一、背景
某物流人老K,物流科班出身,自认为精通了仓库管理。一年前接手了一个商超配送仓库,因为上游老板是做快消品批发的,ERP用的是某家婆软件。
在“统仓统配”的模式诱惑下,上游老板把仓配功能外包给了老K所在的物流公司。为了顺畅做业务交接,老K曾极力要求公司老板上一套WMS。
老板一开始其实是拒绝的,一方面是一套WMS要价几十万,业务还没开展就大笔的支出(这不符合老板的价值观);另一方面你不能让我买,我就马上去买,那我老板的权威哪里去了(这不符合老板的人生观)。
结果是老板希望直接用批发商的ERP,理由是既然批发商原有团队能管好,那老K你这专业物流团队更应该能管好。由此也开启了老K的苦难历程。
二、 第一重难(WMS与ERP的本质区别)
五千多个SKU,搬库完成后第二天就开始要求发货了。但因为原ERP里没有记录商品的库位,发货第一天就抓瞎了,每天有几百票要货订单,平均每个订单在50个SKU左右,他们在哪?
老K带领着库管员开始了无休止的“找你妹”工作。一周后,包括老K在内全部眼圈发黑的团队向老板发出了红色警戒,发货没法完成,加班没用,业务要崩盘。老板的淫威变成了困惑,我们不是专业团队么,做同样的事情怎么还不如草台队伍效率高。
于是物流老板找到了批发企业老板取经(不耻下问):“你们以前是怎么做到的”。批发老板说了一句话:我的员工都跟了我十几年,哪个物品在哪个地方他们闭着眼睛都能找到,但我也陷入了严重的员工依赖,我害怕他们突然请假或离职,只能好吃好喝好工资伺候着。所以才要找你们专业人士来管理啊。
批发老板的话,令物流公司老板不得不重新考虑这个项目的管理模式。老K趁机向老板献策,提高拣货效率是关键;而提高拣货效率,首先必须要让员工知道货物在哪里;在员工不熟练的情况下,要想熟知货物位置,必须要借助WMS来管理;这是专业物流管理人员与草台班子的本质区别。
“君子性非异也,善假于物也”;专业人士如果失去了专业工具,可能还不如愚夫莽汉。工欲善其事必先利其器,否则就得不偿失;物流老板也终于开窍,WMS顺利上线(此处省略上线过程中的辛酸苦辣十万字)。
三、非此即彼,先进先出的两种管理模式
自从引进了WMS实现了货位管理,即使是新招聘的员工,也能根据拣货指令迅速的找到对应的货位。员工们从此腰不酸了腿不疼了,干活更带劲了。基本解决了拣货效率问题,降低了对熟练员工的依赖,业务算是基本站住了脚。老K也终于松了一口气。
这时批发老板提出了进一步的要求,能不能帮忙实现先进先出管理。原因是以前出现过不少压在里层的货物,拣货员出货的时候基本都从外层拿,管也管不住,导致里层货物出现“过保质期”。
对于WMS来说,先进先出功能是标配,这点老K很清楚,所以毫不犹豫的就答应了客户的要求(服务是无止境的,服务越多则与客户的紧密度越高)。
经过老K和软件供应商的沟通,对于先进先出的管理,有两种管理模式:
一种是批次混存方式,也就是不同的批次相同商品允许存放在同一个货位上,这种情况必须要通过标签来区分,否则员工根本没法辨别出来;当然即使有了标签,如果拣货人是近视远视青光散光色盲之类的,也可能辨别不出来。
第二种是批次排他方式,也就是相同商品的不同批次,不允许放在同一个货位上,而必须放在不同货位上,通过货位来做批次隔离。如果采用第二种方式,是不需要批次标签的,因为先进先出体现在货位上,按照指定的货位来拣货,就肯定是先进先出的。
两种模式各有利弊,第一种模式货位利用率高,但打印标签和识别标签,增加了拣货员的工作量和判断失误的可能;第二种模式货位利用率低,但不用打印标签也不会存在识别差错。
老K将结果向老板反映,经过权衡,老板确认了选用批次混存的方式(在经济利益面前,员工就辛苦一点吧)。
对仓库管理来说,增加的工作仅仅是入库时标记一下每次入库的批次(贴入库日期的标签),出库的时候WMS会自动按照先进先出指定拣货的批次标签,按照标签出库就行了。
