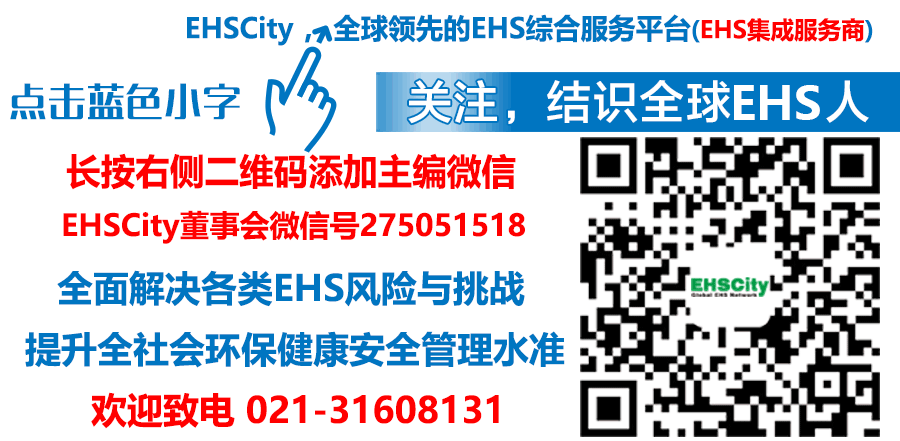
There are close to 200,000
mid-market-sized organizations in the United States and Canada, defined
as having an annual revenue of more than $10 million and under $1
billion, according to the GE Capital 2011 National Middle Market Summit.
Each of these organizations has a plethora of responsibilities and
issues from revenue growth and consumer satisfaction to regulatory
compliance. Perhaps one of the biggest concerns for the mid-market is
employee health and safety.
Mid-market companies employ nearly 25 percent of the workforce, or
around 55 million workers. That’s a huge share of the responsibility to
keep all workers safe and manage occupational risks.
So, how should organization make sure its employees go home safely every day?
The answer here is simple: plan, plan, plan. Don’t wait for something
to happen before you realize that you need to make occupational health
and safety a priority. Don’t neglect employee training and injury
prevention until it’s too late.
Mid-market firms have a major focus on implementing processes and
software for incident management (32 percent) but less focus on managing
and mitigating the risk beforehand (28 percent), according to a recent
study by Verdantix. This is a huge opportunity for improvement, as
managing an incident after it happens often is much more expensive than
taking preventative measures to avoid it altogether.
OSHA encourages all organizations, regardless of size, to implement
an injury and illness prevention program to identify and address
problems before they occur in the workplace. This not only will reduce
the likelihood of a safety event such as an injury, illness or fatality
but also increase employee morale. Employees are loyal and positive
toward an organization that clearly values their safety, leading to
greater productivity and talent retention.
International Standards such as OHSAS 18001 and ISO 45001 provide the
framework for health and safety management systems, but many mid-market
organizations face an array of challenges in implementation.
Limited Resources
In a mid-market company, health and safety typically is one of the
smaller departments, with employees wearing many hats and stretched
thin. With limited human capital, there often isn’t capacity to
implement an effective health and safety program, and the department
becomes reactive rather than proactive.
Those running the EHS department are stuck investigating why a safety
event occurred, rather than identifying and correcting risks
beforehand.
Limited Budget
Verdantix found that nearly half of the CEOs at mid-markets believe
that EHS management is a cost center rather than a potential contributor
to the financial bottom-line. The perceived cost of upkeep is high and
health and safety budgets aren’t prioritized.
With limited resources and limited budget, running a truly effective
health and safety program can be a heavy burden and seem impossible.
With insurance premiums on the rise and with more staff absences being
reported, the perception will need to change from that of a cost center
to that of a cost avoidance center, according to the National Council on
Compensation Insurance (NCCI) and CCH Unscheduled Absence Survey.
Outdated Health and Safety Management Platforms
Many mid-market organizations manage health and safety programs
through a homegrown system using pen and paper, Microsoft Excel or some
other manual tool. These legacy systems can be bulky and complicated,
leading to errors in data reporting, compliance issues and items
slipping through the cracks.
