片剂是普通固体制剂中的重要剂型之一,同时压片是制作片剂必不可少且关键步骤之一,小编认为,一个涉及到压片的项目,多多少少会在压片步骤卡壳一下(与负责人工作经验无关),但卡壳的部位又总是那么的似曾相识。为此,小编总结了自己发生的一些经历与感悟
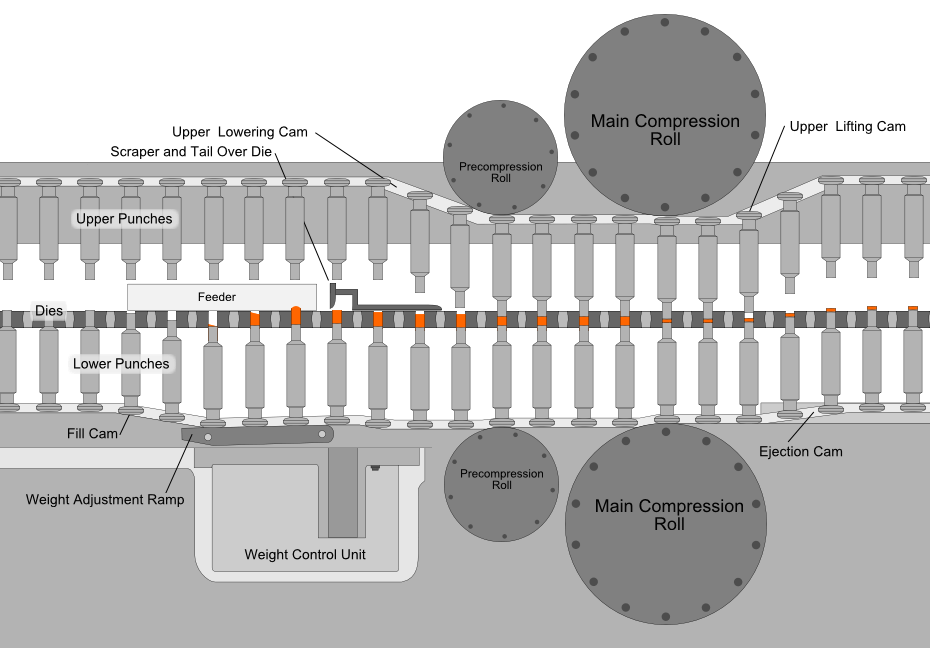
颗粒含水量过高:可在正式压片前检测物料的LOD,这一点对于易吸潮的产品尤为重要,无论是直压的混颗粒或是造粒完后的混颗粒,中间存放过程均有再次吸水的风险;
润滑剂用量不够或未混匀:在处方摸索阶段可考察润滑剂用量及混合时间对产品的影响,如3min、5min、7min等;
室内湿度偏高:对于具有吸湿性物料尤其需要关注室内湿度,可增加除湿设备,将室内湿度降到合理数值,倘若还降不下来,可在压片机转台上加入一定量干燥剂,或在压片前将压片机空转一段时间(注:切不可使用吹风机等设备吹模具)
物料中细粉偏多:可在压片前检测PSD进行评估,细粉太多会使物料与冲头接触的比表面积增大,因此若PSD检测结果显示物料粒径偏小,造粒时可适当增加粒径;对于不能增加粒径的物料,可适当增加润滑剂用量(Mg-st用量过多影响溶出,但硬脂富马酸钠不会)
冲头或中模有水分或其他液体物:这种情况发生概率较小,但小编却遇到过压片机中的机油流到冲头而粘冲的状况,当时是忘记装上冲垫圈。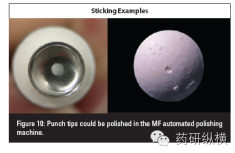
配方因素:粘合剂用量不够或粘度不够;润滑剂用量偏多或混合时间过长,使颗粒之间的粘性降低;处方整体疏水成分偏多,减弱了颗粒间的内聚力和粘性,可适当更换部分成分,如将Mg-st更换为硬脂富马酸钠。
物料因素:含水量偏低,需重新摸索最佳颗粒水分值;或加适量稀乙醇,2-3小时后压片。细粉偏多,细粉多影响可压性,一般呈现的是顶裂(压片前因设备震动等因素,细颗粒处于中模孔中的下端,粗颗粒分布于上端)。
压片参数:压力偏大,或转台转速偏快,一般是腰裂。这两个因素会使中模中的空气来不及排出而裂片。
模具受损或不合格:上冲与中模不配套,或者中模内部磨损。这两种情况应该不会发生,但是好的模具有时确实是如虎添翼,据小编所知,目前国内大部分企业并不关心模具质量因素。
涩冲即压片机在运行时,上下冲不能正常运动,主要的原因是物料与冲模之间的结合力较强,甚至已经发生粘结了。可能原因为物料粘性偏高,或者室内湿度偏高,物料吸附空气中的水分后粘性增加,或者润滑剂用量不够或混合时间偏短。可降低物料含水量、或选用低粘性粘合剂、或增加润滑剂用量(小编用的是增加润滑剂用量)
跳片最可能的原因为转台转速偏快,导致出片时片子与挡板之间的撞击力过猛,从而发生跳片,因此适当降低转台转速即可。
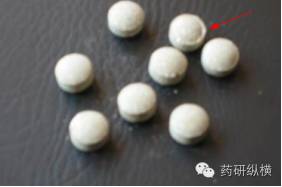
