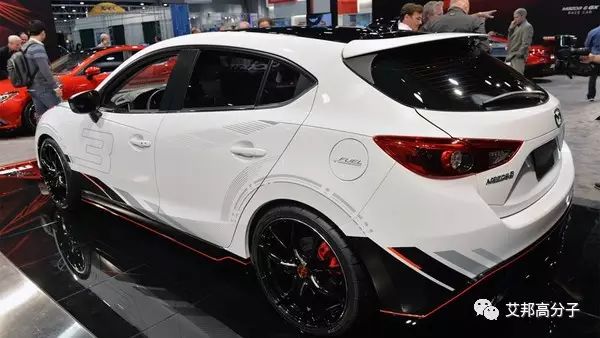
还有2014年国内上市的特供车型,DS首款SUV车型DS6,也是有彼欧打造的第二代尾门。
我们发现,2004年后这种新型的尾门集体爆发了,作为一名爱学习的工程师,我们必须剥丝抽茧寻找事实的真相,2011年前后肯定发生了什么事情,导致主机厂们开始不得不追求更加极致的轻量化技术。我们用第二张图往前推,就可以推到燃油和排放上,运用谷歌一搜索你会发现,欧盟国家2004年开始实施欧四排放法规,2009年实施欧五,2014年实施欧六,见图。
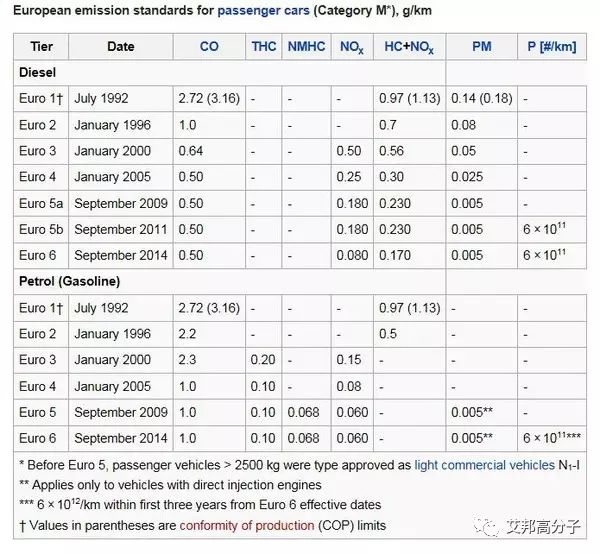
日本2001年将《汽车NOX法》修订为《汽车NOX和PM法》,2007年又修订了该法案,进一步加大了排放物的遏制力度;2004年美国实施“Tier2”第二阶段排放法规,2009年实施“Tier3”第三阶段排放法规。随着越来越严格的排放法规的实施,主机厂不得不在整车各个系统上想办法,以力求最大化减少排放物和燃油消耗。
2014年欧六排放实施,以及2020年的碳排放目标乃至2050年的碳排放目标,无意识摆放在各大主机厂面前的一道坎。2008年八国领导人峰会上达成的到把2050年把全球温室气体排放减少50%作为长期目标的共识,2009年哥本哈根世界气候大会指定的2012年到2020年全球减排协议的指定——种种迹象表明,我们对环境保护的力度越来越重,寻求燃油效率最大化,有害排放物最小化已经成为全球共同的目标和难题。汽车行业作为能源消耗和排放物贡献的大户,自然是责无旁贷,要担负起自己的责任。
