手机显示屏从手机诞生开始就是不可或缺,只是从以前的显示数字,短信文字到现在将书籍,音乐,视频,游戏等等呈现给用户,特别是随着现在大型的手机游戏的流行,用户对手机屏幕的要求也越来越高了。因此手机屏幕材质从当初了UFB、STN进化到现在的TFT、SLCD等等。
不过毕竟屏幕材质实在够多,而消费者对它们的优缺点也不能一一了解,本文先通过对目前九大手机屏幕材质的解析,让消费者有一个明明白白的消费观。这九大手机屏幕材质及技术中,除了传统的TFT、OLED等屏幕之外,还有NOVA、AMOLED、Suoer AMOLED、Super AMOLED Plus、IPS、SLCD、ASV等这几年十分流行的屏幕材质及技术,下表总结了这九大类手机屏幕代表机型及优缺点。从表1可知,不同屏幕材质均有其优点及不足之处,关键在于消费者的抉择。
表1九大类手机屏幕代表机型及其优缺点
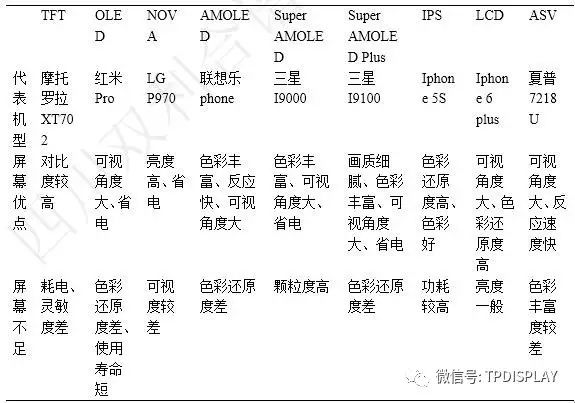
市场研究机构IDC公布的最新数据显示,在2017年第二季度,中国智能手机市场出货量同比下降了0.4%,不过位居前列的国内智能手机厂商均实现了不同程度的增长,华为、OPPO、vivo、小米等四大国产手机厂商所占市场份额继续扩大。
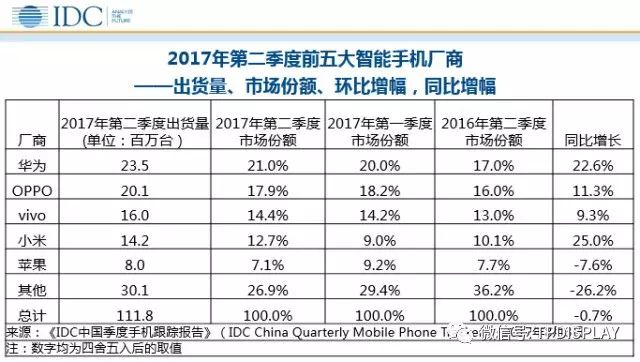
2017年第二季度,华为智能手机出货量实现持续性强劲增长,同比增长约22.6%。OPPO位居第二,vivo位居第三,出货量同比增长分别约为11.3%和9.3%。
在IDC公布的数据报告中,排名前五的手机品牌国产手机就占据了四席,但与市场份额形成鲜明对比的是,国产手机的利润率依旧偏低。市场研究公司Strategy Analytics不久前发布的报告显示,全球智能手机市场今年第一季度的营业利润总额为121.1亿美元。其中仅苹果就占83.4%,而中国手机品牌的利润均不高。
这意味着,尽管国产手机出货量猛增,但并未改变盈利水平不佳的尴尬局面,华为、OV与苹果、三星在品牌溢价能力、供应链把控上存在明显差距。供应链尚且可以通过扩大出货量、不同供应商组合来提升话语权,品牌溢价则取决于产品可圈可点的卖点,技术创新是必经之路,毛利率提升利润自然增加。
换言之,技术驱动成为国产手机品牌重建的良机,尤其是如今手机硬件同质化严重,产品创新已无法通过外界整合获取,自主研发是唯一出路。这也就解释了,去年下半年以来,国产厂商纷纷走上拉升品牌形象、提高旗舰机售价之路,离不开发掘新技术的重要支撑。
近年来,智能手机的市场发展势头迅猛,设计同质化严重,成为手机厂商面临日渐棘手的问题。为引领行业潮流,厂商们必须在上游领域中核心部件的开发上寻求突破,屏幕自然是最好的竞品之一。继小米推出MIX,2017年 3月三星发布屏占比高达84.15%的Galaxy S8,在2017年下半年,将有以下9大品牌的20款产品搭载全面屏。
