风起于青萍之末,浪成于微澜之间。世上没有一蹴而就的成功,却有水击石穿的奇迹。在全面推进深化改革的征程中,中航工业各单位立足业务领域、创新发展模式,探索开展了一系列切口小、落点准的“微改革”“微创新”,将发展堵点作为改革支点,将管理痛点当成改革触点,执改革之笔,书发展答卷,涌现出了一个个“微改革”典型案例,为建设世界一流企业持续注入新动力、增添新活力。
航空工业作为高技术集成的制造行业,在产业规模不断发展过程中,面临着一些问题,制约着航空产品的产出效率:一是产线设备的互联互通性不足,令数据采集与传输受阻,影响生产效率;二是生产线智能化程度不高,难以实现个性化、柔性化的生产需求;三是产线传统的基础设备设施年久老化,缺乏绿色制造理念。
中航工业沈飞深入贯彻落实习近平总书记关于“碳达峰碳中和”工作的重要指示批示精神,时刻铭记使命,以科技创新为引擎,用改革的智慧驱动高质量发展,基于航空制造行业特征推动绿色低碳转型,加快布局人工智能、数字孪生、工业物联网等新技术与产品设计、生产制造、物流运输、回收利用等环节深入融合,以实践应用数字化技术驱动产线升级绿色发展新模式,助力航空工业高端化、智能化、绿色化发展。
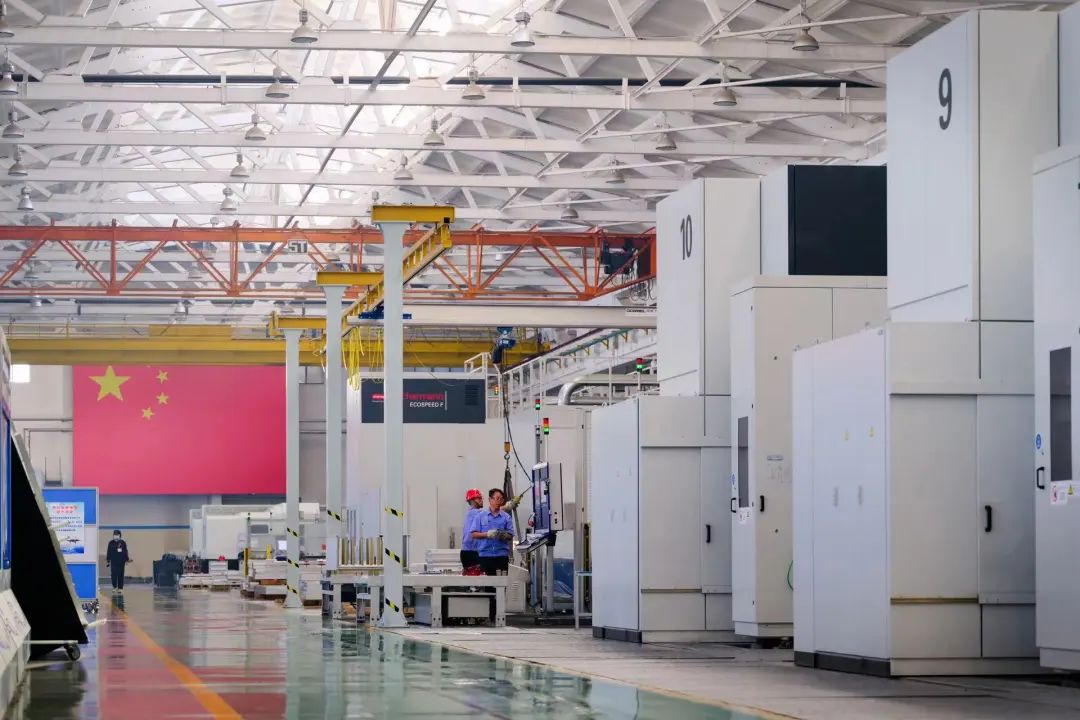
建立数字化柔性机械加工中心群,实现集约高效生产。引进十台数字化柔性机械加工中心,并按照机床型号分成三组组成加工中心群,按照下达的生产计划由轨道机器人将指定的备用方箱及其毛料运送到加工中心进行零件生产,再进行抽真空负压吸附。加工中心运用传感器和内置芯片等技术,实时采集生产设备的运行状态和加工参数。通过建立数字化柔性机械加工中心群,人员节省率为70%,人均零件年产出量由原来的309.85件/人,增加至634.35件/人,增长率达104.73%。
