本文主要介绍了车用聚丙烯(PP)的应用及其改性研究的进展,包括连续增长态势、主要应用部位以及改性研究的多个方面。文章还展望了未来车用PP的改性研究方向和市场需求,并推荐了相关活动。
2021年中国汽车产量为2652.8万辆,2022年为2718.0万辆,2023年为3016.1万辆,呈现连续增长态势。
聚丙烯(PP)是一种综合性能优良的通用热塑性塑料,具有价格低廉、质量轻、耐溶剂、易回 收、无毒等特点,是重要的车用轻质材料。聚丙烯复合材料注塑成型可以制备仪表板、立柱、杂物箱、门板等汽车零部件。
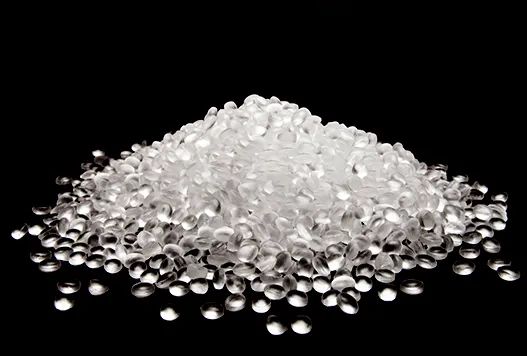
图源: 赛安化学
我国汽车主要应用塑料的统计数据表明,各类改性聚丙烯(PP)材料在汽车上应用量最大。到2025年,考虑汽车轻量化应用发展及PP性能提升,我国车用PP质量可增加至每辆80kg,PP总量将达到280万吨。
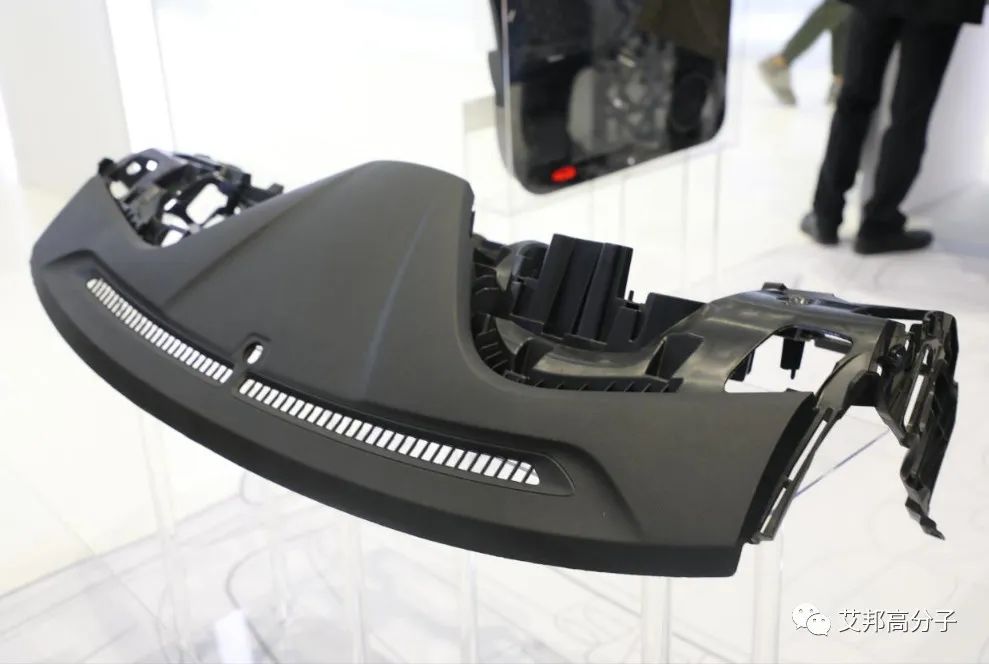
PP改性材料应用于仪表板
一 车用PP轻量化发展
轻量化是汽车工业未来转型升级的必经之路,汽车内外饰已逐步实现塑料化,而车身、车架等主要结构件仍以金属材料为主,汽车轻量化的发展潜力广阔。目前,通过薄壁化、微发泡及吹塑等方式减重备受关注。
1. 薄壁化
一般薄壁制品的尺寸满足壁厚小于1mm且表面积大于50cm2;或是长径比大于100(或150),由于模腔空间尺寸严苛,注塑时易出现严重的收缩。
青岛国恩科技股份有限公司公开了一种低密度聚丙烯的制备方法,该材料的熔体流动速率33.0g/10min,拉伸强度23.2MPa,弯曲强度30.0MPa,弯曲模量1650MPa,悬臂梁缺口冲击强度35.0MPa,密度0.9g/cm3。TVOC含量为3.6mg/m3,气味等级为2.0级。该材料密度低,流动性强,具备高刚性和高韧性的综合力学性能,能够制备薄壁化汽车内饰材料。
林友平等通过氢调法制备高熔体流动速率PP薄壁注塑专用料,该产品弯曲模量不小于1600MPa,达到客户设计指标和加工要求,已规模化生产。
Keisuke等探究了薄壁PP零件的注射工艺与性能的关系,在较低的注射速度下有助于PP分子取向,薄壁产品可获得较高的断裂韧性。