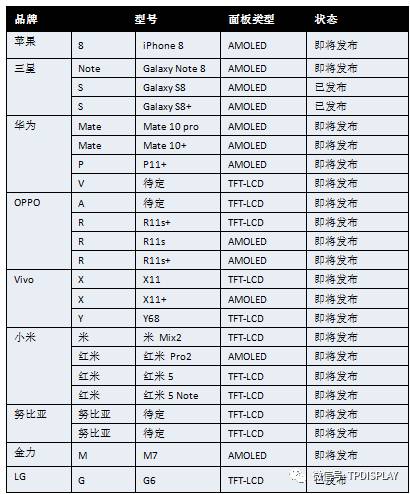
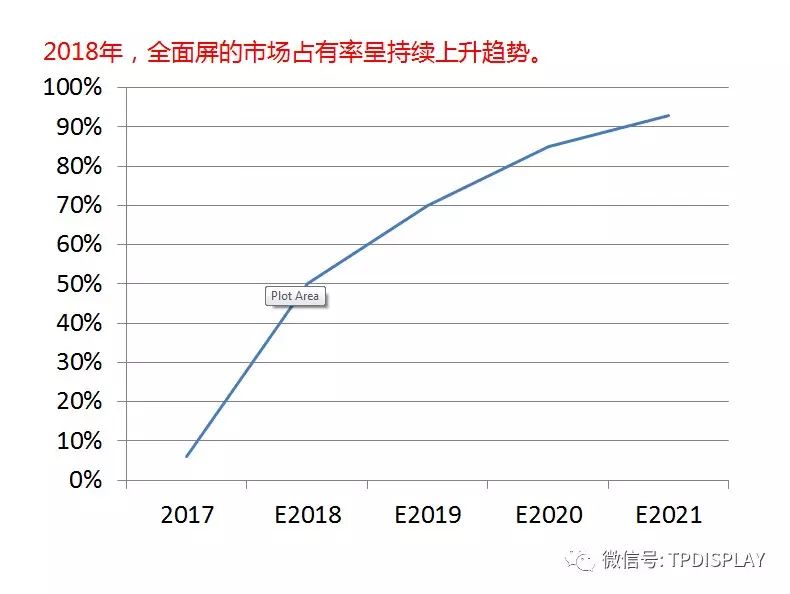
a-Si-TFT LCD
17年, a-Si面板走俏,其原因是一些低端机项目为了快速导入全面屏,在不改变结构设计的前提下,直接将手机两端拉长以容纳18:9屏幕,外加韩系厂商LGD和三星SDC于2016年关停了多条a-Si产线,加剧了a-Si产能紧缺。
但因为a-Si面板电子迁移率较低,每个子像素都需要独立的栅极(Gate IC)驱动走线,两边的BM(无法显示区域)最多控制在1毫米,影响美观。另外受到成本因素的制约,双栅线路的成本无法接受,代表着屏幕无异型切割,摄像头、IR等设备只能堆砌在屏幕之上,而同样因为成本原因,源极驱动仍将采用COG,多种因素相加,在强行保证18:9比例的情况下,手机的外形会变得很长,影响美观。
所以采取a-Si面板的全面屏方案,被认为是异性切割、COF产能不足情况下的无奈之举,不会成为市场的主流。
LTPS-TFT LCD
由于Apple转单AMOLED,造成JDI和Sharp大量的LTPS产能闲置。同时华星光电月产能3万片的LTPS 6代线与2016年下半年实现量产,且价格策略较为激进,进一步加剧了供大于求的市场局面。
但LTPS在全面的电子迁移率较高,所以各个像素点的驱动电压也较低,可以将3个子像素合并一组用一根配线连接到IC上,这样LTPS只需要a-Si 1/3数量的栅极走线即可。在必要的时候,也可以将2根线路重叠设计,中间用绝缘层隔绝开来,进一步节省布线空间,从而有效减小左右BM区域(无法显示区域)宽度。
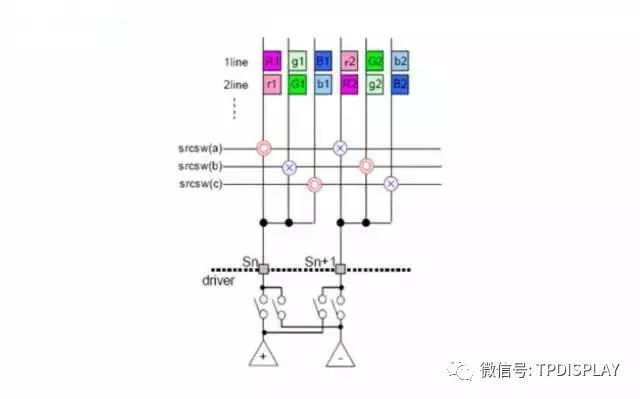
随着异型屏切割及COF功能在2017年7-8月的逐渐展开, LTPS市占率上升的势头将不会改变。
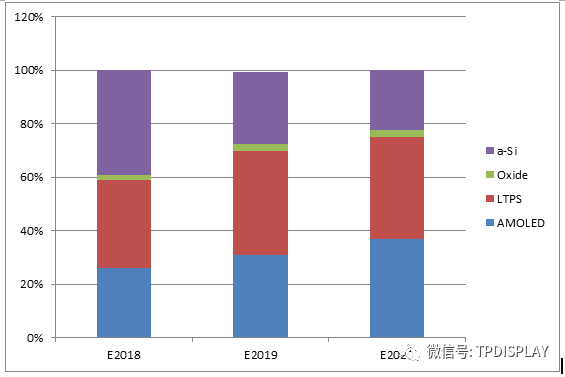
AMOLED
AMOLED是全面屏技术最为理想的实现平台
1)OLED为自发光,不用担心BM(遮盖漏光)区域漏光,同时可以进一步减小组装的预留公差,从而使得BM区域进一步变窄。
2)柔性OLED屏幕的下端子区域也较短,易于实现窄边框设计。
3)最后,柔性基板的机械应力非常小,异形切割难度小,速度快,良率高。在异形切割方面,相比LCD和硬屏OLED有天生的优势。随着国内京东方,和辉光电、维信诺,天马AMOLED技术的逐渐成熟,AMOLED在全面屏领域的市占率将呈现稳步上升的态势