While these potential problems certainly are a challenge for the
mid-market, there is a huge opportunity for improvement through
technology that can mollify the pressure from small departments with a
big job to do.
Software built specifically for the EHS ecosystem can cut costs,
stress and human capital needed for a successful program. With resources
already stretched thin, a fully-automated safety management system
helps departments remain compliant with local and international laws,
ensuring that the program stays in tip-top shape.
By keeping the health and safety department and your employees
automatically notified when issues arise, safety management systems
promote productivity, accuracy and complete communication between
employees and the respective departments.
Business Intelligence
Over 2.9 million non-fatal workplace injuries were reported by
private employers in 2015. Each lost time injury costs approximately
$100,000; employers pay over $1 billion each week for direct workers’
compensations costs. How many of these accidents could have been
prevented with the right information? How much of that information
already exists within a company’s database?
EHS can benefit greatly from a system that utilizes business
intelligence analytics, empowering EHS professionals to easily and
accurately report on their health and safety data to identify trends and
even predict outcomes. The knowledge stemming from these capabilities
ultimately can lead to more informed business decisions that maximize
health and safety.
Time and Money Savings
Investing in a fully-automated safety management system can be a
daunting task. The common perception is that the cost and time to
implement such a system outweighs the benefits, but this is far from
true. With the right system in place, one that is easy to implement and
quick to get up and running, the return on investment most definitely
will outweigh the initial cost and ramp-up time.
Culture of Safety
Employees will feel more motivated and engaged in a company culture
that places a high priority on their safety. With a system that allows
all employees to engage with the health and safety program and clearly
understand the precautions in place, the company can collect more
accurate data collection and promote a safe work culture.
A cost-effective enterprise class safety management system can help
streamline your health and safety program, ensuring that all your
employees arrive home safely every day.
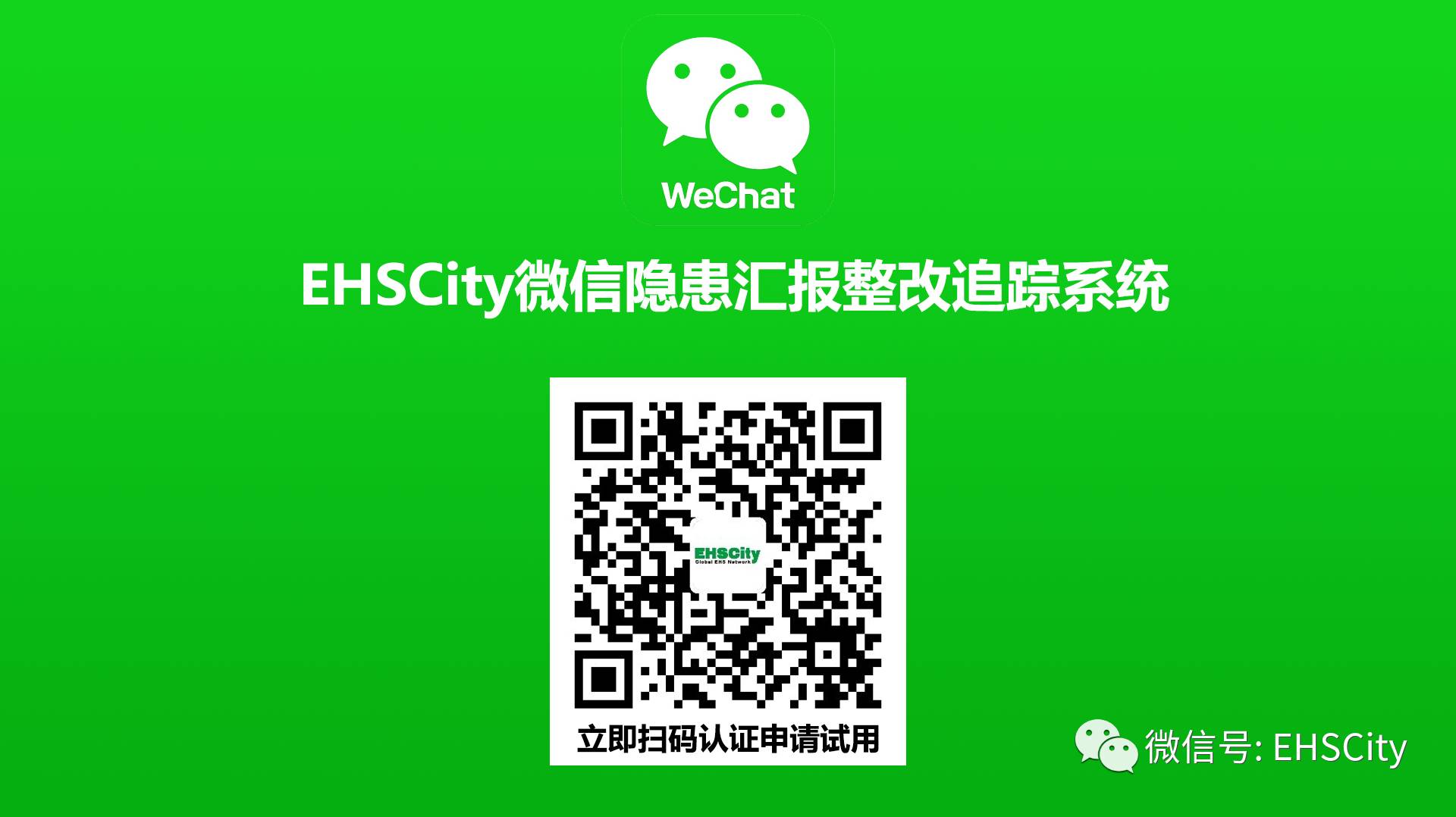
欢迎联系如下二维码,免费试用个人版
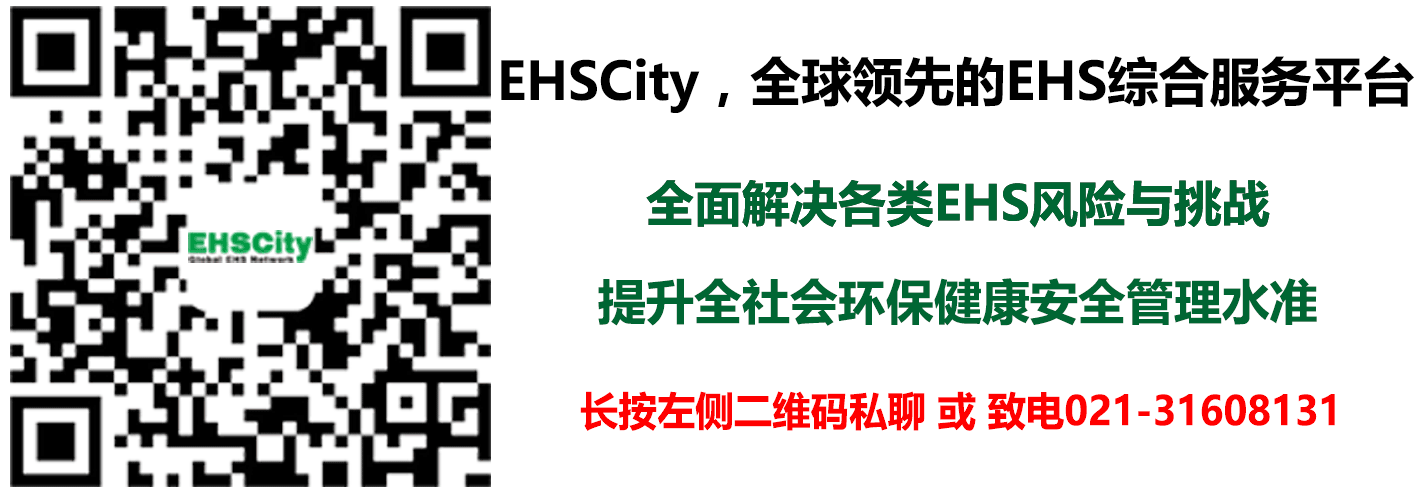