许冰系统分析了长玻纤增强PP(LGFPP)薄壁制件不同部位的玻纤结构与性能。在填充模腔过程中,熔融的PP流动性强于玻纤,远浇口端与模具边缘温度较低,PP快速冷却,而玻纤在不断更新的熔体推动下聚集,含量提高。另外远浇口端的玻纤由于流程增长而发生较多折损,保留长度降低,近浇口端由于长时间保压,玻纤长度也严重受损。中间位置拥有最长的玻纤保留长度,且此处的玻纤因熔体快速流动而高度取向,拉伸强度最强。
2. 微发泡技术
陈明等综述了微发泡PP材料的改性研究,PP的半结晶相结构和较低的熔体强度使其发泡性较差,引入均匀分布的其他粒子,在基体内充当异相成核点,形成的良好分散增大熔体强度,二者协效促进PP发泡。
PP发泡
Wang等使用纤维素纳米纤维(CNFs)改善PP发泡性,细小的纤维结构诱导PP结晶温度提高,形成大量微晶成核点,熔体黏弹性增强防止泡孔破裂合并,当添加5%质量分数的CNFs时发泡性最佳。
陈明等深入探究了热塑性弹性体(POE)对PP微发泡材料综合性能的影响。POE粒子在基体中提供有效异相成核点,形成大量微晶,添加质量分数10%时,发泡均匀,泡孔平均直径约60μm。另外,由于POE与PP分子链间相容性好,互相缠结形成良好有序的网络结构,可使材料松弛时间变长,熔体黏弹性显著提高,为发泡提供有利条件。
3. 吹塑
一些需要纵向拉伸的车用轻量化零件可以通过吹塑工艺制备。PP在高温状态下的熔体强度低,拉延率不高,限制了PP在吹塑工艺上的实际应用。
天津金发新材料有限公司公开了一种PP复合材料的制备方法,可以提高材料在高温状态下的拉延率,解决零件吹破的问题。该材料200℃时的熔体强度和拉延率分别为203MN,274%,190℃时的熔体强度和拉延率分别为90MN,747%,说明该材料在高温时具有优异的熔体强度和拉延率,能够制备车用零部件。
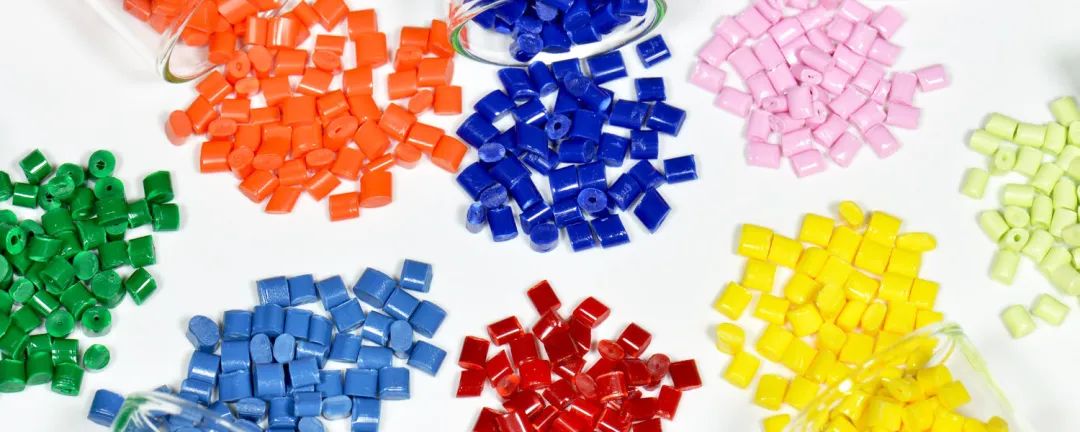
PP复合材料 图源:冠华股份
二 车用PP美观与环保化发展
随着大众消费观念的不断改变,汽车件的外观、耐久、舒适、环保等方面的设计指标对材料提出了更高的要求,促进了改性PP研究的蓬勃发展。
1. 高光泽
Lee等利用3种粒径的BaSO4改善PP光泽度,发现随填料粒径减小,PP表面平整性提高,增大了光反射作用,表面更光亮。同时开发了另一款硅灰石(CaSiO3)填充的新型高光泽PP,两种树脂注塑件表面光泽度基本持平,而新型树脂的优势在于注塑模温比常规树脂模温低30℃,有效缩短成型时间,节约能耗。