为了这一目标,各主机厂及其供应商不断探索,研发了第三代尾门,全塑尾门(Full Thermoplastic),内板使用长玻纤增强的PP(LGF+PP),外板和扰流板使用PP或者TPO,全部使用注塑工艺成型,然后使用涂胶工艺进行装配。长玻纤增强PP与SMC材料相比,刚度模量相差不是太大(根据不同的玻纤比例,效果会很不一样,有一些低组分玻纤增强的PP件感官上还是偏“软”),但是密度要比SMC小,一般地尾门适用的SMC材料密度都在1.8左右,而相同比例玻纤增强的PP+LGF密度一般在1.5左右,这是什么概念呢,我拿手里的一个内板算了一下,大概就是可以降重1.3kg左右,如果做过轻量化降重项目的工程狗们都能理解这是什么概念,所以降重效果还是很明显的;另外由于PP+LGF材料使用各种添加剂要少一点,所以挥发物少,在VOC检测上有优势;还有就是采用注塑成型,自动化程度比模压要高;并别注塑的生产循环速度要比模压快,加之自动化程度提高,所以在生产效率上也有优势。总结下来,就是降重效果明显,而且可以生产节省成本。
第一个应用这种全塑性塑料尾门的车型是2012年雷诺新Clio, 其内板是LGF-PP,外板是PP,扰流板是ABS,见图。
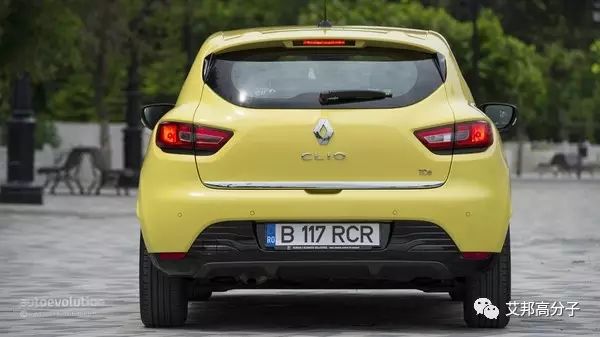
在项目预研阶段,雷诺定下了降重10%并且易回收的目标。为了达到这个目标,材料供应商Styron(现已改名Trinseo)与雷诺一起研究开发了两年,最终开发出了可以量产的全塑尾门。内板、外板和扰流板都是用Trinseo的材料。
2013年尾门供应商彼欧开发了自己的第一款全塑尾门,标致新308的尾门,内板LGF+PP,外板和扰流板PP,材料供应商是SABIC.
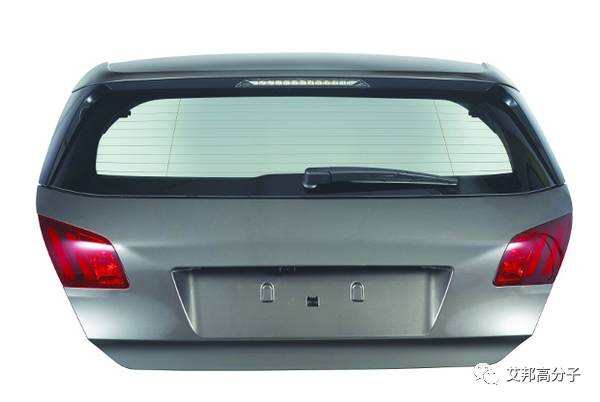
