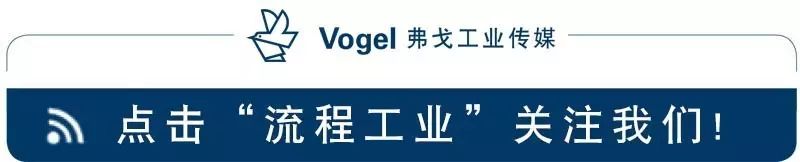
据某咨询机构测算,煤化工投资中设备占55%,安装工程大约占20%,建筑工程大约占8%,其余为设计、建设期利息费用等。显然,设备的成本对煤化工项目投资额有着决定性的影响。
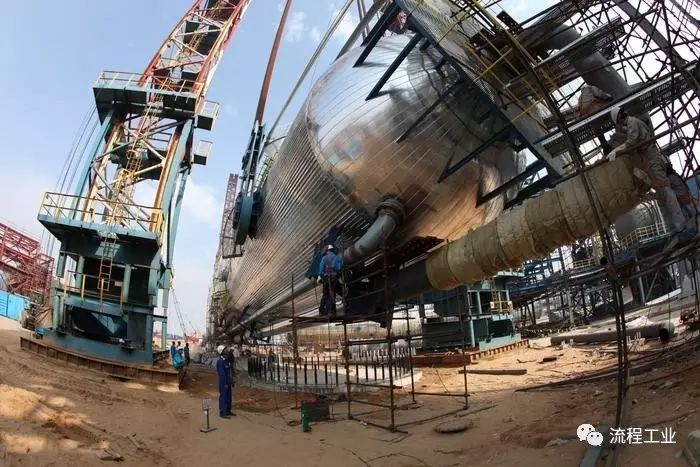
文︱张颖华,《中国煤化工》
有统计数据显示,于2011年投入商业运行的神华鄂尔多斯煤制油公司百万吨级煤直接液化示范项目共有重要设备2860台,其中引进的设备占设备总量的26%。为了引进重大关键设备,项目总投资从原计划的79亿元增加到130亿元。而在2016年12月打通全流程的神华宁煤集团400万吨/年煤炭间接液化项目中,国产化率达98.5%。原计划投资550亿元,实际投资500亿元左右,减降成本10%。显然,从增加投资到减降成本的变化,得益于“中国制造”。
气化炉是煤化工项目中首当其冲的核心设备。气化炉投资额往往占到煤化工装置总投资的四分之一到三分之一。曾经,我国是国外煤气化技术角逐的试验场。现在,国产气化炉早已成为主流炉型,并开始进军海外市场。
煤气化炉从物料接触方式分为固定床(移动床)、流化床(沸腾床)、气流床三大类。
一开始,神华宁煤集团400万吨/年煤炭间接液化项目想引进西门子公司的气化炉,但需要做些修改。然而,西门子公司仅针对气化炉的修改方案就开出了2亿元人民币的费用。后经过努力,2014年11月,由神华宁煤集团自主研发的神宁炉诞生。它解决了西门子气化技术只吃精煤的缺陷,能够通吃各种煤。2016年,美国买了两台宁煤炉。至此,神华集团煤化工项目的气化炉完成了进口——自主研发——出口的逆袭。
两次获得国家科技进步二等奖的多喷嘴对置式水煤浆气化技术已在国内外47家企业用户推广,在建和运行气化炉130台,市场占有率国内第一、国际第三。目前,国内单炉日处理2000吨以上的气化炉全部采用此技术,已成为气化炉大型化的代表炉型。
由航天长征化学工程股份有限公司研发的航天炉,其关键设备气化炉、烧嘴、破渣机、热风炉、安全阀、特种阀(氧阀、煤粉阀、锁渣阀、煤粉调节阀、换向阀、黑水调节阀)、高压耐磨泵、高速泵,均实现国产化。
由清华大学山西清洁能源研究院、山西阳煤丰喜和山西阳煤化工机械(集团)有限公司联合研发的第三代晋华炉于2016年4月1日在阳煤丰喜临猗分公司成功投产,截至2017年6月已经累计为公司节约运行成本3700多万元。目前,晋华炉正在研发第四代“晋华炉”,即在回收气化炉高温合成气辐射式蒸汽发生器的下游增加对流式蒸汽发生器,进一步回收高温合成气的热量,同时生产高温高压蒸汽。
国产气化炉的成功不胜枚举。目前,气化炉90%的部件能实现国产化,但一些核心部件仍然依靠进口,特别是单炉投煤量3500吨/天的大型先进气化技术及设备还有待技术突破和示范验证。“煤气化炉设备未来的创新点仍在于提高国产化水平、降低投资、提高煤气化压力、开发大型煤气化设备,提高节能降耗水平、节水水平、环保水平。”石油和化学工业规划院能源化工处副处长韩红梅说。
大型成套空气分离设备被称为“国之大器”。从2002年起,国内空分设备制造行业用不到15年的时间跨越了3万立方米/小时、4万立方米/小时、5万立方米/小时、6万立方米/小时和10万立方米/小时等大型空分设备的门槛。
2013年4月26日,在神华宁煤集团400万吨/年煤炭间接液化项目12套10万立方米/小时空分设备国际公开招标中,杭州杭氧股份有限公司与德国林德公司在众多竞争者中脱颖而出,各中标6套10万等级空分装置的成套设计、供货及相关服务合同,金额约17亿元人民币。同时,为该项目配套的12套压缩机组中,11套都是由德国曼透平承制,还有一套由沈鼓集团中标。
10万等级空分装置是全球最大的单机容量制氧设备。该设备可以在1小时内生产出可充满14个北京“水立方”的氧气。此份订单无论在合同金额、空分等级、还是在制氧总容量均居国内空分行业第一、世界前列。而在这之前,我国10万等级空分装置还是一片空白。而10万等级空分装置的心脏空压机组,全世界只有两家企业可以生产制造,绝对垄断。