沈叶龙等发明了一款高光泽玻纤增强PP复合材料,利用10份云母替代玻璃纤维,改善了材料表面浮纤问题,显著提高光泽度,基本保持同等的力学强度。添加接枝的PP增加了玻璃纤维与基体的相容性,进一步抑制纤维外露问题。该材料适用于注塑成型车用高光泽、高强度、高抗冲的PP制品。
董莉等探讨了成核剂对高光泽透明PP的作用机理与发展。目前研究最成熟的是二苄叉山梨醇类成核剂,其分子链中氢键自聚集作用形成三维网状结构,比表面积增大,异相成核快速引发结晶,晶粒尺寸微细化,显著提升了PP表面光泽及透明度。结构中存在的极性官能团,与PP具有良好的相容性,力学性能也明显提高。
美国Milliken最新推出HPN-20E超级成核剂,赋予PP多方位的优异性能,广泛应用于家用电器、汽车等领域。国内上海晟霖公司,上海重汇公司等产品也达到了国际先进水平。
2. 耐刮擦
耐刮擦性是汽车仪表板、操控台、门板等内饰件的关键性能。
朱春州等研究了PP配方体系对耐刮擦性能的影响。高结晶均聚PP相较于共聚PP,分子规整度高,抗刮擦变形破坏的能力更强,十字划格试验中表现出“轻划形貌”,划痕表面平坦,划痕宽度与色差(ΔL)值较低。POE对材料的力学性能降低较多,表面硬度更低,受到刮擦力后PP出现“移除形貌”,ΔL值更大。当加入PP-g-MAH(马来酸酐)相容剂,使PP与硅灰石达到分子级的紧密相容,二者形成良好界面结合,减少了界面变形初期产生的龟裂,增强了PP的耐刮擦性能。
王滨等探究了滑石粉对PP耐刮擦性的影响。研究表明滑石粉具备水油“两亲性”和润滑性,能与PP良好相容,降低了PP表面摩擦系数,有助于提升耐刮擦性。随滑石粉添加量增多,在PP中分散性变差,容易出现聚集、不均,导致材料耐刮擦性下降。当滑石粉的粒径减小,尤其5μm以下,PP的耐刮擦性显著改善。但小于1μm的超细粉由于表面能的提高造成分散困难,反而更易出现刮擦发白现象。
3. 低气味/低散发
汽车在40℃高温长时间暴晒时,车内温度急剧上升,普遍在60℃以上,太阳直射部分最高可达90℃,致使塑料内饰件中挥发性有机物(VOC)逸散,严重影响了驾车体验。
