多少人以为只需要一个灯泡(或者LED),一个反光碗(甚至有人都不知道还有反光碗更不要提上面的光学面了),再加一个灯罩就完事了!
每一次被问工作时,答曰:汽车车灯设计。然后对方就一脸嫌弃:一个灯有什么好设计的…
前灯主要由面罩、饰框组、光源系统、底座组成。
面罩就是车灯最外面的那个透明罩子,看着就像个畸形的脸盆似的,并无什么特别的地方,然而并没有看着的那么简单。
面罩分为单色和双色面罩。


单色面罩较为简单,然而考虑到内滑块或者斜顶和近光灯对配光的严格要求,一般采用单色面罩的前灯Z向开口都比较大,外观可能就不是那么美观(如上两张图你会喜欢哪一款)。而且仔细看,在某些地方有一些细线——滑块线,当然为了减小滑块线对外观的影响,需要在内部做一些特征使滑块线显得不是那么明显。可不可以不用内滑块或者斜顶?好吧,如果造型不改的话那么灯具末端靠近翼子板的三角区域怎么出模?靠近引擎盖的地方的缩水如何避免?
双色面罩可以避免滑块线的外观问题,造型尽量美观一些。然而前灯面罩的双色模可不是那么容易做的,国内做的好的没有几家,因为模具大而且复杂、加工精度还高。
此外,面罩外部需要喷一层漆,即所谓的PC-coating,防止划伤。内侧根据客户要求是否喷防雾涂层。设计面罩的时候也需要考虑工艺,不好的设计会导致於漆,滑漆灯外观问题。此外还需要考虑模流,不好的设计会导致流痕,而流痕这种东西即使用moldflow分析也未必分析的出。
最后,last but not least,胶腿的设计也很重要。什么是胶腿,面罩和底座是通过胶粘在一起的,底座上为胶槽。下图中LENS即面罩,BASE即底座,也叫Housing。这里如果设计不合理,会导致气密问题,那么整个灯就废掉了。此外,选用的胶的种类也很重要。
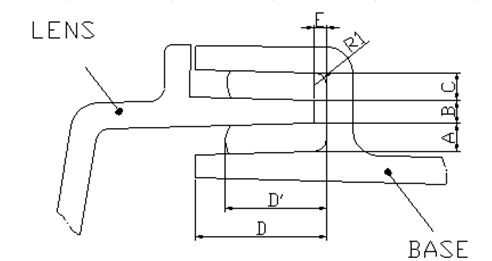
饰框和内套。饰框主要起装饰作用,将内部结构遮挡其他。
呃。。。看来大家都知道车灯不好搞,那就不用再掰扯了,下一个~
在很多时候刮水器都是个摆设零件,但是在整车中,这个小小的零件算的上是最难设计的零件之一。
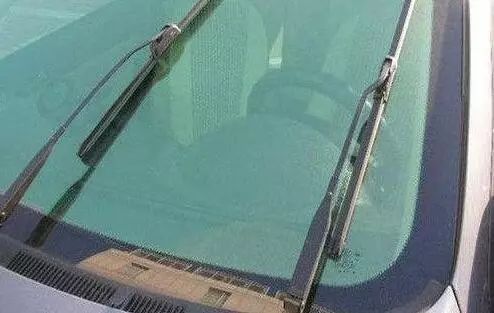
为什么这么说呢?首先雨刮器可以归类为车身零件中的A类零件。那么什么事A类零件?简单点说,就是车辆安全行驶的必要零部件,它的性能是必须符合国家强制法规要求来配备的。
举个例子,老的国家标准规定,雨刮器必须在120公里每小时的车速下稳定工作,眼下,这一标准提升到160公里每小时,在这一时速下要保证雨刮器能够紧密的贴合挡风玻璃,并且回水宽度满足法规要求,仅这一项实验要求的变化,就会使得整个雨刮器系统需要重新设计。
其次,雨刮器系统的相互制约参数最多。一般来说,至于刮水器性能的参数一般有三个:攻角、俯角以及刮臂压力,这三个参数相辅相成,改变其中的一个就会导致其他两个的变化,继而导致刮刷效果的恶化。
第三,雨刮器的安装位置位于车身硬点区域,这直接导致了安装空间和安装结构的不可变。一般来说,避震塔到前围档板之间的距离为整车硬点,这个距离决定的是整车的平台。所以,我们看到很多模块化的平台,其实这个位置都是固定的,比如说大众的MQB。
那么问题就来了,在这个不可变的区域内放置一套运动的四连杆机构,还要考虑到运动干涉、系统本身的性能、洗涤器喷水效果。难度可想而知。

