说明:国内主营的炼油企业均已实现了炼油装置的规模化、大型化和一体化。目前国内的单套常减压装置的设计规模基本是1000万吨/年,本节仅以国内某1000万吨/年的常减压装置的设计为例对常减压工艺、设备、能耗、HSE和投资等方面进行阐述。文中如有错误欢迎您批评指正。
1.1 工艺概述
根据加工原油的性质不同,常减压装置的工艺配置会有所不同,但该装置一般由原油换热、电脱盐、初馏、常压蒸馏、减压蒸馏、气体脱硫、一脱三注等部分组成。主要目的是将原油中不同沸点的烃类物质经过蒸馏提取出不同馏程范围的组分,用于下游工艺进一步加工生产精制产品。
1.1.1 脱盐
原油通常含有水,无机盐,悬浮物和少量水溶性金属物。炼油加工的第一步是这些杂质必须通过脱盐工艺去除,来减少设备的腐蚀,堵塞和结垢,阻止其对后序工艺催化剂的毒害。
原油脱盐有两种典型的方法,化学脱盐和电脱盐,但电脱盐目前在炼厂中较为常用。它利用高压电场使微小的水滴聚集成较大的水滴,靠重力从油中沉降到罐底得以分离。原油中如含有大量的悬浊物时可以加入破乳剂。
进入电脱盐罐前,原油中一般要注水和破乳剂,其用量为分别原油量的4~6%和1~3%。经过混合阀和静态混合器充分混合。电脱盐罐其中充满液体,利用电场来分离原油中的水份。最佳操作温度为120 - 150°C。原油中含有的部分盐类,尤其是镁,氯,在120°C以上可以水解。通常电脱盐罐由多级组成,可以脱除原油中90%的盐分,有效的阻止设备的腐蚀和下游催化剂的失活。
图1.1-1电脱盐的典型工艺流程
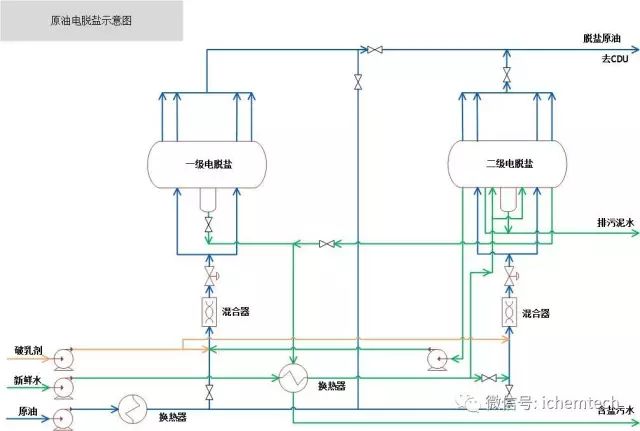
1.1.2 常压蒸馏
炼油工艺的第一步工序就是利用常压塔和减压塔将原油分馏成不同的组分或直馏馏份。这些馏份有特定的沸点范围,可以按照其挥发性的大小分为气体组分,轻馏分油,中馏分油,柴油馏分和渣油馏分。
脱盐原油经过换热器进一步加热至气化,系统压降也随之增大。温度在170 -200 °C左右时,进入初馏塔,操作压力为2~5Barg,进行气液分离,气体直接送至气体处理单元(GPU)。
原油在进入常压蒸馏塔前需要经过一系列换热器与需要冷却的工艺物流进行换热,一般原油经过换热后温度达到200~280°C,然后再送至常压加热炉。加热到200~280°C的原油进入常压加热炉进一步加热到330 -370 °C后直接进入常压蒸馏塔,在常压塔中按照不同的沸点馏程分离出不同的馏分。
在350 °C,约1barg的工艺条件下, 大部分的原油被气化,并通过每层塔盘的阀孔向上流动, 在上升的过程中冷却。 当气体到达某层塔盘时的温度刚好低于其沸点,气相转变为液相,连续的液相物流依靠重力沿降液管逐层向下流动。同理,不同馏程的馏分在常压塔的塔盘上逐级的分离出来。最重的馏分在最底的塔盘,轻馏分则在塔的上层塔盘。在常压塔的不同高度设有抽出盘,该馏分从抽出盘出依靠重力抽出,作为下游原料进一步处理。