为解决现有汽车内饰材料在高温时气味大的问题,金旸(厦门)新材料科技有限公司公开了一种车用PP内饰材料的制备方法,该车用PP的密度为1.038g/cm3,熔体流动速率为19.3g/10min,拉伸强度为19.5MPa,弯曲强度为29MPa,弯曲模量为1856MPa,缺口冲击强度为41kJ/m2。按照大众汽车气味检测标准VW'sPV3900E—2019测试的气味等级为3.0级,制件表面温度39℃。使用该PP可有效降低汽车内饰材料气味和车内温度,提升驾车体验。
上海普利特复合材料股份有限公司提供了一种低气味、低VOC含量的PP复合材料的制备方法。该PP复合材料的拉伸强度28.9MPa,弯曲模量2330MPa,简支梁缺口冲击强度8.5kJ/m2,按照GMW3205—2011车内装饰材料气味测试方法测试,气味等级为6.5级,总挥发性有机物(TVOC)4190μg/m3,应用于汽车内饰材料可以降低车内气味和VOC逸散。
普利特改性PP应用展示 图源:普利特
为提升PP性能往往通过添加助剂来实现,但助剂固有的挥发性,导致制品不能满足气味指标要求。
余林华采用耐刮擦剂V-Si4042复配气味吸附剂PY88TQ制备汽车内饰用PP材料。V-Si4042主要成分为聚硅氧烷,可在材料表面形成润滑层,降低表面摩擦系数。单独添加质量分数1.5%的V-Si4042,PP已不能分辨出刮擦痕迹,显示出较好的耐刮擦性,但气味与挥发性有机化合物(VOC)散发等急剧上升。加入质量分数为1.0%的PY88TQ,其三维多孔结构经表面活化处理可分解或螯合气味小分子基团,此时PP同时满足良好的耐刮擦与低散发要求,已成功推广用于一汽大众、通用福特等车型。
Brodzik检测了3种不同汽车内饰部件(遮阳板、车顶衬和手制动杆盖)的VOC排放,发现各零件单独测试VOC浓度均高于整车测试条件下的结果,材料间存在着协效吸附作用,有利于减弱汽车内部VOC散发。
李秀峻等探究了汽车工业中常用的螺杆挤出双抽真空脱挥法的有效性,PP熔体与挥发性有机物存在“吸附-解析”平衡,还需进一步通过延长高温烘料时间降低材料VOC,由于分子链在高温下运动加剧,自由体积扩大,且熔体黏度降低,利于挥发物扩散释放。在130℃烘烤4h后材料VOC含量降至7768μg/m3,满足汽车零部件对PP材料低挥发的要求。
4. 无卤阻燃
PP在汽车工业的应用已广泛扩展,提高其阻燃特性并达到无卤环保要求,对提升整车安全性意义重大。
无卤阻燃PP 图源:美泰塑胶