挡风玻璃和侧窗玻璃同样也是被大家忽略关注的零件之一,大家对它的关注恐怕就是在贴膜的时候才能想到吧。不过,在整车的零部件里,挡风玻璃以及侧窗玻璃同样是关乎安全的A类零件。在设计过程中,侧窗玻璃是整个车门系统设计的基准,只有确定了侧窗玻璃的曲率以及面积,才可以由此向下设计玻璃导槽、举窗电机、车门门锁等等零件。
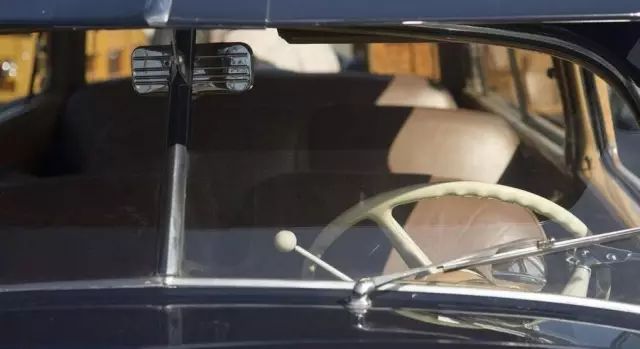
如果侧窗玻璃曲率以及面积在造型阶段没有第一时间确定的话,那么等待工程师的就是整个车门返工重来。挡风玻璃同样是前部的设计基准,其曲率决定了刮水器、A柱、流水槽的结构设计。
另外,挡风玻璃的曲率也会被制造工艺牢牢限制,同时,挡风玻璃还是造型面,这就使得挡风玻璃的设计一不小心就会夹在中间无法脱身。所以也大大提升了挡风玻璃的设计难度。

普通消费者对保险杠的认知,可能还停留在这就是一块塑料壳。对,我们就是这么任性,车上全是塑料壳。对于设计人员,一个前保险杠,可能是最复杂的外饰件之一了。首先是,周边环境复杂,对口件太多。引擎盖啊,挡泥板啊,轮胎包络啊,各种灯啊,水箱位置啊,防撞梁啊,脱钩啊,雷达啊,AEB啊等等。
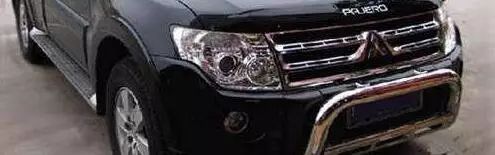
作为一个产品设计汪,你真在专心致志地做数据,开闭件工程师跑过来,你这里这里圆角倒得有问题,导致视觉间隙很大,得改一下。你一看这么大一个锅,也不敢独自背啊,卧槽,这圆角特么是A面上的圆角,我能改么,你找Style吧(造型设计师打了个喷嚏)。
开闭件工程师一看,吆喝,放大招啊,好啊,找造型去。这边刚走,轮胎工程师又来了,刚才把轮胎包络重新做了一下,变大一点,你这里这里的卡扣和紧固点距离包络的间隙不够安全值,都得改……你一听把刚和的水全吐轮胎工程师脸上了,大哥,不带这么玩的,你知道工作量有多大吗?轮胎工程师表示没办法,专家给的新算法,更精确。这个好像没法推了,怎么办,我水还没喝完呢。你把轮胎包络先发给我吧,我看看。已经发给你了,你查查邮箱,你滚!这边轮胎工程师刚走,冷却系统的工程师又来了,你预感到一层黑暗气息轮罩了你的办公桌三尺范围之内。忙哈,我刚才又算了一下进风面积,你这里这里做的结构把进风口挡住了,不利于水箱散热,格栅这里需要做一下调整……
此刻你脑子里只有调整调整两个字在循环,心里想着特么你两个字我B面结构就要重新做了。正在这时,电器工程师跑过来拍了一下你的肩膀,露出迷之微笑,上面决定了,高配车型要加装AEB系统,格栅这里这里结构需要更改,还有增加一个低配时装饰用的装饰盖。唉,你怎么打人啊,打人是不对,啊啊啊啊……大家都走了,你又开始一个人忙碌,把工程更改梳理梳理吧,一晃太阳西斜,快下班了,你的心情顿时明亮了起来。你站起来伸了伸腰,活动活动筋骨。这时,电脑右下角传来一声Outlook魔性的邮件提醒声,你大叫一声不好,然而为时已晚。来自造型设计师的邮件,就五个字:面用原来的。
你以为完了,可以神游天国了,怎么可能,CAE工程师救活了你。您还不能走啊,分析结果显示,你这里的结构太硬了,不利于行人保护;然后你这里的结构又太软了,不利于低速碰撞。你先把这两个问题解决了再走吧。你下班了,但是明天还得继续战斗。这就是一个保险杠产品工程师的日常。
保险杠从外观上看,没什么,确实是一个塑料壳子,但是其B面结构的设计非常复杂,各种对手件的集成设计,还有法规项的考量,卡扣形式的选择,都是需要慢慢去抠接口,做布置,挑战其他系统,也对其他系统做出各种妥协的结果。除了这些之外,考虑模具的影响,浇口的布置,各种接口的实现,又得对现有结构进行优化。考虑涂装的影响,又要根据工厂的涂装线规划,机器人的能力,对产品做出修改。装配线,运输悬链等等,都会对产品的设计产生影响,设计一点都不简单。