塔顶气相物流通过管道送至塔顶冷凝器,通常是空冷器,在塔顶冷凝器中冷却至40 °C后不凝气和液相石脑油混合流进塔顶回流罐,在回流罐中气液分离,气相送至气体精制装置回收LPG(C3/C4), 液相(石脑油,馏程60-200°C)送至加氢装置脱硫处理,作为汽油。
常压塔第一个轻组分抽出物流(常一线)是煤油,馏程为160 - 280 °C,通过管道进入侧线汽提塔。侧线汽提塔的作用是用注入蒸汽或外部再沸器加热来去除轻组分。控制汽提蒸汽流量或再沸器负荷来达到产品闪点的指标。和常压蒸馏塔一样,侧线汽提塔也是通过塔盘进行气液接触,塔顶气相返回常压蒸馏塔。
常压塔第二或第三抽出物流(常二线,常三线)是柴油馏分,馏程范围为200 - 400 °C,其最终用于调和柴油成品。和煤油馏分一样,柴油馏分(轻、重馏分油)也要经过侧线汽提塔后再送至下游装置。
常压蒸馏塔底部抽出的较重的,黑色的渣油馏分。 在常压塔底部专门设置有几层汽提塔盘,采用汽提蒸汽脱出渣油中的轻组分,蒸汽量为塔底物料的1~3%。为了减少设备的露点腐蚀,在初馏塔和常压塔顶部注入缓蚀剂。
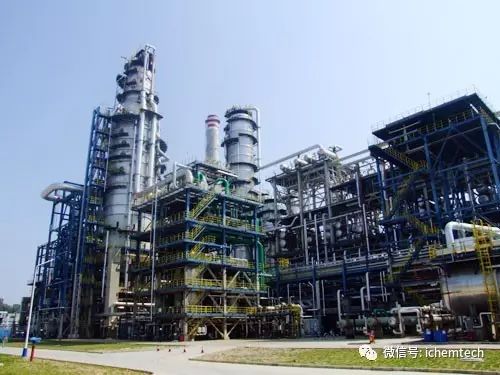
1.1.3 减压蒸馏
减压蒸馏是为了防止来自常压塔的渣油在较高的温度蒸馏时发生热裂解。常压塔底重油用泵送入减压加热炉,加热到390-400℃进入减压蒸馏塔。塔顶不出产品,分出的不凝气经冷凝冷却后,通常用二级蒸汽喷射器抽出不凝气,以利于在高温减压下使油品充分蒸出。塔侧从一二侧线抽出轻重不同的减压蜡油馏分,可以作为润滑油馏分或裂化原料油,它们分别经气提,换热冷却后,一部分可以返回塔作循环回流,一部分送出装置。塔底减压渣油也吹入过热蒸汽气提出轻组分,提高拔出率后,用泵抽出,经换热,冷却后出装置,可以作为自用燃料或商品燃料油,也可以作为焦化原料、丙烷脱沥青或润滑油装置的原料,进一步生产石油焦,沥青和重质润滑油。
为了降低能耗,循环回流和侧线物流的热量可以作为渣油原料的热源,过剩的热量可以用来产生中压或低压蒸汽或通过热集成用作其他装置的热源。
1.1.4 主要工艺参数
表1.1-1 国内某项目常减压装置操作条件
常减压装置主要操作条件(示例) |
序号 | 项目 | 设计参数 |
1 | 设计规模 | 1000 *104t/a |
2 | 年操作时间 | 8400h |
3 | 操作弹性
| 60~110% |
|
|
|
1 | 原油进装置温度 | 45℃ |
2 | 电脱盐温度 | 120℃ |
3 | 初馏塔顶压力 | 0.4MPa(g) |
4 | 初馏塔进料温度 | 220℃ |
5 | 常压炉入口温度(换热终温) | 300℃ |
6 | 常压炉出口温度 | 365℃ |
7 | 常压塔顶压力 | 0.16MPa(a) |
8 | 常压塔底温度 | 356℃ |
9
| 减压炉出口温度 | 390℃ |
10 | 减压塔顶压力 | 15mmHg(a) |
11 | 减压塔顶温度 | 70℃ |