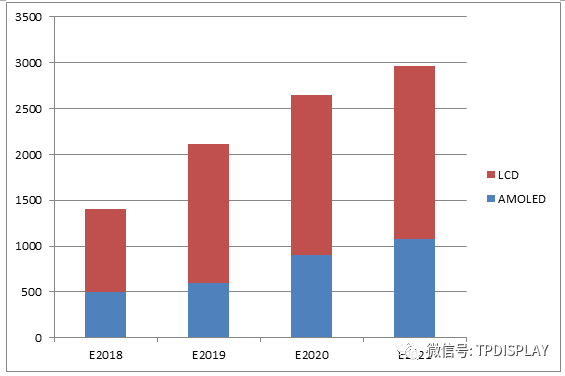
模组段自动化设备
模组段工艺将封装完毕的面板切割成实际产品大小,之后再进行偏光片贴附、控制线路与芯片贴合等各项工艺,并进行老化测试以及产品包装。一共有牵涉到14种设备。
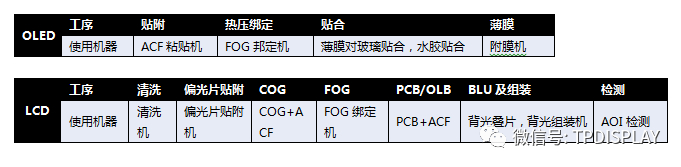
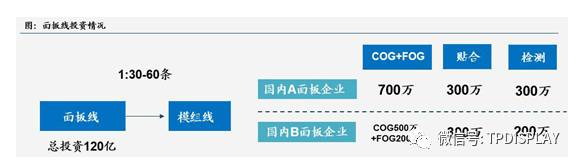
后端模组设备占总项目投资10%,一条面板线对应30-60条左右的模组线,每条后段模组线的投资是2400万左右。
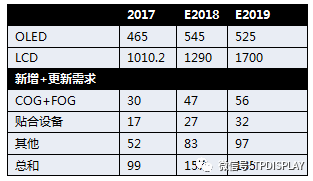
考虑到存量设备的更新和新设备投资规模,2017-2019年AMOLED+LCD模组设备的市场容量为99亿/157亿/185亿,且AMOLED的良率较TFT-LCD低很多,因此AMOLED模组设备的单价比LCD至少高30%。
18:9全面屏成为手机市场新热点
虽然手机大小的提升受限,但并不能阻止手机厂商创新的脚步。如何在有限大小的手机上实现四面窄边框,提升手机正面面积的利用率,进而推出高屏占比的产品,成为当下各大厂商竞争的焦点。
从屏占比角度来看,2007年的初代iPhone屏占比仅为50%左右,后续几年内,手机屏占比在持续提升,但提升幅度不大。通过CINNO Research提供的数据可以看出,在过去几年里,16:9的屏幕比例成为智能机标准屏深入人心,该方案的好处是可以在手机上下端留下足够的净空,用以放置摄像模组、指纹识别、Home键等;但缺点也很明显,手机正面的面积利用率不够,屏占比很难突破75%。
机遇与挑战并存
从5月份开始,国内手机品牌商几乎所有的新设计机型均已全线转战全面屏。有相当多的国内厂商此前已经开了16:9的模具,但由于全面屏的兴起,不得不调整开发计划,重新按照18:9全面屏设计。可以预见的是,由于各大厂商的重视,全面屏手机的开发节奏将会持续加快,全面屏的资源也会越发抢手,预计17年Q4 - 18年Q1,全面屏手机就会大批量集中上市。
从智能机面板的维度来看,2017年,全球全面屏面板的总出货量预计为1.39亿块,其中AMOLED全面屏面板的出货量将达到1亿块,LCD全面屏面板的出货量约3900万块;而2018年全球全面屏面板的总出货量增长至14亿块;2021年几乎所有的用于智能机的面板都会转向全面屏方案,总量达到29.68亿块。
考虑到智能机面板的出货量一般是智能机出货量的1.6倍。其中渠道和厂商囤货,生产过程中的损耗,维修市场三大块分别占总出货量的10%,25%,25%。所以从智能机维度来看。预计2017年全面屏手机出货量为8700万台,2018年全面屏手机出货量为8.75亿。
