高端装备制造业是我国七大战略性新兴产业之一,其以高新技术为引领,处于价值链高端和产业链核心环节,是现代产业体系的脊梁,是推动工业转型升级的引擎。大力培育和发展高端装备制造业,是抢占未来经济和科技发展制高点的战略选择,对于我国加快转变经济发展方式、实现由制造业大国向强国转变具有重要战略意义。 大力发展高端装置制造,离不开智能制造,更离不开处于智能制造核心地位的数控机床。数控机床可将金属毛坯加工成机器零部件,广泛应用于机械工业、模具行业、汽车工业、航空航天等领域,代表了国家工业发达程度,决定了一个国家的制造实力与发展水平,关乎我国工业、产业以及国防的安全。
图1.工业化与机床进化史
对应于工业1.0~工业4.0时代,机床从机械驱动/手工操作(机床1.0)、电力驱动/数字控制(机床2.0)发展到计算机数字控制(机床3.0),并正在向赛博物理机床(Cyber-physical machine)/云解决方案(机床4.0)演化发展,数控机床始终扮演核心的角色。
我国高度关注数控机床的发展,《中国制造2025》将高端数控机床列为制造业重点发展领域之一,自2019年以来,国家已连续发布多项政策重点扶持国内机床,尤其是数控机床产业发展。
图1.2019年以来我国发布的数控机床行业相关战略及政策 随着我国制造强国战略深入实施,我国数控机床行业市场集中度和国产化率不断提升,基础装备转型升级取得积极进展,但发展不平衡、不充分的问题仍然突出。
从2003年至今,全球数控机床行业的专利发展大致可以划分为三个阶段: 数控机床行业的全球年专利申请量缓慢增长,从20世纪50年代起,经过多年的发展,数控机床已经实现PC化计算机控制以及开放式结构的CNC系统,到2000年左右,数控机床的技术已经达到非常高的程度,呈现缓慢发展的态势。 这一时期,随着智能化数控技术的萌芽,以及新一代信息技术和人工智能的发展,智能传感、物联网、大数据、数字孪生、赛博物理系统、云计算和人工智能等新技术与数控技术深度结合,促使相关企业进行技术研发,并取得突破性进展,不断推出新产品。 从2021年开始,增长速度放慢,尤其是2022年的申请量有降低的趋势,主要由于之前的技术快速发展,数控机床产业智能技术已经相对成熟,加之近年来新冠疫情对全球经济的影响,可以预测全球数控机床产业的专利申请将在近几年仍保持较为平缓的趋势。 在全球范围内,排名前10位的申请人均为国外知名企业,并没有中国企业,其中发那科、三菱和西门子是全球知名的数控系统巨头,数控系统基本垄断了全球市场,肯纳金属、伊斯卡和山特维克则是知名刀具生产企业,德玛吉森精机和大隈则是知名的数控机床生产企业,安川电机是全球领先的电机生产企业