12 | 减压塔底温度 | 365℃ |
13 | 稳定塔顶温度 | 50℃ |
14 | 稳定塔顶压力 | 1.0MPa(g) |
图1.1-2 典型的原油蒸馏装置流程图
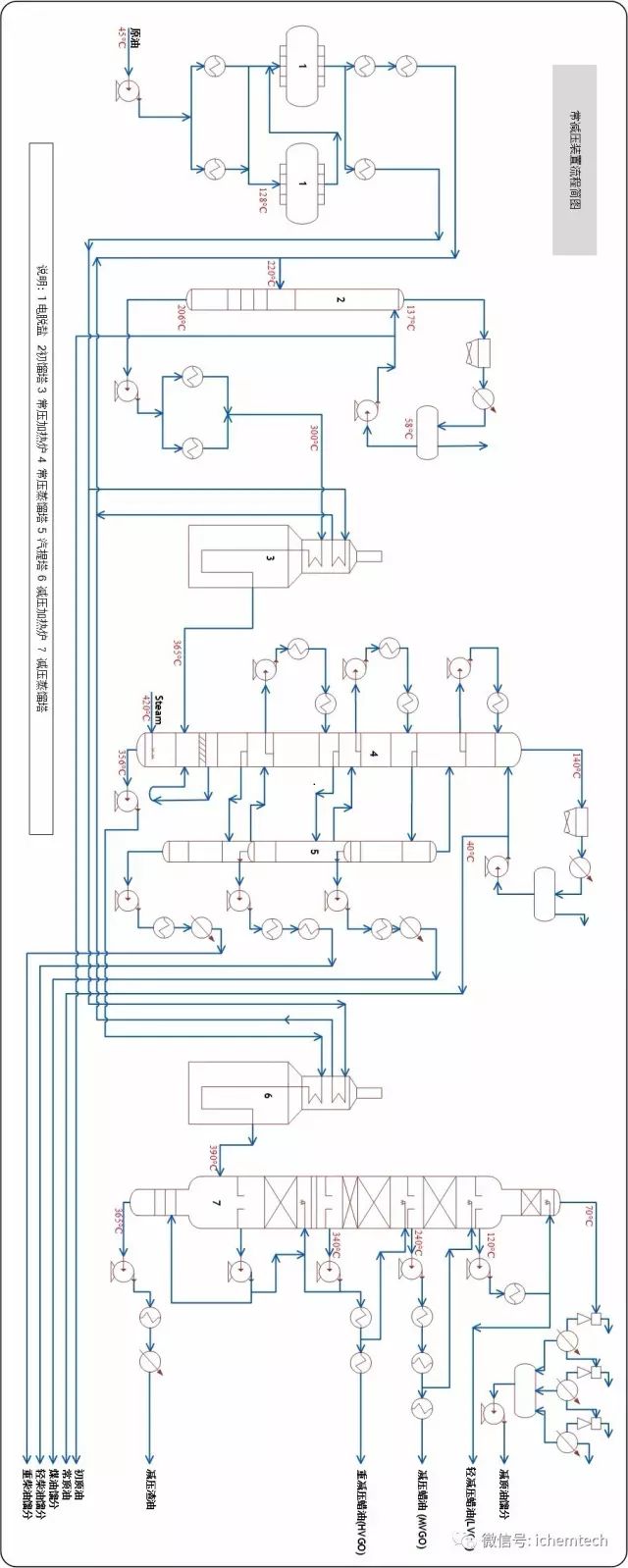
1.2 物料平衡及能耗
1.2.1 物料平衡
表1.2-1 国内某项目常减压蒸馏装置物料平衡
序号 | 物料名称
| 收率 | 数量 | 备注 |
w% | kg/h | t/d | 104t/a |
一 | 入方 |
|
|
|
|
|
| 沙特混合原油 | 100 | 1190476.19 | 28571.43 | 1000 |
|
|
二 | 出方 |
|
|
|
|
|
1
| 气体+损失 | 0.37 | 4404.76 | 105.71 | 3.7 | 燃料气 |
2 | 液化气 | 1.4 | 16666.67 | 400.00 | 14 | 产品 |
3 | 石脑油 | 15.7 | 186904.76 | 4485.71 | 157 | 催化重整原料 |
4 | 常一线油 | 7.62 | 90714.29 | 2177.14 | 76.2
| 航煤馏分、柴油馏分 |
5 | 常二线油 | 12.35 | 147023.81 | 3528.57 | 123.5 | 柴油加氢精制原料 |
6 | 常三线油 | 9.69 | 115357.14 | 2768.57 | 96.9 | 柴油加氢精制原料 |
7 | 减一线油 | 2.85 | 33928.57 | 814.29 | 28.5 | 蜡油加氢裂化原料 |
8 | 减二线油 | 12.82 | 152619.05 | 3662.86
| 128.2 | 蜡油加氢裂化原料 |
9 | 减三线油 | 9.84 | 117142.86 | 2811.43 | 98.4 | 渣油加氢脱硫原料 |
10 | 减压渣油 | 27.36 | 325714.29 | 7817.14 | 273.6 | 渣油加氢脱硫原料 |
| 合计 | 100 | 1190476.19 | 28571.43 | 1000 |
|
1.2.2 能耗
表1.2-2 国内两项目常减压装置能耗
序号
| 项目 | 国内项目A | 国内项目B |
小时耗量 | 耗能指标 | 单位能耗 | 小时耗量 | 耗能指标 | 单位能耗 |
单位 | 数量 | 单位 | 数量 | MJ/t原料 | 单位 | 数量 | 单位 | 数量 | MJ/t 原料
|
1 | 循环水 | t/h | 1800 | MJ/t | 4.19 | 6.34 | t/h | 1950 | MJ/t | 4.19 | 6.86 |
2 | 污水 | t/h | 207.7 | MJ/t | 46.05 | 8.03 | t/h | 99.5 | MJ/t | 46.05 | 3.85 |