目前,全面屏在结构设计、摄像头、听筒、天线设计、软件UI、指纹识别、工艺设计、光距离传感器等方面都面临着相应的技术挑战,每一次技术变革,都将是行业重大的机遇,全面屏显示技术的到来,必将在手机制造产业链里造就一批明星企业。而全面屏玻璃的设计、摄像头小型化、听筒小型化、新型指纹芯片的随着全面屏而进行的演变也将会引发整个手机产业链的变革。
窄边框方案是全面屏的基础
(一)减小BM区域的宽度可以实现窄边框
从手机的正面看,从外向内依次是将整个机身包裹在内的金属中框;显示屏的可见部分,即可视区域(VA,Viewing Area);显示屏内实际可用部分,即有效区域(AA,Active Area),VA和AA之间是黑边,即BM区域(Black Matrix)。全面屏的实现,需要最大程度减少BM区域的宽度,从而实现窄边框,提升屏占比。
从结构来看,BM区域主要包括边框胶和驱动电路排线,边框胶用于液晶屏封装,防止液态的液晶分子流出;驱动电路排线区域顾名思义,用于放置传输屏幕驱动电路控制信号的走线。
除此之外,BM区域还可以用来阻挡背光模组的光线,由于背光模组最上层是扩散膜,光线通过扩散膜会散射形成均匀的面光源,而非直射光源。如果手机屏幕组装时误差较大,BM区无法有效遮挡的话,屏幕点亮时边缘位置就会出现明显的光晕。
(二)点胶工艺的进步有助于减小BM区域宽度
从手机面板的结构来看,一块典型的显示屏包括液晶面板和背光模组两部分,其中液晶面板中的液晶位于上基板(CF滤光片)和下基板(TFT)之间。由于常温下的液晶呈现液体状态,可以自由流动。所以为了限制液晶的活动区域,需要用边框胶将其封装起来。
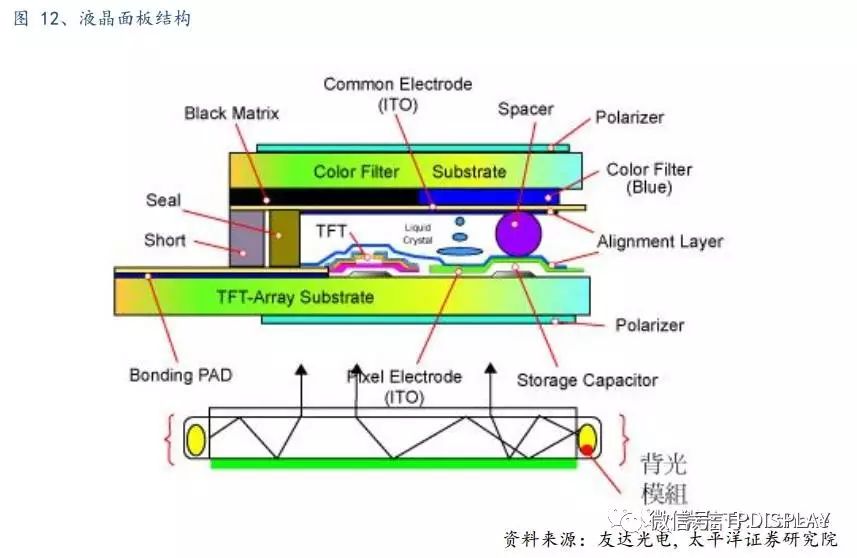
边框胶的主要成分是环氧树脂。当前主流的边框胶宽度一般为0.5mm。为了适应全面屏的趋势,各大面板厂推出了0.3mm胶径的产品,大幅度减小了边框胶的宽度。但其生产难度也随着增大。
在液晶面板的生产过程中,液晶分子的滴入和边框胶的涂布是同时进行的。由于边框胶的宽度越来越窄,对点胶工艺的精度提出了较高的要求,同时液晶分子的滴入准确度也越发重要。如果滴入不准确的话,容易刺穿还没有固化的胶水。另外,胶水的粘度也需要提升,这样就可以利用较窄的胶水来固定液晶分子的流动。
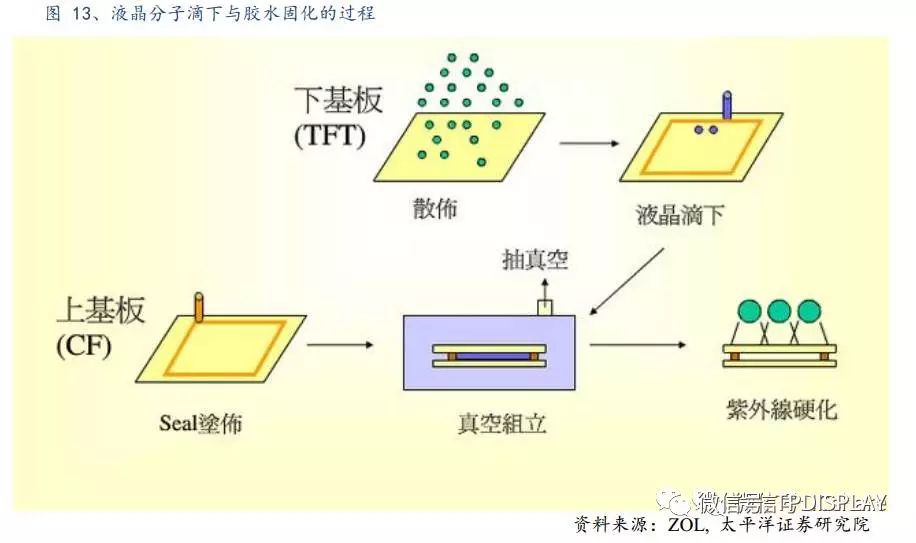
而对于OLED面板来说,同样需要边框胶来实现密封封装。OLED生产流程是在基板上制作电级和各有机功能层,然后功能层上方加置盖板,并在盖板内侧贴附干燥剂,再通过密封胶将基板和盖板相结合。
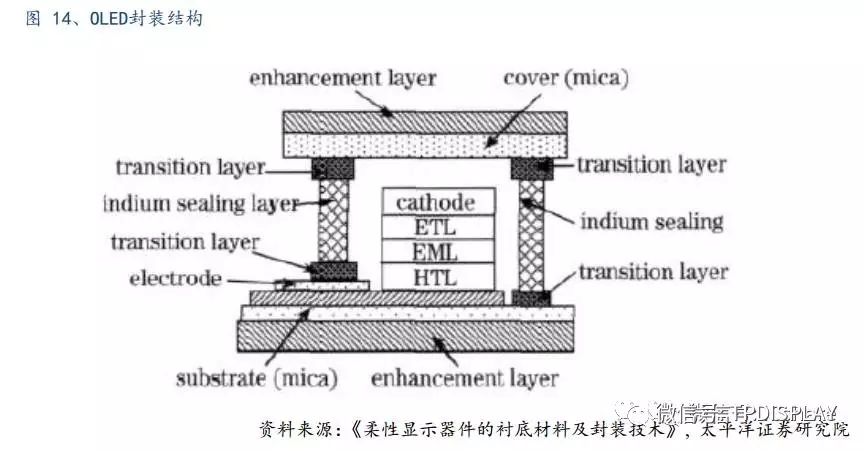
(三)栅极驱动芯片新技术减小左右驱动电路区域宽度