从全世界范围来看,专利申请主要分布在中国、美国、日本、欧洲、韩国,这些国家和地区均为数控机床主要生产国和消费国,同时也属于数控机床主要的技术输出国家和地区。
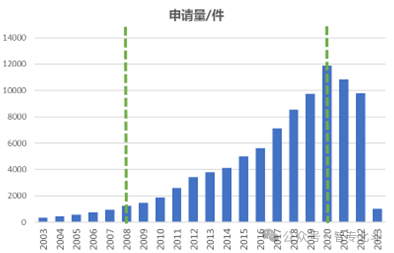
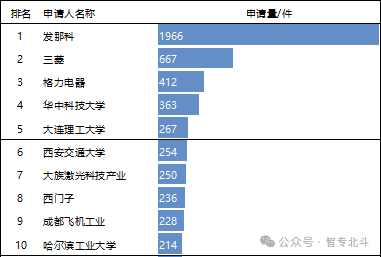
与全球态势略有不同,从2003年至今的中国专利申请趋势大致可以划分为起步期、快速增长期和瓶颈期三个阶段。 国家“863计划”的“高精尖数控机床”重点专项,支持了航空、汽车等部分重点领域急需的高精尖数控装备研制,我国数控机床产业开始起步。 在这一时期,专利申请量开始快速增长,国家启动实施“高档数控机床与基础制造装备”科技重大专项(简称“04专项”),对国内数控机床产业进行扶持,在此期间,我国在金属加工数控机床的生产、消费和进口三个方面均列世界第一,国产数控机床市场竞争力不断增强,在国内中低端数控机床市场已占有明显优势。 年申请量相比2020年的峰值有所降低,这是由于近几年全球经济出现衰退迹象,加上受到后疫情时代影响,在国内经济稳内需、调结构的大环境下,数控机床行业的技术研发和专利申请出现了一定程度的瓶颈。 排名前10位的专利申请人中,国外数控机床企业例如发那科、三菱等十分重视中国市场,在国内进行了较多的布局;国内申请人中有多所高等院校,包括华中科技大学、大连理工大学、西安交通大学等,国内企业包括格力电器、大族激光科技产业、成都飞机工业。 从中国申请人地域分布来看,中国数控机床行业专利排名前十位的省份依次为江苏、广东、浙江、山东、辽宁、上海、安徽、湖北、四川和北京,均属于经济相对发达、知识产权意识较强的地区。 数控机床主要包括数控系统、功能部件、机床本体和辅助系统四个分支。在国外专利申请中,数控系统的申请量占据绝对优势,其次为功能部件,国内数控机床各一级技术分支的占比与国外占比基本同步,在数控系统和功能部件领域的创新最多。相比较而言,国内在数控系统方面的占比明显偏低(差距为26%),辅助系统和机床本体的占比较高。 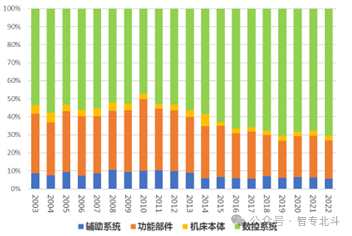