仪表板和保险杠一样,因为布置在其上的接口多,各种按键,仪表,电器件等等,接口设计极其复杂。为了追求良好的触摸质感,制造工艺复杂,搪塑啊,吸塑啊,发泡啊,都会给设计带来困难。
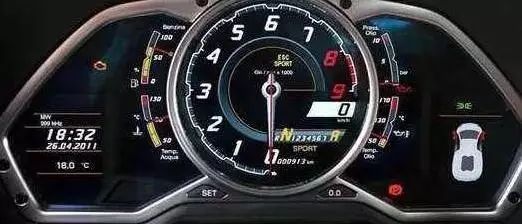
储物盒的布置,你得放的小各种东西吧,你还得考虑人机工程,大部分人能伸手够得着吧。仪表的事业不能遮挡,还得遮光放炫目,以免驾驶员看不清仪表上的指针数字。仪表板还不能太高吧,以免遮挡驾驶员的视野。和门护板,玻璃,中控的间隙你得控制吧,不然不美观。车内VOC得考虑吧,你看对门奔驰都因为这个被诟病,我们三线小自主,得学着点啊,材料不能乱用,选个味道好点的。
以仪表板副驾驶布置副驾驶气囊那个区域,算是仪表板上难设计的一个典型。大家都知道,气囊是布置在仪表板下面的,所以当遇到碰撞事故时,气囊在加速度的作用下经过传感器引爆,把这个区域的仪表板炸裂,然后气囊充气鼓起,对乘员形成保护。所以,这个区域的仪表板厚度需要精确控制,厚了不行,炸不开啊。所以这个区域一般会做弱化减薄处理,有些做到零点几毫米。但是做薄呢,又回带来外观问题。为什么呢,PP材料对厚度变化特别敏感,这个区域厚度的突变,往往会产生比较明显的缩影,而仪表板一般是要腐蚀皮纹的,皮纹对于缩影这种缺陷是起放大作用的,所以会非常明显。
还没完,产品出来了进行气囊爆破试验,炸裂的仪表板碎片,也要控制,不能太大,重量要控制,以免爆炸后飞出伤及乘员。如果不合格怎么办,回来改结构,再分析,再试验,到合格为止。