3 | 电 | kW
| 8282 | MJ/kW.h | 10.89 | 75.75 | kW | 7800 | MJ/kW.h | 10.89 | 71.35 |
4 | 净化水 | t/h | 40.3 | MJ/t | 7.12 | 0.24 | t/h | 10 | MJ/t | 96.3 | 0.81 |
5 | 除氧水 | t/h | 35.2 | MJ/t | 385.19
| 11.39 | t/h | 18 | MJ/t | 96.3 | 5.82 |
6 | 新鲜水 | t/h | 7.35 | MJ/t | 7.12 | 0.04 | t/h | 3.5 | MJ/t | 6.28 | 0.02 |
7 | 标准燃料 | kg/h | 9440 | MJ/kg | 41.868 | 331.99 | kg/h | 8830 | MJ/kg
| 41.868 | 310.54 |
8 | 0.4MPa蒸汽 | t/h | 5.46 | MJ/t | 2763 | 12.67 |
|
|
|
|
|
9 | 1.0MPa蒸汽 | t/h | 6.65 | MJ/t | 3182 | 17.78 | t/h | 16.5 | MJ/t | 3182 | 44.1 |
10 | 净化风 | Nm3/h
| 100 | MJ/Nm3 | 1.59 | 0.13 | Nm3/h | 300 | MJ/Nm3 | 1.59 | 0.4 |
11 | 热出料/低温热 |
|
|
|
| -68.2 |
|
|
|
| -35.6/-17.6 |
| 合计 |
|
|
|
| 396.17 |
|
|
|
| 390.56 |
|
|
|
| 9.46kg标准油/t原料
|
|
| 9.33kg标准油/t原料 |
注:本表中的数据仅供参考。
1.2.3 核心设备
1.2.3.1 电脱盐罐
装置采用一级或多级电脱盐工艺,每级设一台电脱盐罐,其大小是根据原油在强电场中合适的上升速度确定的,主要要考虑罐的轴向截面积及油和水的停留时间。
脱后原油含盐≯3mg/l,含水≯0.2%。
电脱盐罐排水设除油罐,排水含油≯50ppm。
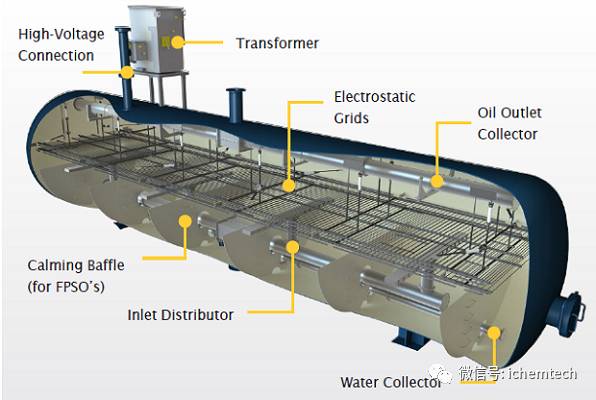
1.2.3.2 分馏塔
减压塔:减压塔主要出催化裂化或加氢裂化的原料,产品较简单,分馏精度要求不高,故只设置2~3个侧线,不设汽提塔。为减少减压塔的全塔压降,降低操作成本,减小塔径,减压塔分馏段全部采用规整金属波纹板填料。为均衡减压塔负荷,减压塔设置三个侧线。减压塔的内件是实现减压塔低压降、高通量和较高分馏效率、较高产品质量和拔出率的关键。目前国内外大多数炼厂的燃料型减压塔,洗涤段常选择防堵规整填料;换热分馏段选择高性能规整填料。
减压蒸馏系统按操作条件,主要分“湿式”减压蒸馏和“干式”减压蒸馏两种。
1.2.3.3 加热炉