毛边即片子边圈有突出,在小编的工作生涯中就遇到多次,片子边圈多出来的部分有时用手即可使之脱落,最终直接导致片子外观不合格,同时影响片重等质量指标。出现这种原因首先想到的是压力偏大,使片子中间物料压得太实而往边圈跑,因此可降低压力试试。其次是模具磨损,使冲头与中模间的间隙偏大,这种一般用肉眼即可看出缺陷,可拆下模具看看,也可采用更换模具的方式排查原因。也可尝试增加预压。
爆冲是指冲头发生开裂或爆碎,原因为压力过大或上下冲质量不佳。国内仍有部分厂家不关系冲头质量问题,而在实际生产过程中又一味的追究压力指标,难免会有爆冲的风险。
物料粒径相差较大,粗颗粒与细颗粒流速不一,导致中模中物料装量有差异,如粗颗粒较多的可能片重偏轻,细颗粒多的颗粒偏重,在微丸压片中尤为明显。另外,若物料颗粒粗细相差较大,由于高速压片机在运行时机器的震动作用,物料在进入中模中(甚至在料斗中)已发生分层,因此开始压出合格片重的片子在压片机运行一定时候片重会发生改变,这种情况可降低压片机的运行速度,或者重新调整物料的PSD分布。
物料流动性差,导致进入中模中的物料时多时少。可重新调整物料的整体流动性,如改变粒径、加入助流剂。另,小编在此给大家推荐一个秘密武器,圆柱形饲料器叶轮(见图),常用的为长方体的叶轮,据小编所知,目前国内也有厂家有这种配件哦。
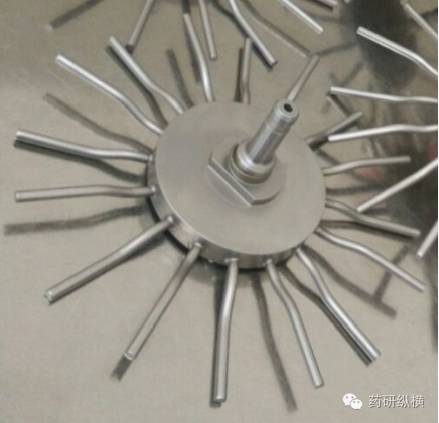
饲料器转速与转台转速不匹配:据小编所知,国内有很多企业仅关注了转台转速的调节,而忽视了饲料器的转速。与转台转速相比,若饲料器转速低,则不能充分发挥饲料器强制饲料的功能,会导致中模孔中的物料不能填满;若饲料器转速过高,则会导致饲料器中的物料来不及运送至中模孔中,从而导致物料在饲料器中二次混合(对于含有Mg-st等疏水性辅料会影响崩解和溶出)。因此,在低转速时应采用较低的饲料器速度,转速增加时饲料器转速也应相对增加。
物料结块,目前做的一致性评价的项目很多属于BCS I或III类,容易吸潮的物料在料斗或压片机其它位置易结块,物料若在料斗中结块会使料斗堵塞或部分堵塞,影响物料的正常流动,使中模中的物料时有时无。这种情况因注意室内湿度、暂时不压的物料要及时清出压片机各部位。
物料快完了:这一点国内很多企业都没注意,一般在压片最后结束前会预留一部分物料报废掉,因在整个压片生产过程中压片机一直在震动,因此最终剩的部分物料的处方成分已发生改变。国内许多企业为了节省成本,一般将物料压至没有甚至压到压片机自动停止,这都是不合理的做法。
导轨不合适:小编初次压片时,即使将填充深度调至最大也无法获得目标片重,后来发现是忽视了导轨的问题。导轨是保证冲杆作曲线轨迹运动的重要部件,一般导轨槽的深度决定着最大填充深度,所以当需要较大或较小填充时,应考虑目前的导轨是否合适。这一点也是很容易被忽视。
另外,模具磨损导致物料填充不一从而影响片重。写到这里,小编已发现模具磨损能引生出很多风险。在压片前定要自己看看模具是否已磨损。