从液晶面板的成像原理来看,液晶面板的运作受到栅极和源级电压的共同控制。栅极电压负责开启和关闭具体某个像素点下方的TFT晶体管,从而影响像素点的亮灭。随后源极电压给像素点所处的液晶区域充电,影响液晶分子旋转角度,进而影响像素点的灰度。再通过彩色滤光片来实现彩色图像的输出。
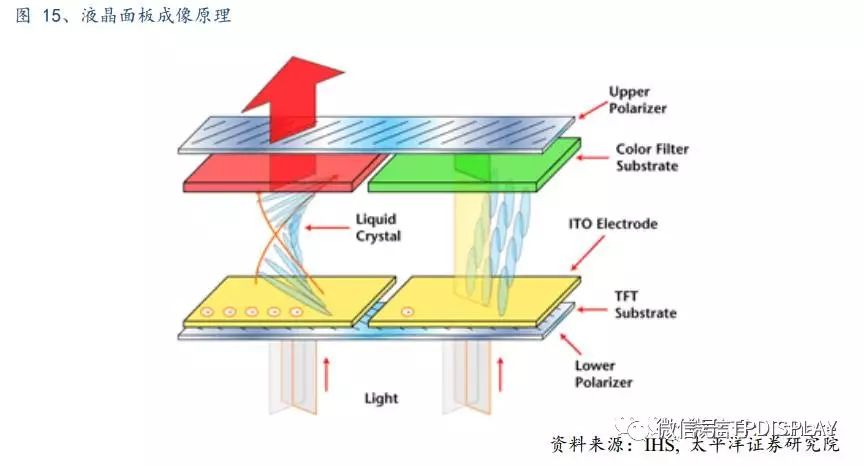
相应的,传统的液晶面板驱动IC也分为两种,栅极驱动芯片(Gate Driver IC)和源极驱动芯片(Source Driver IC),Gate IC 主要负责TFT的打开和关闭。而Source IC负责控制像素点的灰度。由于驱动芯片要同时传输多个信号,所以从外型上看是长条形,位于屏幕侧边。其中Gate IC一般位于面板左右BM区域里,而Source IC位于面板端子区。随着消费电子对窄边框需求的持续升温,Gate IC占据了宝贵的边框面积成为了面板厂亟需解决的难题。
(四)COF方案可以减小面板端子部长度
此前讨论的GOA方案可以有效减小面板左右两边的BM区域,而面板端子部的结构会更加复杂一些。面板端子部除了边框胶之外,还有连接源级和驱动IC的斜配线;Source IC;以及FPC Bonding区。目前这三者的宽度均在1.5mm左右,而边框胶的宽度一般为0.5mm。所以,如果采用当前主流的COG(Chip On Glass)封装方式,将Source IC直接邦定到玻璃上,面板端子部的边框一般在4-5mm左右。
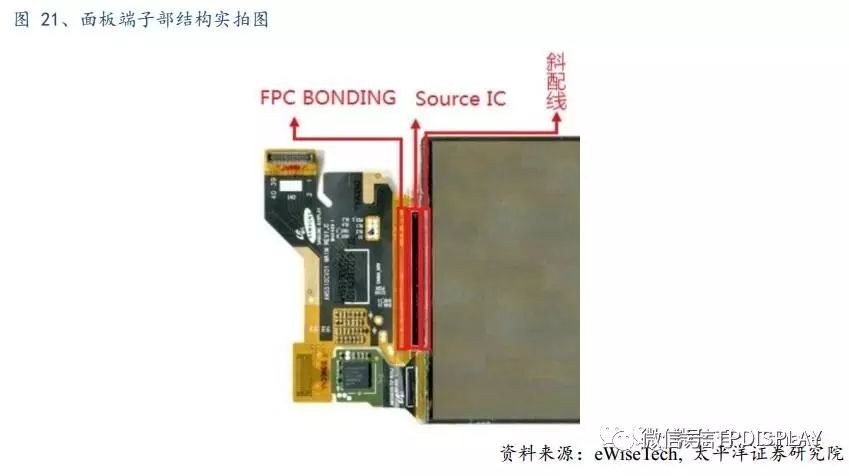
由于Source信号要分256个灰阶,比较复杂,所以无法像GOA技术一样把Source IC整合到TFT 阵列基板中。为了缩减BM区域宽度,面板厂商开始采用COF(Chip On Film)方案,将Source IC封装到FPC上,再将FPC弯折到玻璃背面。相比IC在玻璃上的COG技术,COF技术可以缩小边框1.5mm左右的宽度。
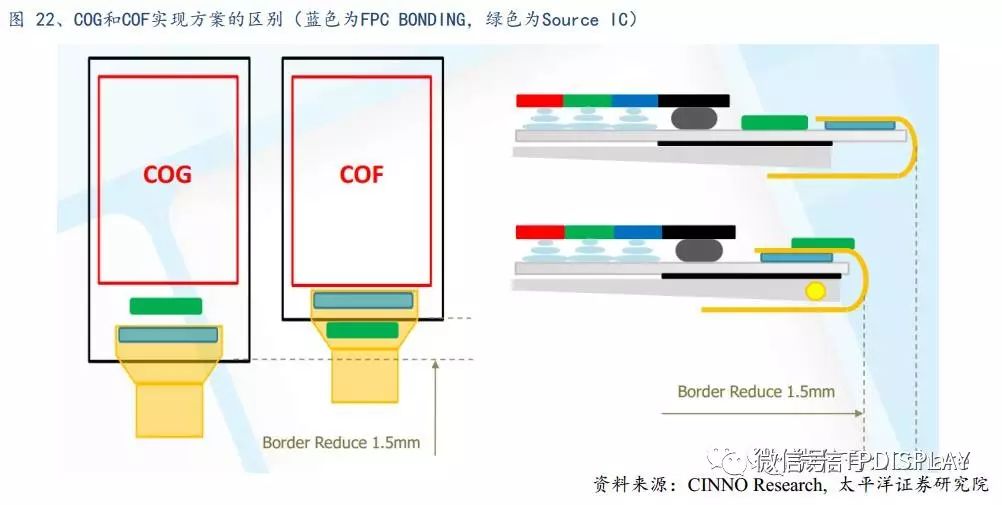
COF方案所用的FPC主要采用聚酰亚胺(PI膜)混合物材料,厚度仅为50-100um,线宽线距在20um以下,所以在FPC生产过程中要采用半加成,或者加成法工艺。目前COF封装用的FPC主要是台系厂商供货,如易华电等。而国内厂商如景旺电子,合力泰子公司蓝沛也有相关技术积累,后续有望受益于COF方案的进一步推广。