多系统数字化技术融合,实现生产流程智能管理。建立铝屑回收管道智能系统,年节约成本在200万元以上。建设自动物流系统,各个操作站点间的运输通过物流自动引导车完成,在零件物流转运时,自动引导车自动运行到指定位置,有效节省人力及人员移动距离。应用数字化测量系统,对于复杂零件或大型零件的单面80个点位的测量,操作时间由传统做法的2天缩减至30分钟。建设数字化绿色表面处理生产线,实现生产前模拟运行、生产中自动控制以及生产后回放追溯等功能,对于不同零件的表面处理要求、工艺时间能够精准控制,同时与数字化柔性机械加工中心群联动排产,科学合理地控制上下游工序间的生产节拍。
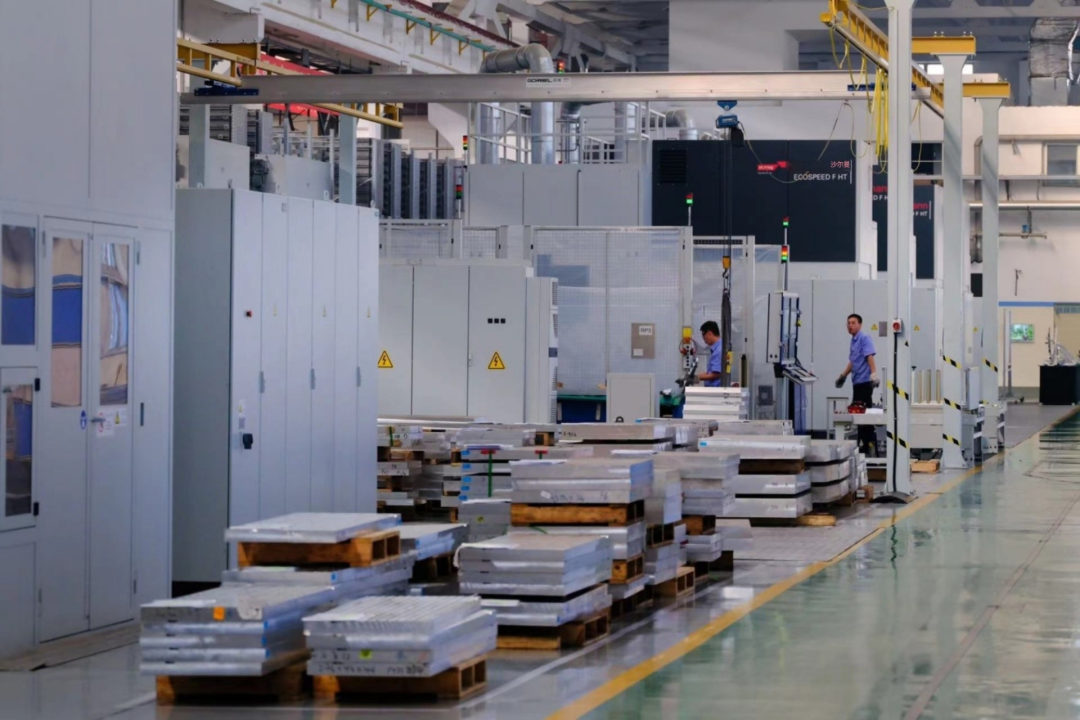
建设中央监控平台,统筹设备及生产运行管理。利用数字孪生技术开发虚拟现实中央监控平台,将数字化柔性机械加工中心群、轨道机器人、零件立体库、铝屑回收系统、物流自动引导车、真空泵、数字化零排放表面处理生产线等设备设施集成到中央控制服务器,通过平台统筹运行管理,并对实时加工过程、虚拟世界、BI看板等信息集中展示,实现了设备设施的运行参数、状态和生产过程信息系统呈现,以零件生产全流程可视化、实时化和数字化,引领产线综合管理效能提升。
以科技创新为核心,推动传统产业绿色转型升级,是实现航空制造业绿色低碳发展的关键。中航工业沈飞通过引进、应用先进信息技术和自动化设备,显著提升生产效率,优化产品质量,为转型发展持续注入新动能,加速推进绿色化制造。
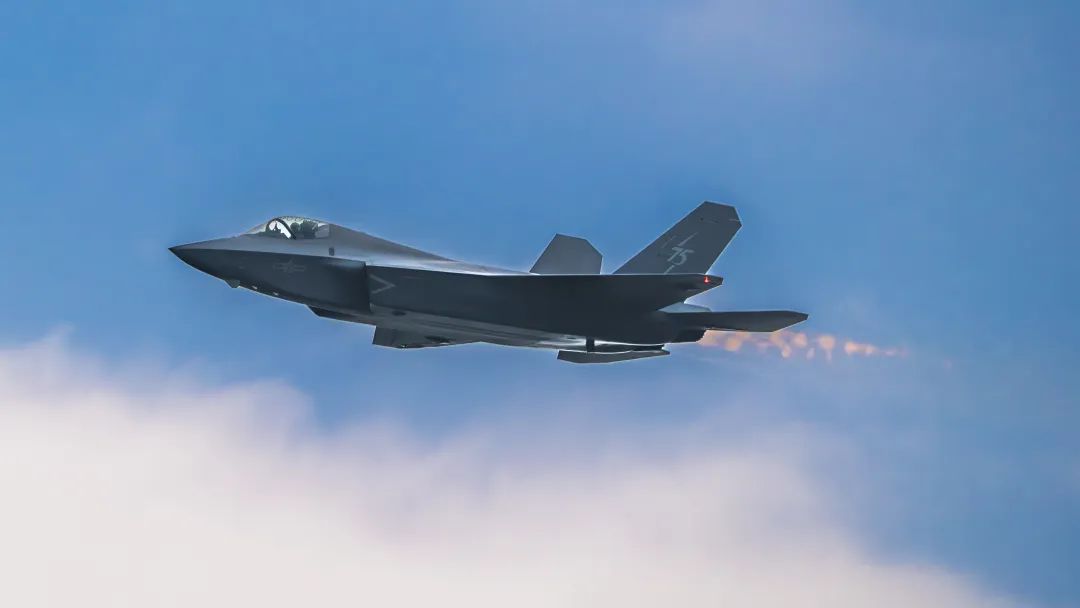