出现松片,小编首先想到的是增加压力。压力过小使颗粒间内聚力不强,可适当增加压力;压片速度过快也能引起松片,可适当降低转台转速。
从物料上说,物料过于干燥或含水量低,会导颗粒的弹性增强而塑性减弱,可重新摸索最佳物料水分值;处方中整体粘性较弱,导致物料间的粘性较弱,可适当增加粘合剂用量或改用粘性更强的粘合剂;润滑剂过量或混合时间过长会减弱颗粒间的内聚力。
物料流动性差而引起中模中的填充不够,这一点很容易被忽略掉,小编曾经遇到过,压出来的片子成型了却一碰就碎了,最后才发现是料斗里的物料没有留下来,导致中模中的填充量不够。
压力过大,是在压片工序中引起片剂崩解时限超限的主要原因之一,一般可在此工序考察一定范围内压力大小对崩解时限和溶出的影响,如测得RLD的硬度~8kg,那么可考察低硬度(~6kg)、目标硬度(~8kg)、高硬度(~10kg)下压出来的片剂对崩解时限差异和溶出的影响。
处方因素:物料颗粒硬度较大,可能是粘合剂加入量过多或粘性较强,可减少粘合剂用量或改用粘性弱的粘合剂;也可能是崩解剂性能不佳或量不够,可增加崩解剂用量或改用超级崩解剂。同时粘合剂内加、外加、或者对半加也能影响崩解时限,具体怎么影响需根据项目而定,可做一个考察。润滑剂如Mg-st用量偏多,阻止水分渗入片剂内部,可减少润滑剂用量,或改用亲水性润滑剂,如硬脂富马酸钠。
转速:压片中可能会发生这种情况,片子的硬度在低速下调整好了之后,增加转台转速后硬度变低了。转速若过快,物料受到的压力时间变短,颗粒瞬间反弹而使硬度变小,因此可以适当降低转台速度,或者通过增加预压力改善。
润滑剂:润滑剂用量偏多或者混合时间偏长,会减弱颗粒间的内聚力,从而降低片子硬度。
颗粒粒径:颗粒粒径整体偏小,比表面积太大,硬度大。可在造粒阶段尝试造粗颗粒。
含量均匀度不合格常发生于微丸压片和小剂量片剂(主药<25mg/tablet或比例<25%)中:微丸压片中,由于物料中粗细颗粒大小相差太大,即使物料已完全被混匀,在压片过程中也会因压片机的震动而分层,此时最好的办法是降低压片速度(该办法影响生产效率,但小编不知是否还有更好的办法);对于小剂量片剂,由于处方中各成分相差较大,一步混难以混匀,可用等量的增法、溶剂分散法(如主药加入浆液中制粒)等,同时延长混合时间(须兼顾疏水性辅料的影响)。
可溶性成分迁移:在涉及干燥步骤如造粒完成后的干燥或者包衣过程的干燥中,因水分蒸发过程中带动部分可溶性成分在颗粒间的移位,最终导致均匀度不合格,可使用与可溶性成分具有亲合力大的辅料,或采用微波干燥方式(传统干燥方法为外部加热干燥,微波干燥是一种内部加热的方法)。可溶性成分迁移可联想包衣过程中部分包衣液迁移后导致包衣着色不均匀。
本着以分享的态度,难免不全或有误,小编真诚期待各位同行朋友的指点。
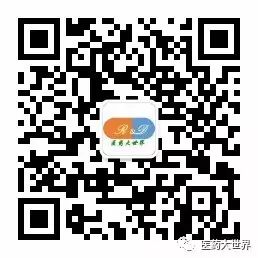