在汽车工程领域,只要是有三个零件结合的地方,都会被工程师们称之为死亡三角。
其中最典型的区域就是A柱和窗台线之间的三角区域。那么它为什么被公认难啃的设计之一呢?
要说明这个问题,我们首先要知道一个叫公差的东西,任何零件的制造和安装都存在着一个合理的公差范围,对于单一零件而言,零点几毫米的公差波动是认为合理的。不过,当几个零件同时在一个狭小的区域实现匹配的时候,公差波动就会在这个区域出现公差累积的情况。
也就是说,这个零件尺寸在正常范围内跑偏了零点几毫米,另外一个零件也在正常范围内跑偏了零点几毫米,但是当它们匹配在一起的时候,这些正常的公差值就会体现为一个误差值,继而造成外观质量甚至是性能方面的缺陷。
以车门三角区为例,在这个区域内的零件包括外后视镜盖板、车门密封条、窗框、玻璃导槽、窗框加强板、窗框亮条等几个零件。这几乎是整辆汽车上零部件搭接最密集的地方,所以也是最容易出现公差累积的位置。所以,在设计终了之后,这个位置还需要进行数论的间隙段差匹配,同样,也是触一发而动全身的设计从而大大提升了难度。

然而看着也就是几片圆环,却占据了整机35%的摩擦功,50%左右的机油耗问题与之相关,直接接触上千度的燃烧火焰,承担了25%-40%的的活塞散热通道,密封了峰值爆发压力达到100个大气压的燃烧室,而你只需要支付几听可乐的钱就可以拥有一缸副,但是如果它失效了,客户需要支付1万-2万人民币以上进行大修或者3万-6万人民币进行动力总成更换。
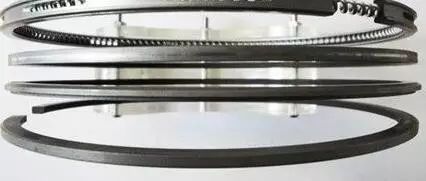
全球入流的汽车企业的钢制活塞环的材料99%由日本钢材线材供应商提供。全球4-5家供应商基本占据了全球的主要活塞环的生产。在这个宽度只有1-2mm的钢带上,我们实现了各类加工形貌造型,20多种金属/非金属涂层,使用了热处理、电镀、PVD/PCVD、等离子金属喷涂等一系列的技术,目前最先进的涂层历经24万公里和缸体的磨损,平均磨损量仅有0.0008-0.001mm,而且能够以每年数千万片的规模保证质量稳定一致,平均PPM低于10。
基于三维的模拟软件可以分析在各个发动机工况下,活塞环体在360度的变形和动态扭转形貌,从而计算出摩擦功/机油耗/漏气量等一系列的数据。在微观尺度下计算u级的外周形貌变化对于油膜形态以及摩擦区域的差异和影响,同时还有透明缸套试验+荧光高速摄影和浮动缸套试验进行验证,复杂的工序也体现出了它设计的难度系数。
活塞环有气环和油环之分,气环位于活塞的第一环和第二环,某些重型柴油机由于其工作载荷较大,为了能更好的对高温气体起到密封的作用,有时还具备第三道气环。但对于汽油机和小型柴油机来说,两道气环的设计已经满足密封的要求,故不需要第三道气环。最下面的一道活塞环是油环,其作用是对气缸壁润滑和阻止机油进入燃烧室。
它的磨损或损坏会导致发动机工作不正常,特别是窜机油的概率增大。如果一台使用时间很长的汽车,在机油加注正常的情况下尾气冒蓝烟,很有肯能就是活塞环出现了问题。此时如果排查其他部件没有问题仍然烧机油的话,就得将缸盖打开更换新的活塞环了。

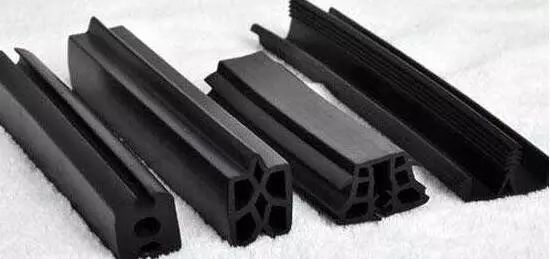
哪天你发现怎么我的车怎么不使劲摔关不上门,怎么开门声音是啪的一声,而不是彭的一声?
哪天你发现你的车怎么开始漏水了,后备箱一打开里面可以养鱼了……
哪天你发现玻璃怎么升降过程这么慢,还有点乱七八糟的响声,甚至卡住……
哪天你发现开车呼呼的风噪大到你没法听音乐……
哪天你发现你的车窗上被塞满了小卡片,而旁边的豪华车却是夹在风挡玻璃上……
这一切,密封条都逃脱不了干系!
内行人看车先看车门,而看车门重点还在密封条上。可惜的是,国内这方面设计能力太欠缺,明明很重要的一个零部件,可从上到下都不重视,各种压缩成本……
国内也欠缺这方面的人才,缺到什么地步呢?网上某人说,一个三流主机厂的半吊子密封条产品工程师都被猎头推荐到上海一家一流外企设计公司去了,外企HR说他英语不过关,人家说:没关系,我们可以放宽要求……不要求你英语……