COF封装则是采用自动化的卷对卷设备生产。下图是典型的COF卷对卷生产流程示意图,产线左右两边都是PI膜卷,PI膜通过自动封装机台从左往右传输,自动封装机台下方会被持续加热至400摄氏度。芯片被压放在PI膜上之后,芯片下方的金球会和PI膜中的引线键合,这一过程被称为内侧引线键合(ILB, Inner Lead Bonding),随后芯片会通过环氧树脂封装起来(Sealing Resin流程),并涂上阻焊层(Solder)进一步保护IC,后续将其他周边元器件也通过ILB键合并封装在PI膜上。经过这一流程COF就生产完成了。由于COF卷对卷生产过程中需要加热,而PI膜的热膨胀系数为16um/m/C,相比芯片的2.49 um/m/C而言,较为不稳定,所以对设备精度要求很高。COF封装是台系厂商主导,颀邦科技,南茂科技主要营收均来自COG和COF。而近期上达电子和常州欣盛的设厂也宣告了COF生产本土化的开始。期待后续更多的国内厂商形成突破。
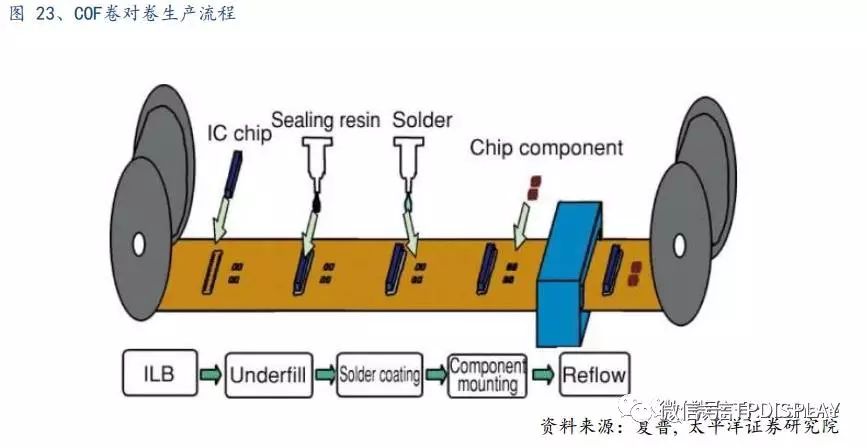
封装完之后,待模组工厂取得封好的FPC卷,会用冲裁(Punch) 设备将PI膜裁成单片,再将FPC和面板邦定。目前各大面板/模组厂已经开始布局相关产能,但业内主流方案依旧是COG。
从设备角度看,目前封装和邦定的成熟设备方案主要有ASM的COF902,FOF902,CPL100等设备,国内相关设备尚未成熟,良率较低。后续COF方案的普及和推广还需要等待国产设备跟进。
(五)LCD面板方案的革新助力窄边框实现
目前,TFT面板的主流方案有a-Si,IGZO和LTPS三种,其中a-Si方案最为成熟,成本优势明显,但是由于该方案的电子迁移率较低,为了驱动各个像素点所在的TFT打开和关闭,需要把栅极电压升到40V以上才能正常工作。所以a-Si方案难以应用在高解析度、高亮度的面板上。而铟镓锌氧化物(IGZO)材料的电子迁移率是非晶硅的25倍,低温多晶硅的电子迁移率是非晶硅的100多倍。所以相比之下可以支持更高解析度的屏幕。
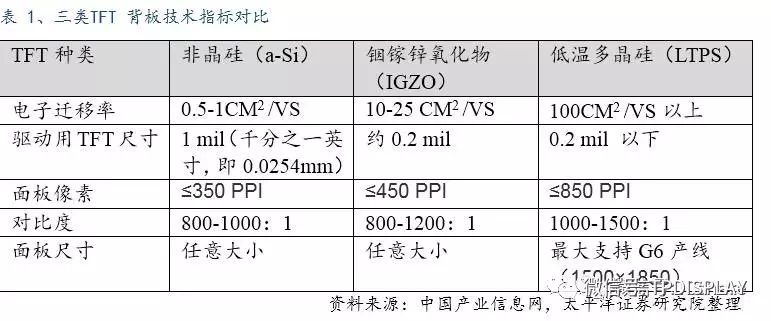
在a-Si的方案里,为了保证稳定的电压控制,每个子像素点都需要独立的栅极走线,会占据较大的左右BM区域宽度。而LTPS的电子迁移率较低,所以各个像素点的驱动电压也较低,在具体设计电路时,可以将3个子像素合并一组用一根配线连接到IC上,这样LTPS只需要原来1/3数量的栅极走线即可。在必要的时候,也可以将2根线路重叠设计,中间用绝缘层隔绝开来,进一步节省布线空间,从而有效减小左右BM区域宽度。
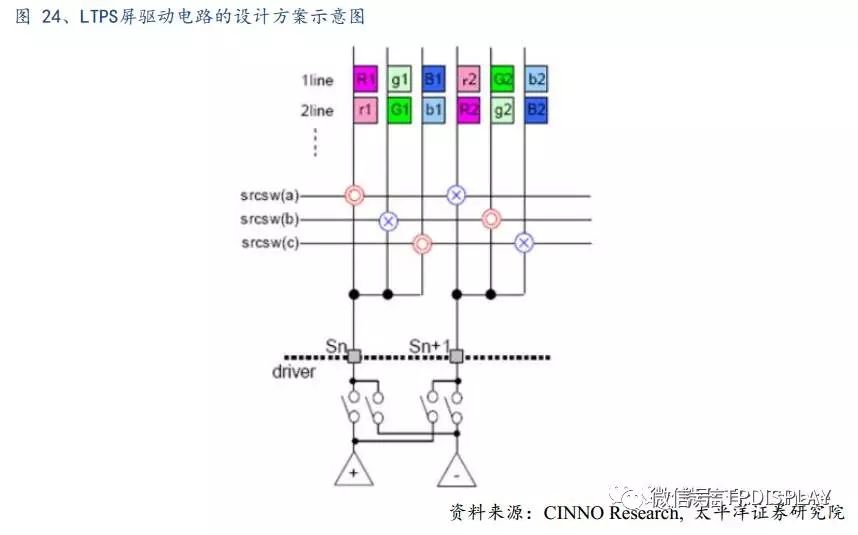
由于LTPS方案在LCD屏上的应用优势明显,未来市占率有望持续提升。根据CINNO Research的预测,2017年LTPS的全球市占率将会提升至33%,而2020年则会进一步提升至38%。
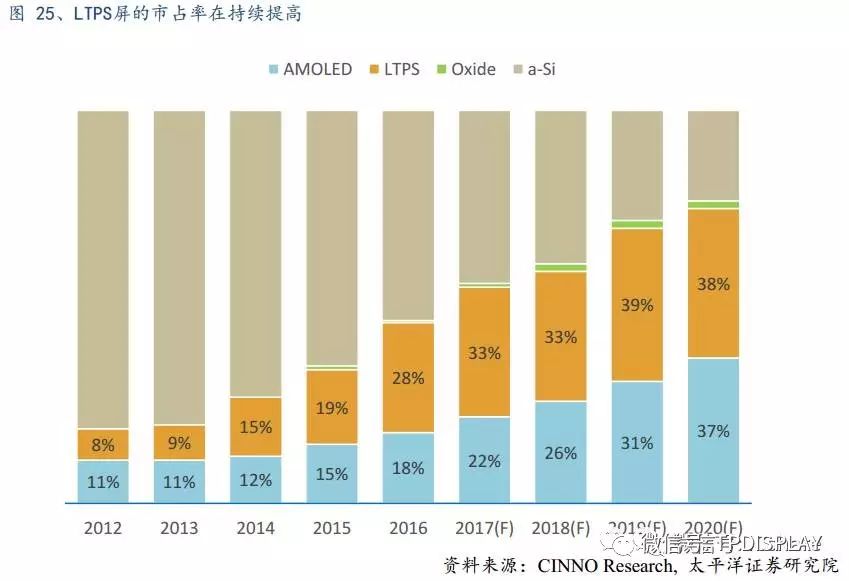