常减压装置设置常压炉一台、减压炉一台。通常加热炉炉型有圆筒炉、卧管立式炉和立管箱式炉。
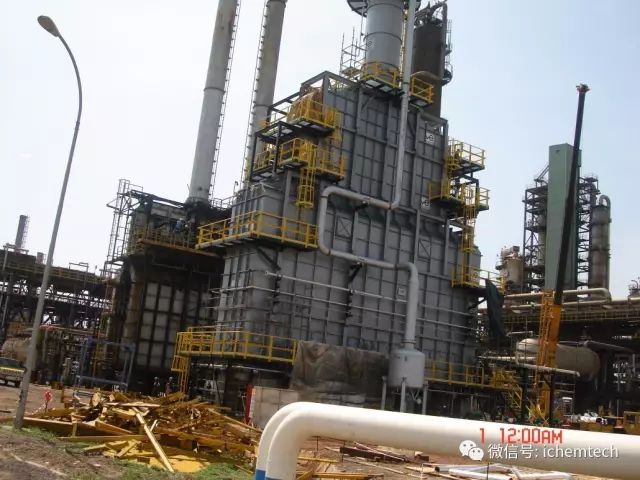
立管圆筒炉。该炉型为 3个辐射室立管圆筒炉,每个辐射室内4管程,炉管附墙布置,为单排单面辐射。多台小能量燃烧器与炉管呈同心圆布置,为底烧结构。 3个辐射室共用一个对流室。被加热介质分12管程从对流室上部进入加热炉,经对流加热后入辐射室。
立管圆筒炉各管程炉管均为单排单面辐射,附墙布置。优点为:每个辐射室有多台燃燃烧器,单台燃烧器有故障时对炉子负荷影响较小,不用停炉。钢结构较简单。缺点为辐射炉管表面热强度不均匀系数比较大,空间利用率低,占地面积大,每个辐射室使用多台燃烧器使炉底风道及燃烧器配管结构复杂,操作维护费用较多;辐射室与对流室之间的转油线和连接烟道长,对流-辐射转油线排管困难,压降不均匀。
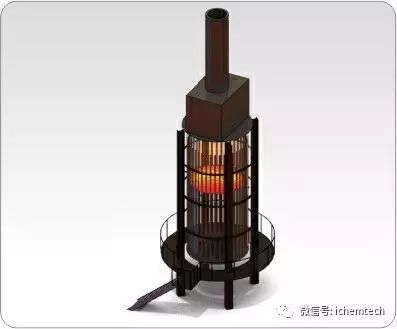
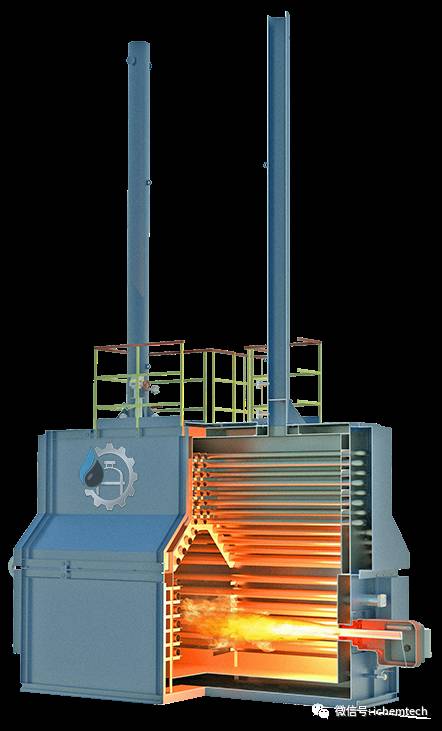
1.2.3.4 主要设备参数
表1.2-3某项目主要设备设计参数举例
序号 | 设备名称 | 规 格 |
1 | 初馏塔 | φ4000/5200×28000(切线) |
2 | 常压塔 | φ7000/φ8200×48000(切线) |
3 | 汽提塔 | φ3000×34000(切线) |
4 | 减压塔 | φ6800/8600mm/11000/5000×46000(切线) |
5 | 一级电脱盐罐 | φ4000×28000(切线) |
6
| 二级电脱盐罐 | φ4000×28000(切线) |
7 | 常压炉 | 78Mw,立管箱式炉 |
8 | 减压炉 | 38Mw,立管箱式炉 |
注:本表中的数据仅供参考。
2.1 污染源及三废
2.1.1 电脱盐单元污染源分析
该单元污染源为一级、二级电脱盐罐产生的含盐废水和机泵噪声。
2.1.2 初馏单元污染源分析
该单元污染源包括初顶回流罐、初顶分水罐含硫废水;空冷、机泵等设备噪声。
2.1.3 常压蒸馏单元污染源分析
该单元污染源包括常压加热炉烟气;常顶回流罐、常顶一级、二级分水罐含硫废水;加热炉、引风机、空冷、机泵等设备噪声。
2.1.4 减压蒸馏单元污染源分析
该单元污染源包括减压炉烟气;减顶分水罐含硫废水;加热炉、引风机、空冷、机泵等设备噪声。
2.1.5 其它污染源分析
各单元设备、储罐因“大小呼吸”产生的无组织废气;机泵冷却,设备及地面清洗产生的含油废水;废机油、废含油抹布等固废。
2.1.6 废水排放
常减压蒸馏装置产生的废水包括含盐废水、含硫废水、含油废水。
表2.1-1 国内某项目常减压装置废水排放
序号 | 污染源名称 | 污水类型 | 产生量 t/h | 污染处理 |
1 | 机泵冷却及地面冲洗排水 | 含油污水 | 5 | 去污水处理厂 |
