ISO9000 2015版相对于以前的版本来说,更加强调风险识别和风险控制,如何将这种思想与广大质量人员平时的工作相结合,在实践中成功落地?笔者认为其中的关键是将风险识别和控制与过程管理相结合,本文用一个PCBA外协批次性加工不良阐述这种方法。
2017年6月9日,我公司维修人员在维修甲产品时发现有3个产品的不良现象均一致,其产生原因是其中的M1板D34和Q15引脚与本体碰到一起短路(如图)。
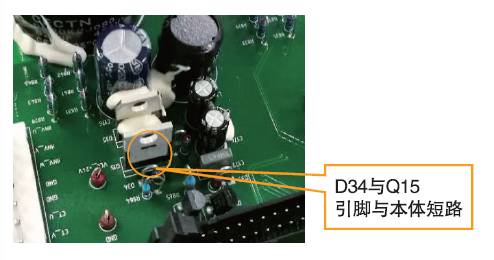
维修主管立即将此问题反馈给我,作为品质总监,我立即要求下属的主管封存此批产品,并要求外协加工厂B派人前来我司,配合我司品质人员,对甲产品和M1板全部进行排查和返工处理。
返工过程中发现在待出货的库存成品中有5台机器均存在同一问题,从外协PCBA加工厂回货的M1板也有7片存在此不良现象。
返工完成后,我要求外协品质工程师填写《纠正预防报告单》发给外协厂B,要求其在一周内针对此作业不良进行分析,并提供正式的《纠正预防报告》。
说到这里,我给大家先介绍下ISO9000质量管理体系中关于纠正预防的几个基本概念。
● 纠正:为消除已发现的不合格所采取的措施。
● 纠正措施:为消除已发现的不合格或其他不期望情况的原因所采取的措施。
● 预防措施:为消除潜在不合格或其他潜在不期望情况所采取的措施 。
对这三个概念,许多人都会混淆,就连一些工作数年的质量管理人员,有时也不知道如何才能制定正确的纠正预防措施,并将这些措施落实到位,以彻底消除不良品。
当月13日,外协PCBA加工厂B发来了《纠正预防报告》,我一看,里面的内容无法达到我的要求,于是决定以此案例来对其进行纠正预防方面的质量辅导,确保其能按照正确的思路解决产品质量问题,提升加工质量。
一周后,我去这家外协加工厂,与它的品质、生产、工艺等人员一起检讨本案例中的纠正预防之道。
检讨会上,我说:“此问题出现后,贵司来人与我司品质人员对库存M1单板和甲产品进行返工处理,将不合格品变成了合格品,此为纠正。但是对贵司针对此问题提出的纠正措施和预防措施,我不认可。”
见大家一脸不解,我打开电脑,将其发给我的《纠正预防报告》投影出来,接着说:“贵司认为产生此不良的原因有三:第一,由于D34与Q15距离近,过波峰焊后Q15向D34倾斜,导致短路。第二,点胶员从两个MOS管本体中间点胶固定时,导致Q15向D34方向偏移致短路。第三,检查人员未重视检查发现此隐患,导致不良流出。”
我指着墙上投影出的内容:“你们基于这三点分析,给出了五点纠正措施:1.针对器件D34过炉,做小方块治具进行限位扶正过炉。2.针对Q15\D34两器件,点胶后将其贴紧。3.优化检查作业指导书,针对此项进行重点检查。4.针对问题录入品质履历表,以便后续生产类似工艺及产品时进行预防管控。5.品质部分针对此问题召集会议,通报相关部门检讨,工程、生产、品质后续新品评估时将此工艺列入评估范畴案例集。”
我接着问:“你们认为这样可以彻底解决此问题产生的根源吗?”