而目前,受制于成本以及开发进度等原因,目前各大面板厂开出来的全面屏资源主要规格是1mm的左右边框,以及4.5-5mm的端子区。且a-Si + COG方案居多。
三、全面屏异形切割,激光设备是关键
传统的16:9的手机屏幕呈长方形,四边均是直角,由于要在机身上放置前置摄像头,距离传感器,受话器等元件,所以屏幕和上下机身边缘均有一定距离。而18:9的全面屏手机的屏占比一般都会大于80%,屏幕边缘会非常贴近手机机身。如果继续沿用此前的直角方案,会无处放置相关模组和元件,同时,屏幕接近机身会让屏幕在跌落时承受更多的冲击,进而导致碎屏。
因此对屏幕的异形切割十分必要。一方面要在屏幕四角做C角或者R角切割,同时通过加缓冲泡棉等进行边缘补强,以防止碎屏。以另外一方面需要在屏幕上方做U形切割,为前置摄像头,距离传感器,受话器等元件预留空间。
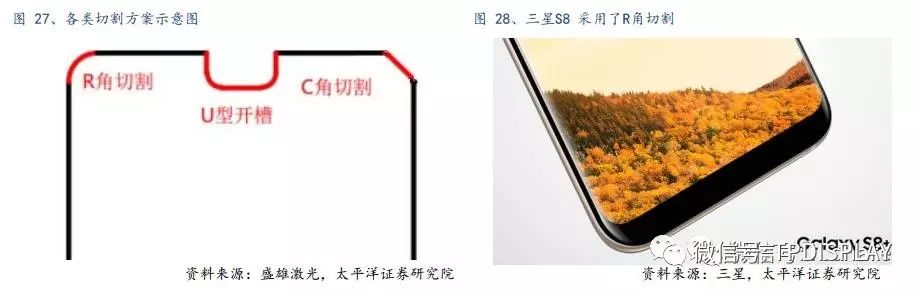
当前的异形切割方案主要有:刀轮切割,激光切割,以及作为临时替代方案的CNC研磨。其中刀轮切割是最为传统的切割方案,成本低,一般用于直线切割,精度在80um左右。刀轮切割的具体流程是先用刀轮在玻璃上划出切口,再通过裂片机完成裂片。
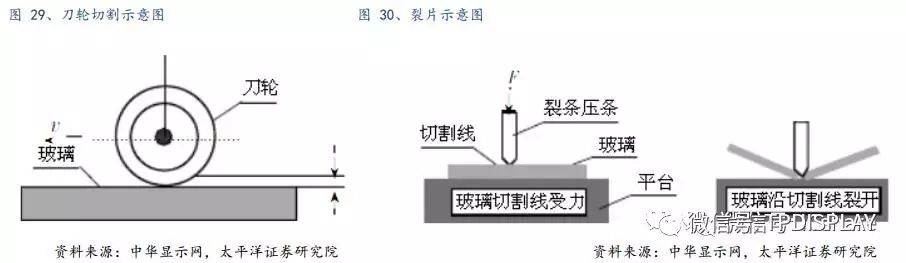
目前异形切割的主流方案是在屏幕面板上切两个C角,两个R角,一个U槽。该方案里主要是圆弧切割,如若采用刀轮切割方案,则崩边严重。同时刀轮切割的效率低下,通过产业链调研得知,由于刀轮切割需要预留切割线,相比激光切割,刀轮切割对于整个Panel的利用率会下降10-20%;切割一片需要2-3分钟。所以在短暂的尝试之后,刀轮异形切割已经逐步被业内淘汰。
相比之下,激光切割在异形切割方面的优势明显,激光切割是非接触性加工,无机械应力破坏,且效率较高。同样的两个C角,两个R角,一个U槽的加工方案,20秒左右就可以完成切割。
激光切割的原理是将激光聚焦到材料上,对材料进行局部加热直至超过熔点,然后用高压气体将熔融的金属吹离,随着光束与材料的移动,形成宽度非常窄的切缝。激光切割的精度可以达到20um。
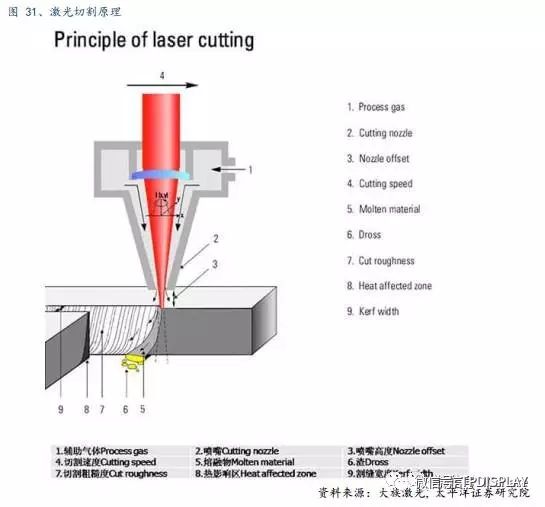
激光器的分类较多,从增益介质来看,分为固体和气体。其中,固体激光器包括Al2O3,YAG切割等,气体激光器主要有CO2切割等。一般而言,气体激光器一般为10.6um波长的红外光,使用范围较广,固体激光器一般为1064nm波长的红外光,输出能量大,峰值功率高。同时,除了波长较长的红外激光器之外,还有一种固体紫外激光器(波长从180到400nm),紫外切割更多用于处理聚合物材料,通过破坏非金属材料表面的分子键,来实现切割,紫外切割也被称为冷激光,热效应较小。
