
过去的20年,中国作为世界新兴制造业大国,让人品到了成就与辉煌,也读到了不安与焦虑。工业革命的滚滚车轮和时代的快速变迁,深刻地冲击着传统的生产方式,“世界工厂”不再只是光环加身。
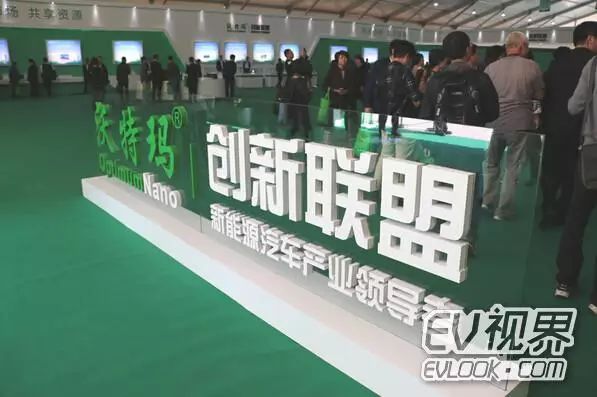
12月18日,在中国沃特玛新能源汽车产业创新联盟第三届年会上,创新联盟发起单位——深圳市沃特玛电池有限公司向参会嘉宾和媒体们展示了已经投入生产的动力电池全自动生产线,这是目前在国内处于领先地位的智能化生产车间,也是国内圆柱形动力电池实现智能化生产的首条产线。
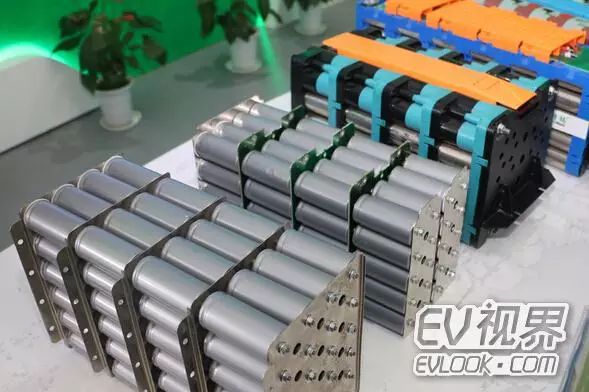
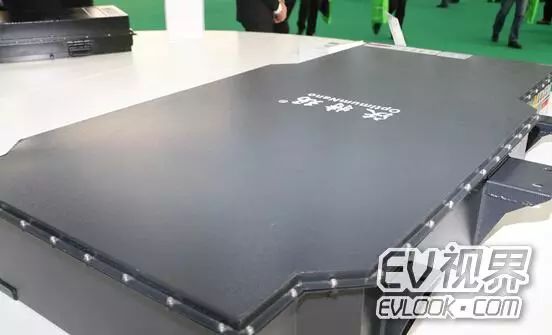
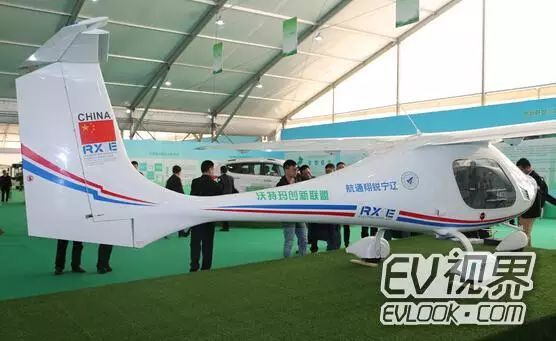
大制造、大数据与大智能的沃特玛智慧车间
走进这间车间,没有看到昔日拥挤的工人在车间穿梭繁忙的场景,反而显得有点“冷冷清清”。生产设备在高速运转,工人们却显得有些稀疏,为数不多的二十多个工人,看起来更像是技术人员。据陪同的工作人员介绍,这个车间已经实现了全自动化生产,不再需要工人上手作业。
这是沃特玛新打造的全新动力电池自动化pack车间,也称为沃特玛智慧工厂,集自动化、信息化、智能化于一体,通过云数据处理实现以机带人的自动化作业,形成集数据、信息、服务为一体的综合体系,11月中旬正式投产。
沃特玛智慧工厂采用新型的生产模式,通过云数据库管理和人机信息对接,仅需10人即可完成全部生产过程。目前,沃特玛pack生产线的所有工序:配档、电焊、包膜、锁模、组装和测试,已经全部由人工转为了自动,可以说,工人的双手已经走下了产线。