姜向新等采用聚磷酸铵(APP)/三嗪(CFA)/三聚氰胺(MCA)体系组成的膨胀型阻燃剂,当阻燃剂质量分数为25%时,试样表面形成牢固的多孔疏松炭层,有效阻遏热量释放和传递,隔绝氧气和可燃气体,将材料氧指数提高至36%。在燃烧过程中,提高阻燃体系中CFA的比例,使得残炭量提高,形成致密的炭层,提升氧指数值。
叶淑英开发了一款新能源汽车电池包上盖专用PP材料,添加质量分数为20%的无卤阻燃剂,材料达到V-0等级。由于无卤阻燃剂中哌嗪基团具有优异的成炭性,相比传统阻燃剂用量减少,原料成本下降,力学性能的削弱也得到缓解。阻燃剂将PP的初始降解温度降低38℃,利于其形成泡沫炭层,同时阻隔PP继续降解,材料热稳定性提升。再使用质量分数10%的POE-DF610进行增韧,材料冲击强度达到25.5kJ/m2。
三 车用PP高性能发展
1β成核增韧
随着汽车保险杠、仪表板、立柱等对PP材料冲击韧性要求进一步提升,添加少量的β成核剂增韧,价格低廉,操作灵活便捷,显示出巨大的潜力。
窦强等对比了添加质量分数0.1%的β成核剂与橡胶对PP的增韧效果:β成核剂将纯PP的缺口冲击强度提升2.6倍;相比橡胶增韧保险杠专用料,拉伸强度保持率高出30%,热变形温度、弯曲强度等指标均更优。
Ghoshal利用顺丁烯二酐接枝PP改善PP/碳纳米管(MWNT)的界面结合,形成良好分散的纳米复合材料中可以观察到β晶体,仅使用质量分数1.0%的MWNT,PP的冲击强度增加了152%,且基本维持原本的柔韧性。
常用的β成核剂包括芳香族二酰胺类(如TMB-5),杜海南等探究中,当添加TMB-5质量分数为0.05%时,PP冲击强度最高为9.2kJ/m2,较原始PP增长150%,继续增加用量,强度快速回落,质量分数超过0.20%后与基体韧性接近。TMB-5在PP中分散性好,生成疏松、完善的β晶,表现出最优的冲击韧性,而高于临界浓度后,TMB-5含量增加形成“捆束”状晶体,冲击韧性下降。
2 碳纤维增强
随着新能源汽车及轻量化发展,碳纤维(CF)增强材料具有轻质、高模、比强度大、耐高温等一系列优点,在汽车行业的应用得到广泛关注。
三井化学 TAFNEX™CF/PP材料 图源:三井化学
北欧化工推出3款CF/PP增强材料,适用于汽车大灯面罩、泵壳、座椅骨架、天窗框等部位。福特2018年发布的多用途SUV车型中,A柱支架使用了Boreali公司商业化的再生碳纤维复合材料产品,纤维质量分数仅为6%,有效减重14%,材料各项性能满足要求,每年降低成本约18.6万美元。