翼子板才是最可怕的零件,大学的时候有门课叫做《互换性与几何测量技术》,里面讲的最多的就是公差与配合,最难的也就两个零件轴和孔的配合。
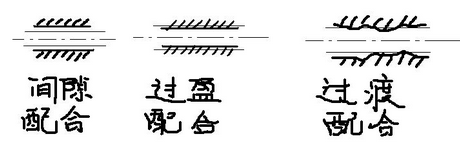
直到TM出现翼子板,才知道原来一个零件可以和这摩多零件配合,发动机舱盖、车大灯总成、前保险杠、车轮和车门,一不小心就从公差变成误差了(手动流泪);我终于知道为啥有些人买车的时候先买好皮尺去4S店测量翼子板各个位置的间隙去看厂家的做工怎么样。
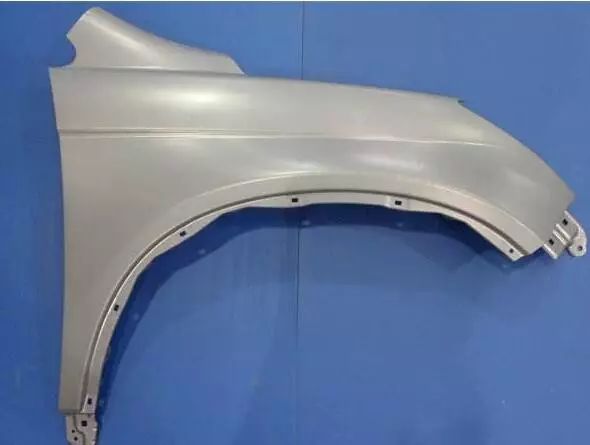
计算公差就算了,翼子板上还有各种造型要求的线条;橙色箭头与车 侧窗玻璃形成的belt line;红色箭头与OTR外板 形成的shoulder line;还有车前黄色箭头标示的车头feature line…每次模型固定前,设计师、工程师和生产技术人员都会围绕翼子板有一场口水战。

车载的电控单元是看不见摸不着的一段3MB大小的代码。车载控制器和发动机配套的就是发动机控制器(ECU);和变速箱配套的就是变速箱控制器(TCU);和混动配套的有混动中央控制器(HCU),电机控制器(MCU),电池控制器(BMS);还有车身控制器(VCU),ESP……
在车辆全面电控化的今天,控制器就是各类子系统的大脑,连悬架可能都有独立的控制器。而缺少某个关键控制器,你的车也就和刷ROM挂掉的手机一样,板砖一个……
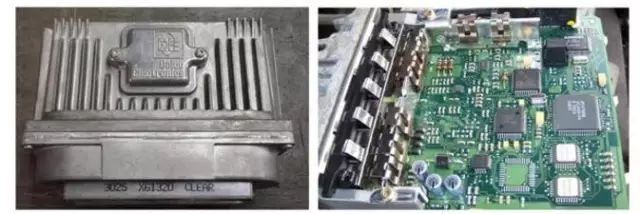
然而大多控制器都很小巧,且藏在发动机舱,后备箱或者其他内饰板下面,故障率极低,所以一般用户可能永远都不会接触到,甚至不会意识到他们的存在。可以看到的也只不过是一个金属外壳,不知道里面有什么,知道的人大多以为这只不过是块电路板,也不知道这个可能是整车设计最难和最贵的部分。
成本最高和设计最复杂的,还不是车载控制器硬件本身,而是你根本看不到的刷写在ROM里的控制软件代码。一个控制器的电路硬件成本可能只有上百美刀。一个复杂控制器装载的软件,比如发动机和变速箱控制器的软件,5兆字节不到,但是从头开发的话需要:①在国外成熟的技术条件下,一个数十人的有相关丰富经验的技术团队。② 三至五年或者更久的时间产出第一版量产软件,然后再用一个更久的周期使软件成熟。③ 轻松上亿人民币的研发费用,而要一个软件真正成熟,经过多年的版本更迭研发费用轻松达到十亿级别。
这一切只为产出大概 3MB 的代码。
所以,很多车载系统的自动化都伴随着极为昂贵和复杂的控制系统设计,比如从手动变速箱到自动变速箱,又比如自动驾驶。其中成本的增加绝对不只是一个几千上万块的箱子或者几个摄像头雷达而已,只不过一般消费者看不到罢了。