除了自动化设备,记者还在现场看到了机器人的身影。在测试区,一台机器人正在勤勤恳恳地给所有已经完成组装的电池箱进行充电测试前的接插线工作,然后将它们送上自动驶来的AGV小车进行充放电测试。尽管从速度上看机器人的动作并不比手工更快,但其背后所带来的规范化、标准化和全自动化,则是未来车间作业的方向。“从我们统计的数据来看,这条产线下来的成品,合格率高达99%。”现场工作人员介绍到。
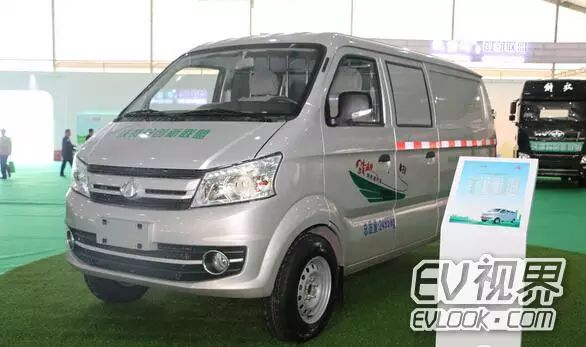
据介绍,沃特玛智慧化生产车间可实现信息数据化、过程可视化和决策智能化,从智慧车间出去的所有电池,都会纳入到沃特玛自主打造的沃联网大数据监控平台,实现数据共享;整个生产过程可视化,实现有效监管;此外,智慧车间可做到一键完成工艺流程设计,所有设备能够进行智能检测,对有效数据实行监控和实时记录,异常情况及时报警。
沃特玛“三步走”智能制造“扬帆计划”
动力电池是新能源汽车的核心,随着新能源汽车产业的高速发展,国家对电池生产企业在研发、质保、生产一致性等方面要求更加严格。在今年国家工信部发布的《汽车动力电池行业规范条件(2017年)》(征求意见稿)中,又再次强调了确保生产过程中一致性问题。然而传统的电池生产过程复杂繁琐,生产过程多以手工作业为主,劳动需求较高,且一致性较低,严重影响动力电池的整体性能。
今年9月20日,沃特玛集团总裁李金林在陕西沃特玛新能源汽车有限公司的投产仪式上表示,沃特玛已经正式启动“扬帆计划”,力争在5年内打造先进的智能制造标杆企业。