4年之后的2017年3月15日下午2时58分,神华宁煤400万吨/年煤炭间接液化示范项目杭氧系列首套国产10万等级特大型空分装置一次开车成功,成功产出合格氧氮产品。实时数据显示,氧纯度达到99.6%,氮纯度达到99.999%,系统运行稳定,各项指标达到设计要求。
2017年5月15日,由沈鼓集团自主研发的我国首套国产10万空分装置压缩机组在神华宁煤400万吨/年煤炭间接液化示范项目现场一次开车成功。运行数据表明,机组的各项机械性能及气动性能指标均达到国际先进水平。10万空分机组全负荷试车成功向世人宣布,10万空分装置第一次用上了“中国心”。
据了解,沈鼓集团10万空分用压缩机组研制出炉后,西门子公司的同型号产品价格从每套1.7亿元下调到1.2亿元。而由杭州杭氧股份有限公司设计制造的12万立方米等级特大型空分设备,也将配套世界最大天然气制甲醇项目——伊朗波斯湾附近的210万吨/年甲醇项目。这意味着我国制造的特大型空分设备已然跨出国门,正式进军国际高端市场。
长期以来,国内甲醇大型化走的是过去合成氨的老路,即基本上成套引进天然气制甲醇装置,或者引进煤制甲醇中的合成回路。大型合成氨和甲醇生产技术装置迟迟实现不了国产化。在一些年产60万吨甚至百万吨级大甲醇项目中,国内的技术开发商即使有机会收到参与投标的邀请,也往往无缘最终投标,连参与竞争的机会都没有。造成这一局面的主要原因,就是自主技术缺乏工业应用案例,业主保险起见,都直接选择了进口的技术设备。
转机终于出现。2016年6月,采用杭州林达化工技术工程有限公司(简称林达公司)绕管式水冷反应器技术设计制造的DN3600甲醇合成塔在河南顺达化工30万吨/年甲醇项目投运成功。据杭州林达化工技术工程有限公司副总经理冯再南介绍,该项目的合成塔采用林达公司绕管式水冷反应器技术,投运后表现出催化剂床层温差小、循环比低等特点。
有了第一,就会有第二。据了解,林达公司已中标并签订新疆中衡甲醇国际招标项目合同并已完成年产80万吨/年工艺包设计。该项目4.2米直径合成塔日产甲醇2470吨,在110%负荷下年产甲醇95万吨,已达到DAVY大甲醇单台90万吨能力。2015年底,林达公司还与中石化宁波工程公司签订了合作开发年产180万吨大甲醇工艺包协议。
过去,业内人士常说,我国是阀门制造企业最多的国家,也是高端阀门进口最多的国家之一。也就是说,中国企业只能生产阀门中的低端货,高端阀门还得进口。煤化工领域尤其如此。
但是这几年有了变化。2009年8月云南天安化工公司开始在壳牌炉上试用上海开维喜集团股份有限公司生产的锁斗阀,投用后都未出现问题,开关动作灵活正常,从运行周期上来看还要比进口阀长,而价格是同类进口阀价格的三分之一多一点。目前,上海开维喜集团股份有限公司已经获得了壳牌的认证,成为其阀门供货商。
就这样,国产高端阀门挤出了一道门缝,而且门缝越挤越大。航天长征化学工程股份有限公司依托中国航天在运载火箭和液体火箭发动机中特种阀门在高温、低温、抗氧化性、耐磨等方面的技术积累,研制出适合于煤化工苛刻工况的特种阀门,打破了进口品牌在煤化工领域的垄断地位。2008年10月,200多台煤化工特种阀门成功配套于河南濮阳龙宇15万吨/年煤制甲醇项目和安徽晋煤中能20万吨/年煤制合成氨项目中。2011年9月,航天工程公司开发的高温硬密封氧气切断球阀经过中国石油化工联合会、氮肥协会、中国航天科技集团组织的专家鉴定。
2016年8月,苏州安特威阀门公司根据干煤粉装置特殊需求所研发出的全球第一台双盘阀,使用寿命达到了德国产品的2倍以上,综合性能已达到国际领先水平。此国货现已广泛应用于壳牌、西门子GSP等煤化工工艺系统中,其在磨损冲蚀性介质有卓越性能,且价格适中,供货周期短,售后好,性价比极高,因而成为进口阀门的替代产品。
除了阀门,一批国产材料也开始走向世界。
内蒙古北方重工公司制造的P91管线产品可完全替代进口,价格比进口的15万元/吨低70%,且供货周期由1年缩短至90天;江苏海鸥冷却塔公司研发的大型环保型冷却塔群,成功中标土耳其速马电厂项目,进入西门子公司全球采购系统;河钢集团舞阳钢铁公司的钢板已出口到中亚、中东地区。
据统计,神华宁煤煤制油项目中,用于37项国产化攻关的投入约57.6亿元人民币,而新增销售收入87.3亿元人民币。这份账单说明,“中国制造”是一个稳赚不赔的事业。