设计起来复杂的零件绝不会看起来简单。设计起来复杂无非以下几点:1,机构复杂;2,公差、互换性等要求高;3,零件结构受限且工作条件恶劣;4,需要妥协的零件、即在设计上要考虑众多因素,需要寻找一个最佳平衡点。
例如:活塞环,活塞环又包括油环和气环,活塞环不能太紧、否则将增大摩擦、造成过多的发动机功率浪费、太松也不行、起不到密封作用。油环还同时起到辅助润滑作用、润滑油当然也有一定的冷却作用。通常活塞环都会设计切口、切口要错开布置、防止串气或造成烧机油,活塞环切口设计很关键、有效避免泵油是防止烧机油的关键。
例如:燃烧室。燃烧室看起来很简单、实际上很讲究。设计巧妙的燃烧室能够使混合气混合更加充分,能产生涡流或滚流来帮助快速混合。根据公式可知,燃烧室容积大小还涉及到压缩比,随着科技发展,现如今的压缩比可以做到越来越大,但是过大的压缩比是很危险的,一旦压缩比过大、容易造成爆燃、对发动机造成伤害。
还有很多很多类似的零件:例如同步环、同步环是换挡的关键零件、虽然只是看似简单的一个带齿的圆环而已。再例如涡轮增压技术的关键零件:涡轮里面所使用的轴承,涡轮工作时转速高达十几二十万转,如此高的转速是需要一个多么精密的轴承、且润滑要做得多好、这是一项很神奇有趣的技术。
汽车上有成千上万个零件、若是一个汽车迷或者机械迷、就会发现每一个零件都有自己精彩的故事。

这还真是个不错的问题。然而以我简陋的知识储备,回答起来可能不怎么到点子上。
个人认为有三方面需要说明一下:
首先,汽车零部件的设计开发流程决定了其合作性的开发模式。越大的零部件,越是会与其他零部件发生干涉、配合、共同工作的零部件,其开发流程需要考虑的内容越多,当然也就越复杂(比如翼子板、气囊)。而完全独立的开发,也是在给出边界条件的基础上自行负责内部结构等,最后实现功能性能,最简单的可能就是一个尺寸要求而已(比如变速箱内的油毡),这种相对还是简单一些。
与安全相关的零部件、强制性认证检查零部件(这两个概念有一些区别,请注意),如无特别,多数都会有相关的法规要求,且要涉及到可靠性验证。从设计和验证上,多数需要涉及CAE、疲劳试验等,复杂程度有所提升。
个人感觉,一般零部件的设计难度:传动/制动/转向系>车身≥电控系统>附件。这个判断做不得准,只是皮毛感觉而已。
以上仅讨论设计难度(有无参照、有无限制),但不讨论实现难度(生产流程)。
综合我个人的了解,认为气囊系统(Airbag System)是比较复杂的一个产品。以驾驶位气囊系统(DAB)举例:
涉及到的主要物料包括塑料件(罩盖)、织物(气囊)、化学品(炸药)、金属(壳体)等;
需涉及物理加工(注塑、涂装、裁切缝合、组装;冲压、焊接)、化学(炸药配比)、电学(响应曲线)等;
安全件,且有A面,还需结构设计、仿真、实车碰撞实测等多项内容;
如果形成方向盘总装件,则还包括金属骨架、发泡框体、皮革包覆、缝合等多种加工方式。
以上的环节,从设计开发到生产流程,包含多个领域,整体来讲绝不简单,细节就不多说了。
看到这,发现各个零部件的设计都不容易。以上内容整理自知乎,感谢知乎的大神们。

▼ 点这儿,来看看盖世更多精彩文章