“沃特玛集团将抓住"中国制造2025"总体规划实施的大好机遇,紧密结合产业和企业实际,运用新一代信息技术和智能制造等融合发展,提升产品品质和市场竞争力,为行业实现新增长培育新动能。这是一个系统性的计划,我们有一个很平实形象的名字,叫扬帆计划。”
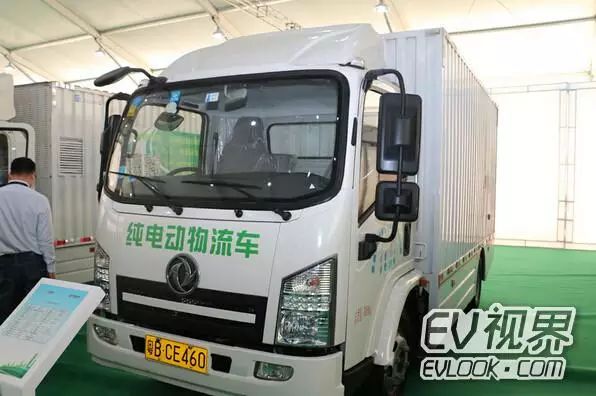
智能制造是产业发展的必争高地,作为国内排名领先的动力电池企业,沃特玛提早部署了系统化的智能制造计划,即到2014年半自动与人工加工结合,制程保证方案解决;2016年打造自动化,联合自动化设备厂商取消手工作业;到2017年提升智慧制造,基于示范点成功经验,打造沃特玛智慧工厂,形成行业标杆。
目前,沃特玛智能制造已经快速起航,智慧工厂在沃特玛的总部深圳和分部渭南先后成功落地,形成示范效应,明年又将在临汾、呼和浩特、十堰等基地进行复制,打造出国内一个又一个领先的高端动力锂电生产基地,推动产业升级。
“智能背后的价值是数据化运营和服务模式创新,要覆盖到应用推广和运营环节。”李金林指出。由沃特玛发起成立的沃特玛创新联盟,通过协作创新增强了智能制造后劲,并通过技术创新、产品创新、服务创新、模式创新和管理创新,推出了公交电动化、物流电动化和充电服务体系于一体的创新模式,目前纯电动公交运营落地17省26市,纯电动物流扎根5大省区,充电网络“两横一纵”规划建设……扬帆起航的不只是智能制造,或许还有未来的产业格局。
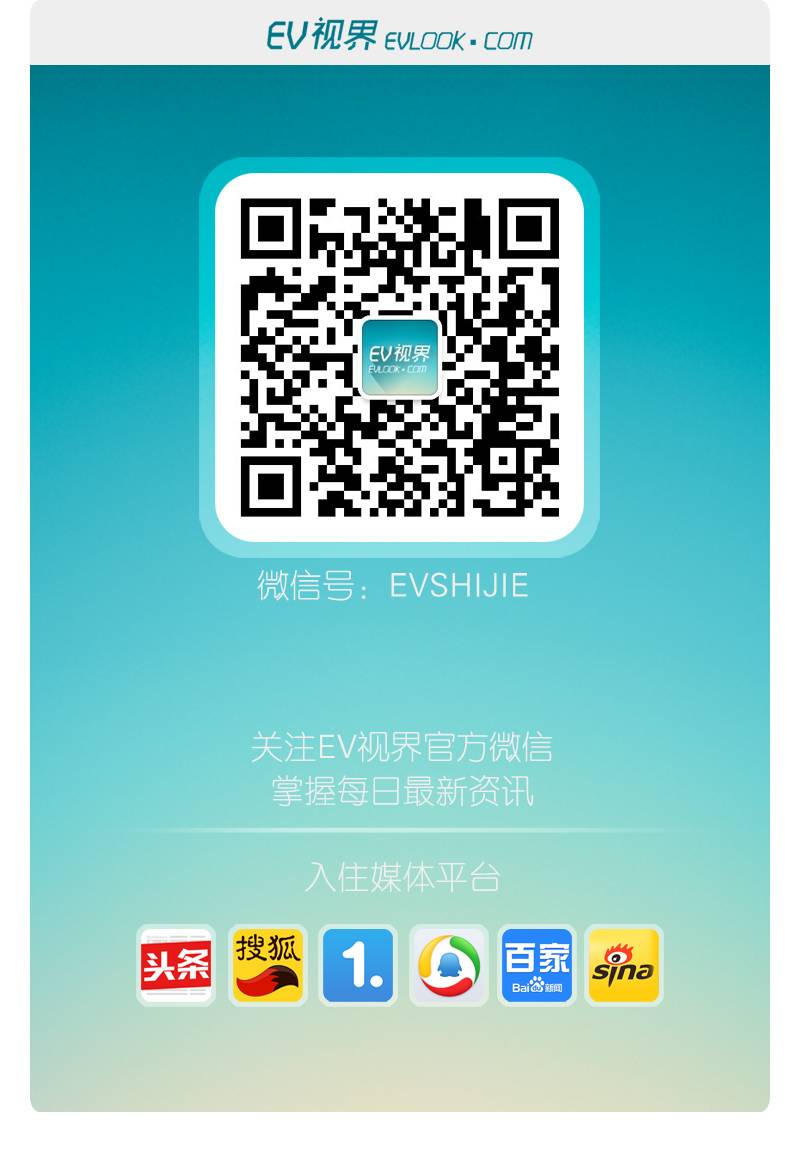
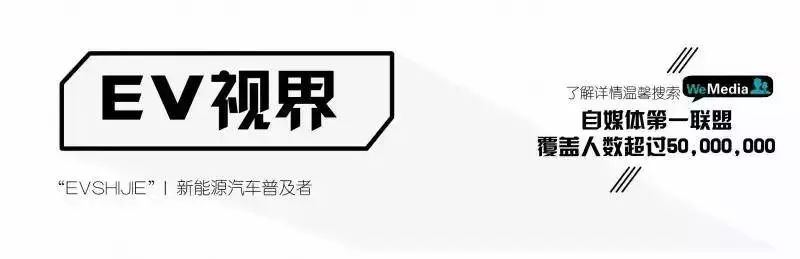
文章转自:中国电池网