2 | 塔顶回流罐排水 | 含硫污水 | 34.5 | 去酸性水汽提 |
3 | 电脱盐罐排水 | 含盐污水 | 69.5 | 去污水处理厂 |
注:本表中的数据仅供参考。
2.1.7 废气排放
常减压蒸馏装置产生的废气主要为常压炉、减压炉烟气和无组织排放废气,烟气中污染物主要为二氧化硫和二氧化氮;无组织排放废气主要为非甲烷总烃。
为减少加热炉烟气中污染物的产生和排放,采取源削减和污染治理相结合的方式进行污染防治。
首先,采用脱硫后的催化原料油作为加热炉燃料,为进一步减少SO2 排放,尽量将燃料油改为脱硫后的液化天然气;
其次,采用低氮燃烧器,脱硝效率可达到50 %以上;
第三,烟气有组织高空排放,常压炉烟气和减压炉烟气合并后,由80 m 高排气筒高空排放,通过大气的扩散和稀释,降低污染物对大气环境的影响。
采取加强设备维护,减少静密封泄漏等措施减少装置无组织排放废气的产生。
表2.1-2 国内某项目常减压装置废气排放
污染源名称 | 排放规律 | 排气量 | 污染物 | 污染处理 |
Kg/h |
加热炉燃烧烟气 | 连续 | 159000 | SO2、NOx | 高点排入大气 |
注:本表中的数据仅供参考。
2.1.8 废固排放
常减压整理装置产生的固废主要包括废碱液、废机油和废含油抹布,均属于危险固废,委托有危废处理资质单位处理。
2.2 介质风险因素分析
表2.2-1 国内某项目常减压装置工艺介质危险因素分析
介质名称 | 沸点/℃ | 闪点/℃
| 自燃点/℃ | 爆炸极限(体积)/% | 爆炸危险类别 | 火灾危险类别 |
下限 | 上限 | 类别 | 组别 |
原油 |
| 6.67~32.2 | 350 | 1.1 | 8.7 |
|
| 甲B |
石脑油 | 36~68 | <-20 | 480~510 | 1.2 | 6 | ⅡA | T3 | 甲B |
汽油 | 50~150 | -58~10
| 415~530 | 1.1 | 5.9 | ⅡA | T3 | 甲B |
煤油 | 175~325 | 43~72 | 210 | 0.7 | 5 |
|
| 乙A |
柴油 | 280~370 | 50 | 257 |
|
| ⅡA | T3 | 乙B |
蜡油 |
|
|
|
|
|
|
| 丙B |
重油
| 300~350 |
| 380~420 | 1.2 | 6 |
|
| 丙B |
液化石油气 |
| -74 | 400 | 1.5 | 15 |
|
| 甲A |
干气 |
| 气体 |
| 1 | 13 |
|
| 甲 |
氨 | -33 | 气体 | 630 | 15 | 28 | ⅡA
| T1 | 乙 |
硫化氢 | -60 | <-50 | 270 | 4.3 | 45.5 | ⅡB | T3 | 甲 |
二乙醇胺 |
| 135 | 265 | 0.9 | 8.4 |
|
| 丙B |
注:本表中的数据仅供参考。