这时,这家工厂的品质主管站起来说:“我认为是可以的。”
我说:“D34与Q15在板上的距离的确比较近,但是只要加工正确,是不会互相碰在一起的,问题发生的原因是你们的点胶人员在点胶后将Q15往边上推了一下,才导致二者碰在一起短路。为什么会出现此问题?根本原因是点胶人员点胶后,未查看其点胶动作是否导致其他元件互相碰撞到一起,这是点胶作业的常识性知识,而从此案例来看,点胶员显然不具备此知识。因此,贵司应该编写点胶人员的培训教材,对所有点胶人员进行培训,此类问题才能彻底解决。”
“从过程管理的角度来看,问题产生的原因是贵司的点胶过程管理存在漏洞,人员的操作技能达不到上岗要求,因此纠正措施之一就是建立点胶人员的上岗培训制度,并执行到位。”
“原来问题要这样看。”大家似乎恍然大悟。
“纠正措施的第二点,这个问题在点胶过程出现后,本来应该被后面的检验员发现,但是检验员也没有发现这种批量性的问题,为何?经过我的调查,这款M1板是第一次转移到贵司生产,你们第一次加工就闹出了这么大的问题。”
“二十年前,我还是个制造工程师,当时负责PCBA加工制程的指导,在客户的产品第一次转移到我司生产时,在第一片板子完成加工后,我会对着样品与生产、品质人员进行评审,将所有可能出现的风险点识别出来,制定出一个《××产品加工注意事项》,发给生产和品质人员对这些加工风险点进行重点控制。”
我看了一下所有人,问:“贵司有没有这样的作业流程?”
“有的。”有几个人异口同声地回答。
“显然,你们在这个流程上也没有执行到位。因此,针对本次问题的纠正措施之二就是,将新产品第一次生产后评审的流程做到位,可以由品质人员制定一个实施记录表,如果没有做,检查员必须执行产品入库。”
“因此,本次批次性不良问题的产生主要源自以下两个过程的管理存在漏洞,一是点胶过程,二是新产品第一次生产加工评审过程。如果这两个问题不解决,类似问题一定会继续发生。”
“我们公司对这两个过程的管理的确做得不到位,以前也出过类似的问题,一直想不到解决问题的根本办法。”大家纷纷点头。
“我再说说预防措施,所谓预防措施,是问题还未真正发生时就采取的措施,既然问题未发生,如何采取措施呢?很简单,就是识别出这个产品在生产过程中存在的风险,再针对风险制定出相应的措施,确保风险点不会变成真正的问题。”
“因此,大家应该组织起来,对这块M1板,从来料开始,到半成品出货到我司,中间的一系列过程,进行加工风险识别,找出每个过程中存在的风险点,并采取有针对的措施。比如说,如果识别出本案例中的D34和Q15有碰在一起的风险,我们可以对D34的本位增加热缩套管,这样即使二者碰在一起,也不会产生问题。”
“一句话,所谓的预防措施是针对业务过程中存在的风险而定的,不同产品在加工过程中的风险是不一样的,最新的ISO9000 2015版强调风险识别和风险控制,我的思路与它是一致的。”
经验总结
在我近二十年的质量管理生涯中,遇到过无数的产品质量问题,这些所谓的“产品质量问题”经过调查,其发生的原因只有一个,就是在形成这个产品的一系列过程中,某一个或者某几个业务过程的管理存在漏洞,最后的表现就是产品不良。
如果我们能以过程的角度来看待纠正和预防,就会发现问题的解决会更有效率。而目前众多的中小企业,根本没有建立过程管理体系,在出现产品质量问题时,是不可能有效实施纠正和预防的。
(作者著有《质量总监成长记》一书)

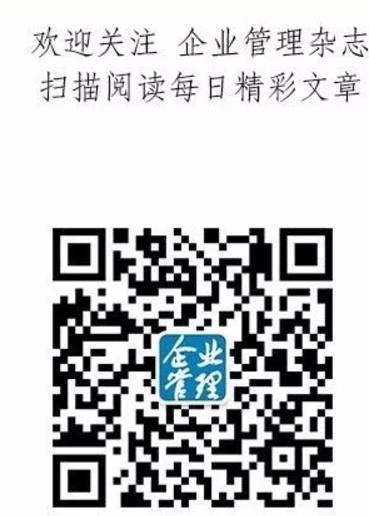