李思宇等将去浆碳纤维浸入浓硝酸氧化处理,再挤出造粒得到PP复合材料。研究表明,改性的短切碳纤维(NCF)表面存在羟基、羧基等活性官能团,表面粗糙纹路加深,与基体的缠结作用力增大,NCF与PP间界面性能良好。当NCF质量分数为15%时,纤维可形成良好分散,复合材料拉伸强度相较纯PP提升92%,弯曲强度提升220%,缺口冲击强度提升160%。
四 车用PP改性研究展望
随着能源和环保问题日益严峻,汽车工业积极响应可持续发展要求,“以塑代钢”具有长远的意义,改性PP作为主选塑料材料,需求前景广阔,经济效益巨大。汽车的广泛普及极大地增多了用户与车辆的交互,从视觉、触觉、嗅觉等方面对材料提出越来越严苛的要求,如内饰减少应力发白,表面抗静电,长时间光照下抗发黏等等。
现代高分子研究进步飞速,成核剂、改性剂等更新加快,纳术技术、塑料合金化、原位反应挤出等新技术与工艺迅速发展,为PP改性创造了更多可能的空间。因此,加强对PP的改性研究,开发出适用性更广,功能性更强的PP材料,将是未来长期关注的焦点。
参考资料:车用聚丙烯材料改性技术的研究进展,祁蓉;聚丙烯复合材料在车用内饰件中的应用研究进展,云宁
在艾邦高分子2024年12月12日在深圳举办的“第九届工程塑料创新应用论坛”论坛上,来自金发科技的汽车聚烯烃技术经理陈嘉杰将为大家带来车用PP相关报告,欢迎与会讨论!
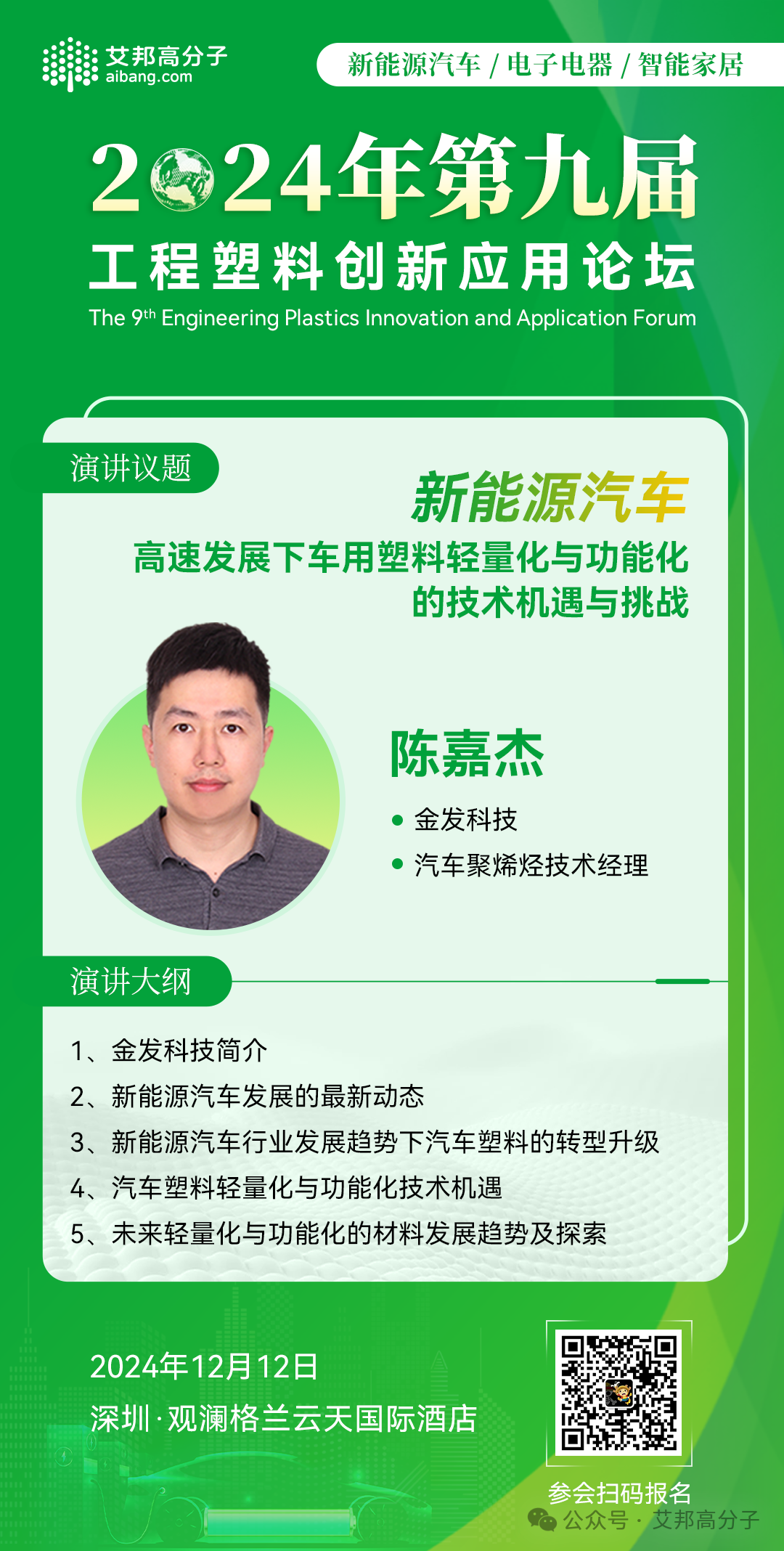
欢迎加入艾邦聚丙烯PP产业交流群:
活动推荐:2024年第九届工程塑料创新应用论坛(12月12日 深圳)
议题安排:
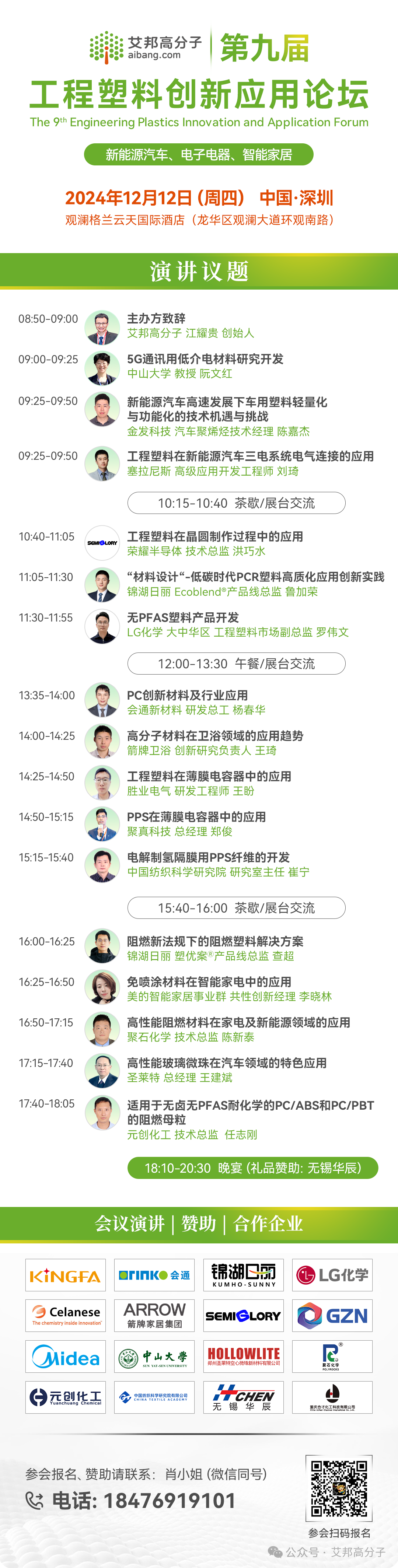
报名方式:
方式1:请加微信并发名片报名
肖小姐:18476919101(同微信)
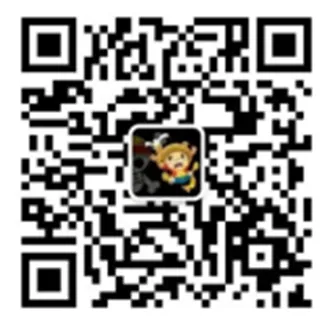
邮箱:[email protected]
方式2:长按下方二维码在线报名
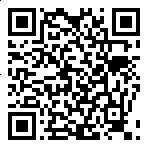
https://www.aibang360.com/m/100220?ref=172672
阅读原文,在线报名