图6.国外和国内专利分布发展趋势(左图-国外;右图-国内) 从图6可以看出,与国外发展趋势明显不同,我国数控机床专利申请占比中,机床本体和辅助系统占比逐年上升,对于数控机床的核心技术分支数控系统以及功能部件,其占比逐年下降,这与相关分支研发难度较大,成本高,短期的收益低等有密切关系。随着我国智能制造水平的不断提升,加之政府出台各项政策进行支持和引导,数控机床的核心技术将被不断突破,我国企业一定能够引领数控机床产业发展潮流。 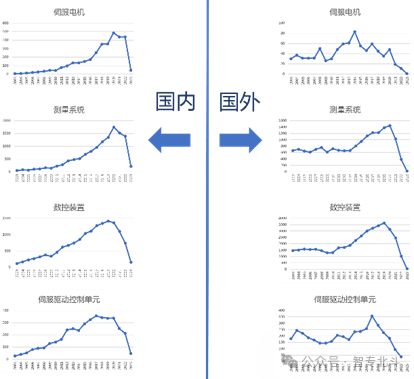
上图为数控机床核心技术分支数控系统以及各细分分支的发展趋势。国内数控系统专利从2003年开始申请量始终呈现快速增长的态势,2020年达到峰值,接近4000件,但仍然低于国外申请。对于数控系统的细分分支,最为重要的数控装置、测量系统以及伺服驱动控制单元,国外申请人进行了大量的研发,均呈现上升的态势;各技术分支的国内申请均呈现快速增长的态势。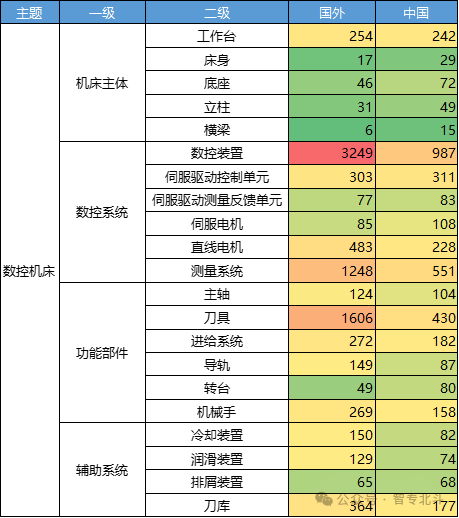
上表展示了国外和中国各技术分支的协同创新情况。国内外协同创新均集中在数控装置、测量系统、刀具和伺服驱动控制单元,除了上述重点领域之外,国外更注重对直线电机、刀库的协同研发,而国内更重视对伺服驱动控制单元和工作台的协同研发。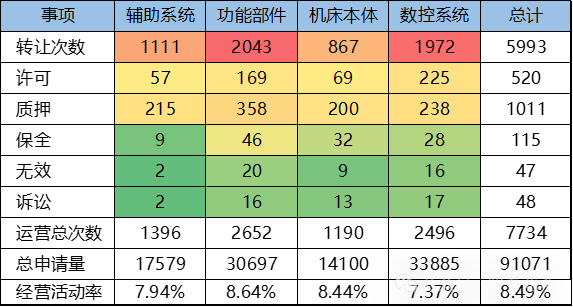
上表为各技术分支的专利运营情况,从2003年至2023年,中国数控机床产业专利运营活动占全部申请总量的8.5%,专利转让是数控机床产业最主要的专利运营方式,此外质押和许可的次数也比较多,位居第2、3位。经营活动率最高的技术分支为功能部件。数控系统的经营活动率占比最低,这与数控系统大多为国外企业垄断,技术门槛较高,维权难度相对较大有密切关系。 根据数控机床技术的发展现状,重点分析了“智能自适应”“智能反向间隙补偿”和“空间几何误差补偿”这三个关键技术。 “智能自适应”:随着人工智能在计算机领域的不断渗透和发展,数控系统的智能化程度不断提高,数控系统的自适应控制技术能检测加工过程中的重要信息,并自动调整系统的有关参数,从而改进系统运行状态。 “智能反向间隙补偿”:主要针对机械传动在改变转向时,反向间隙的存在引起伺服电机的空转的缺陷,需要定期对机床各坐标轴的反向偏差进行测定和补偿,而随着智能化、自动化技术的发展,反向间隙补偿也逐渐实现“智能化”。 “空间几何误差补偿”:随着数控机床加工精度不断提高,需要在系统上对数控机床几何误差进行分析与补偿,近年来发展了基于数控系统插补数控的几何误差补偿法。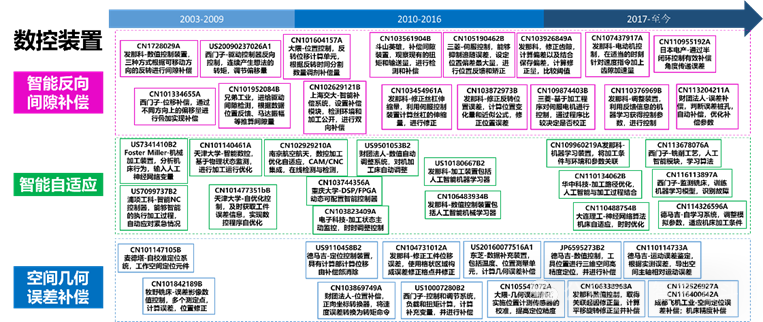