从激光器的脉冲宽度时间来看,又分为纳秒(ns,10^-9秒)、皮秒(ps,10^-12秒)和飞秒(10^-15秒)等。脉冲宽度约短,峰值功率越高,热效应越低。
从切割方案角度来看,激光切割又分为表面消融切割和内聚焦切割,表面消融切割可以直接切透,不需要后续增加裂片工序,热影响区域大;而内聚焦切割后需要裂片分离工序,热影响区域小。
通过产业链调研得知,目前主流的激光切割机型是红外固体皮秒激光器,采用内聚焦切割方案。该方案在成本和效率之间取得了最大的均衡。国内的面板激光切割设备厂商主要有:大族激光,盛雄激光,德龙激光,国外厂商主要是日本平田。

通过产业链调研得知,国内各大模组厂均是在4-5月之间开始局部COF以及异形切割设备,由于目前设备交期是2-3个月,再加上验证和测试的3个月,我们预计国内的COF和异形的产能将在2017年Q4释放。但由于目前异形切割的需求较为旺盛,所以有较多厂商选择用CNC研磨的临时替代方案加工面板。
同时从面板角度来看,由于引入了U形槽切割,使得栅极控制信号传输到切割处就中止,所以需要在模组生产过程中就引入左右双栅极控制排线。由于各款手机的U形槽大小不一,面板厂和手机品牌商/手机ODM厂商的定制化合作会成为大趋势。
投资建议
需求旺盛叠加供应不足,面板将长期供不应求:全面屏时代的来临,对面板行业最为直接的影响就是面板需求量明显提升。在同样大小的手机里,18:9的屏幕比例相比16:9的方案,屏幕的尺寸会提升约10%左右。对面板的需求量也同比例增多。从供给端角度分析,由于韩系厂商LGD和三星SDC于2016年关停了多条a-Si产线,加剧了a-Si产能的紧缺。下游需求旺盛、上游产能紧缩,致使a-Si面板供不应求的态势在较长的时间周期内都会成为业内常态。
新工艺流程增加面板和模组厂的获利空间:对于面板厂而言,为了实现四面窄边框,需要改进点胶工艺,采用GOA方案。这会在一定程度上推升面板的单品ASP;对于模组厂而言,由于COF和异形切割均需要购置新设备、对已有产线做较大改造。所以国内的COF和异形切割的产能在2017年Q4才能得到释放。通过产业链调研得知,采用异形切割方案的显示模组ASP相比传统方案提升20-30%。抢先布局的厂商将占得先机。
工艺改进,材料设备抢先受益:对于四面窄边框的全面屏方案而言,COF和异形切割都十分必要。COF方案所用的FPC主要采用PI膜材料,厚度仅为50-100um,线宽线距在20um以下,FPC生产过程中要采用半加成、或加成法工艺。景旺电子以及合力泰的子公司蓝沛均有相关的技术积累,后续有望在COF领域实现突破;异形切割需要在屏上做C角,R角以及U形切割,目前主流的激光切割机型是红外固体皮秒激光器,采用内聚焦切割。