表3.1 国内某项目1000×10⁴t/a常减压蒸馏装置工程费用估算表
序号 | 工程项目或费用名称 | 设备
购置费 | 安装费 | 建筑 工程费 | 其他 | 合计 万元 | 占工程费用 | 含外币金额 |
|
|
(%) | (万美元) |
| 工程费用 | 42360 | 35953 | 1879 |
| 80192 | 100.00% | 550 |
1 | 总图运输 |
|
| 241 |
| 241 | 0.30%
|
|
2 | 建筑物 |
|
| 802 |
| 802 | 1.00% |
|
3 | 构筑物 |
| 5318 | 777 |
| 6095 | 7.60% |
|
4 | 静置设备 | 25255 | 4392 |
|
| 29647 | 36.97% | 180 |
5 | 机械设备 | 5165 | 312 |
|
| 5477
| 6.83% | 170 |
6 | 工业炉 | 67 | 8289 |
|
| 8356 | 10.42% | 70 |
7 | 工艺管道 |
| 10401 |
|
| 10401 | 12.97% | 30 |
8 | 电气 | 4878 | 3390 |
|
| 8268 | 10.31% |
|
9 | 通讯 | 182 | 59
|
|
| 241 | 0.30% |
|
10 | 自控仪表 | 5857 | 3044 |
|
| 8901 | 11.10% | 100 |
11 | 给排水 |
| 205 | 60 |
| 265 | 0.33% |
|
12 | 采暖通风 | 110 | 107 |
|
| 217 | 0.27% |
|
13 | 热工 | 847
| 436 |
|
| 1283 | 1.60% |
|
注:本表中的数据仅供参考。
4.1 专利商及技术简介
4.1.1 电脱盐技术
目前成熟的原油电脱盐技术有低速电脱盐及高速电脱盐两种。与低速电脱盐相比,高速电脱盐技术具有脱盐效率高、单罐处理能力大、电耗低等优点。国内外电脱盐技术主要有以下几种:
交流电脱盐(传统电脱盐)—全阻抗交流变压器、水平电极板、水相进料;
高速电脱盐—全阻抗交流变压器、水平电极板、专用分布器、极板间油相进料,Petreco Bilectric技术;
交直流电脱盐—
NATCO技术,全阻抗双频交直流变压器、垂直电极板、水相进料;
长江(扬中)电脱盐设备有限公司,全阻抗交直流变压器、垂直电极板、水相进料;
脉冲电脱盐—中石化洛阳工程有限公司,全阻抗脉冲变压器、水平电极板、水相进料。
其他原油电脱盐技术—双极电脱盐(NATCO技术)、鼠笼式电脱盐、双进油双电场电脱盐。
技术链接:http://www.lpec.com.cn/showme.asp?id=57
技术链接:http://www.santacc.com/products_list/pmcId=30.html
技术链接:
http://www.slb.com/services/processing-separation/oil-treatment/dehydration-desalting.aspx
技术链接:http://www.howebakeruk.com/
技术链接:
https://www.bakerhughes.com/products-and-services/downstream-chemicals/refining/desalting-optimization
4.1.2 常减压技术(开放技术)
常减压蒸馏技术基本是炼油行业中公开的工艺技术,各大石油公司或工程公司均有自己独特的自有技术,在这里仅列出了部分工艺技术及其提供商,供参考。
技术链接:http://www.lpec.com.cn/showmeview.asp?id=55&sid=47
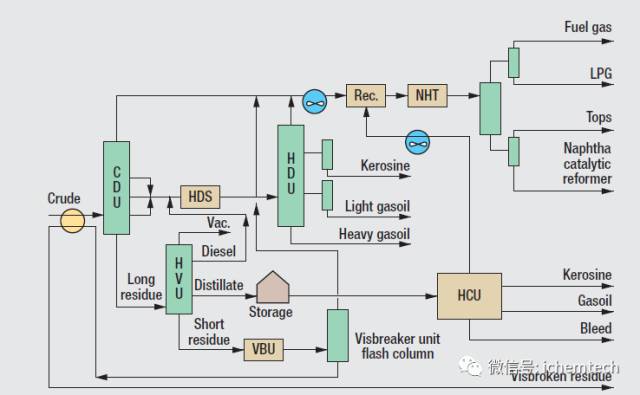
SHELL的高真空减压蒸馏技术(HVU)
减压渣油切割点温度已达到610℃,减压加热炉出口温度可达到440 ℃,减压塔闪蒸段压力可达到22mmHg;
减压塔中段回流采用空塔喷淋技术,减压塔压降可以达到7mmHg;
减压塔进料采用Schoepentoeter;
减压塔进料段采用一段洗涤,抽出集油箱采用特殊结构;
减压炉采用特殊设计,炉出口温度可以达到440 ℃,连续运行时间可以达到4年以上;
技术链接:http://www.shell.com/business-customers/global-solutions/refinery-technology-licensing/distillation-and-separation-technologies.html
KBC减压深拔技术
KBC已开发出连接各装置形成全炼油厂模拟的模型软件(PETROfine/Petro-SIM)
每个炼油物料由一组含有75个假定组份的分析所描述;
每一假定组最多能存储77个物理性质;
对于减压深拔项目,记录的关键物理性质有残炭、C7不溶物(沥青质)、硫、氮和金属;
KBC设计的工业化装置已达到:北海原油(API 39)切割点达到620℃,中东原油(API 34)610℃,重油如Bachaquero BCF-17、Merey-16和Maya原油565℃;
使用KBC深拔技术减压加热炉出口温度已成功操作在高达435℃;
技术链接:http://www.kbcat.com/process-simulation-software/refinery-simulation
参考文献:
《炼油装置工程设计》中国石油大学出版社
《炼油厂设计与工程》中国石化出版社
------------------------------------------------------------------------------
如需转载或有疑问,请邮件联系[email protected]