上图展示了数控机床关键技术的发展路线,各分支的主要研究思路以及未来发展方向如下所述: 对于智能自适应技术的发展,主要是引入人工神经网络、深度学习以及人工智能等技术来提高智能化,通过智能化来适应不同零件的加工。未来在智能自适应方面的技术发展主要有以下方向:深入结合人工智能技术;改进传感器和通信单元;进一步完善控制模型,提高变换处理、建模分析和数据挖掘能力。 智能反向间隙补偿技术则集中于如何检测机床工作过程中产生的间隙误差,以及采用何种技术手段来进行间隙补偿,主要有以下发展方向:进一步改进测量设备的精度、参数;进一步优化计算单元,提高计算模型的准确性;进一步完善控制单元,改进修正方式,提高智能化程度。 空间几何误差补偿技术的主要改进思路为提高测量技术,通过改善误差分析和数学建模来提高数控机床的几何精度,未来主要有以下发展方向:改进几何误差模型,优化空间几何变换算法,研发通用误差模型;继续提高测量技术,例如改进测量仪器,完善测量方法;研发新型的加工工件补偿方法和补偿系统。 技术进步是数控机床产业相关企业具有核心竞争力的必由之路,为了适应和促进全球数控机床产业的发展,相关企业必须不断进行技术研发,通过科技创新,解决数控机床产业的技术难题,打破技术瓶颈,从而在竞争中立于不败之地,可以先攻克技术含量低的周边部件,之后逐步掌握高价值的数控系统以及核心功能部件。 数控机床产业涉及的技术分支十分广泛,国内也涌现出大量的相关企业,可以引导中小企业走“专业化、精细化、特色化、新颖化”之路,专注于主轴、伺服电机、直线电机等具有高附加值的细分市场,精耕细作,集中有限的资金、力量打造核心产品,发扬工匠精神,抓住产品的关键环节,实现技术突破,抢占市场。 在当今竞争激烈的国际环境中,越来越多的企业认识到,单靠自身的力量是不够的,而与其他企业联盟不失为一种降低风险和成本、提高企业总体竞争力的有效手段,通过构建企业战略联盟,能够有效地共同分担研发经费从而促进技术创新,拓展新的发展领域,实现优势资源互补,同时可以避免或者减少企业间的对抗性竞争。[1]、Liu chao, Xu Xun.
Cyber-physical Machine Tool- the Era of Machine Tool 4.0 [J]. Procedia CIPR,
2017
[2]、“数控机床发展历程及未来趋势”,刘强,《中国机械工程》,第32卷第7期
[3]、《我国数控机床六十年》,任国梁,2022
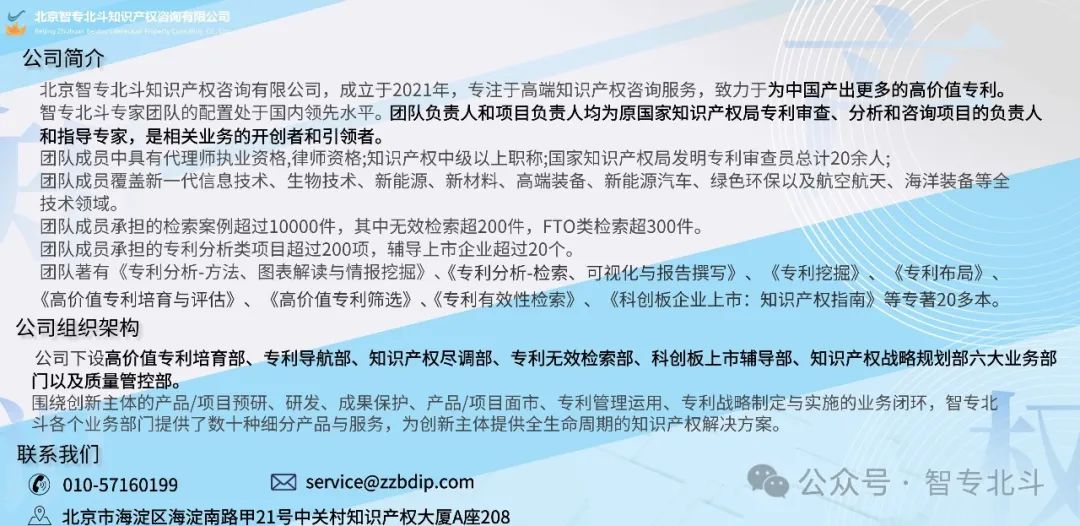