同样是2013年法兰克福车展,日产发布了其第三代X-trail,搭载着麦格纳为其开发的全塑尾门。这款车型14年国内是上市之后就是国产新奇骏,其北美版为Rogue. Rogue的塑料尾门获得了当年SPE(The Society of Plastic Engineers)的创新大奖。
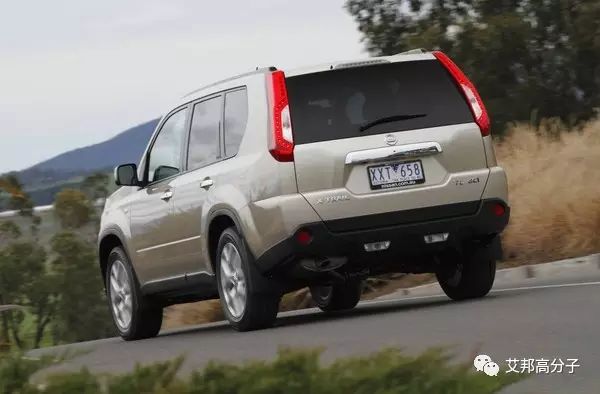
2014年宝马i3使用麦格纳开发的全塑尾门。
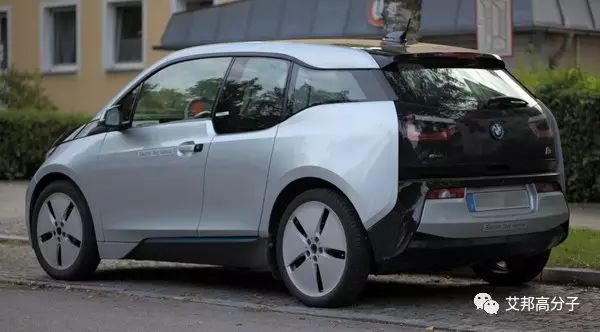
至此,基本上三代塑料尾门的编年史我们就已经捋的差不多了,有些遗漏或者不对的地方,由于信息搜集上的限制没办法做到完美,遗漏之处还请批评指正。
再回到排放的话题上来,塑料尾门的开发,就是顺应全球对汽车减少燃油消耗的诉求以及排放法规越趋严格的大势之下,我们可以看到欧洲和日本的厂商对于此项技术比较热衷,搜寻资料的过程中发现一个很有意思的网站,其预测了到2020年,那些主机厂可以达到碳排放标准而那些可能达不到。其中法系的标致和雷诺被看好,日系其次。而德系,美系,韩系则可能达不到目标见图(29)。我们从塑料尾门的开发力度上,也可以说明这一点。
从目前的情况看,可以肯定的是未来塑料尾门肯定会越来越普及,SUV和MPV车型,混动和电动车型,都有轻量化的需要来提升油耗,排放或者续航能力,会有越来越多的主机厂去做这样的尝试,我们拭目以待吧。
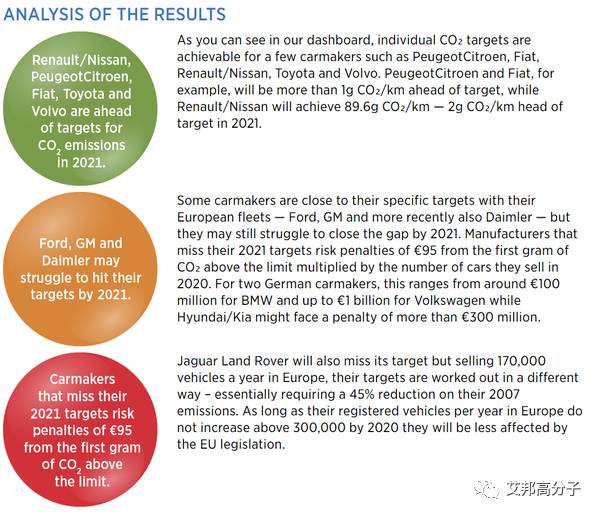
文章来源:知乎 作者:P Tyne
推荐阅读:
如果您还想了解更多,加入汽车产业链交流群,请长按以下二维码添加小编微信申请加入,验证时请备注“公司+主营”
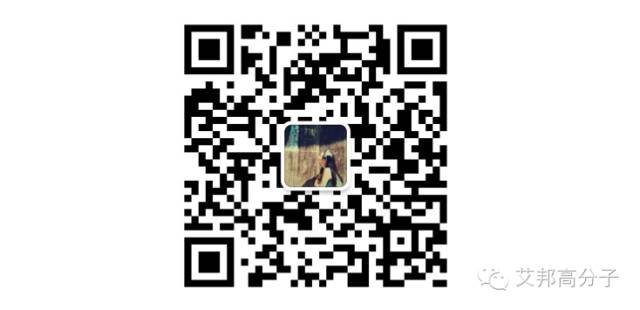
阅读原文,申请加入汽车产业链交流群
↓↓↓