无非是写一个标签,这也许会增加一点仓库现场的工作量(不管这个标签是手写还是通过电脑打印),但在效益面前,增加的工作量可以忽略不计了
四、先进先出的歧义
本来以为解决好了的先进先出,老K从此能过上幸福美满的生活。但正所谓人生不如意十之八九,物流人的宿命,解决了一个问题,后面八九个问题随之而来。
有一天送货到某便利店,便利店老板以货物批次较老为由拒收。老K就有点莫名其妙了,我们都是按照先进先出做的啊,怎么可能坑你呢。
和客户讲道理,当然是无解啦;只好请出批发商老板,擒贼先擒王嘛。批发商老板道出了问题的根源:这个品牌供应商的商品,入库的时候就不是按照生产日期先后来入的,有时候先入库的是后生产的,有时候后入库的是很早之前生产的。

老K一脸的惊诧,这样也行么,说好的先进先出呢,如果供应商不按照先进先出的游戏规则来,那我们做先进先出还有啥意义。
批发老板对老K的感叹表示理解,在供应链领域里,上游不按规矩做的事情,反倒要下游来按规矩做,这种情况很常见。不用问什么,就是因为你是乙方。
遇到这种不按规矩出牌的,老K心里的委屈有谁能理解;无奈只好求助WMS服务商。服务商给的答案很简单,针对这个商品,可以单独按照生产日期(或批次号)来做先进先出,而不像以前那样按照入库日期做先进先出。这样就彻底解决了上游供应商不按规矩出牌的问题了。
办法虽然有了,但在实际操作中,需要针对该供应商的商品,单独打印生产日期/生产批号标签,这也增加了业务的多样性和复杂性。对于这点麻烦,在物流行业其实不算什么啦。
本来就是要通过精细化管理实现降本增效;也正是通过多样化和精细化管理来体现团队和公司的价值。老K庆幸又迈过了一关。想躺着就赚钱的,不适合在物流行业里呆着,这点老K是深有体会。
五、特定批次怎么办
人无百日好,花无百日红;过了几天安稳日子的老K终于又迎来了一次客户的投诉。
这次是送办公家具,送到客户那后不多久,客户说安装不上要求退货。老K就纳闷了,你安装不上,怪我咯?核对一下出库指令,收货人、时间、SKU,都没有问题的;先进先出也是约定好的。
实际上,对于家具类商品来说,先进先出并不是很敏感的啊。没办法,老K还是要去找批发老板了解情况。
原来客户要的这批办公家具是定做的,样式和标准款是一样的,只是因为客户办公室空间不足,在尺寸上要求比标准样式款稍微小一点。
因为款式一样,供应商也懒得对这次定制业务创建一个新的SKU,就沿用了原来的SKU代码。如果按照先进先出,很可能就把标准款发给客户了,而标准款因为尺寸大,所以客户安装不上。
实际上,这个出库单的备注里也注明了这个客户“专供”,一方面是发货要求没有说清楚,没有强调客户专供的具体含义;另一方面也是仓库员工没有注意到单据备注里的特殊含义。说到这里,其实就是各打八十大板了。
问题不可怕,关键是要找到问题发生的原因,办法总是比问题多的。解决办法其实很简单,就是新建一个SKU,那么就一切搞定。
但客户坚持用特定批次来区分,老K也表示很无奈,也来不及指责客户不按规矩出牌了。批发老板也是很诚恳的希望物流公司这边给出其他更具体可行的解决办法,以确保以后不会发生类似的问题。
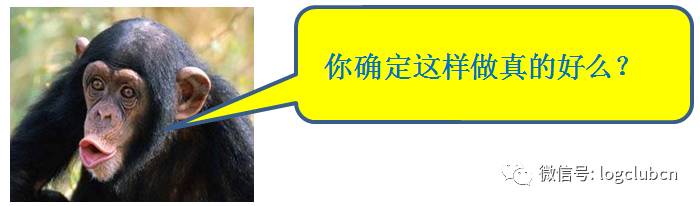
纯靠人为是肯定控制不住了,仍然是把希望寄托在WMS上。其实WMS是有特定批次管理的,针对特殊定制问题,服务商给出了解决思路:
首先,特殊定制的物品,一定要在入库时在“批次号”上标记特殊定制的批次。
其次,特殊定制物品,入库后一定要进行锁定(冻结),以防止其被先进先出规则发货。
第三,发货时,一定填写定制批次号,并要求必须要按照指定批次发货。如果指定批次不存在,则不允许发货。
第四,指定批次发货前,要求先对锁定的该批次解锁;同时尽量不要同时操作该SKU的其他出货单。
一场虚惊,终于是有惊无险,老K揪着的心也终于放松下来。要求员工适应更多的特殊情况是肯定的了。谁以后再说仓库要实现无脑化管理,估计老K第一个就会跳出来说对方没脑子。
六、被“三六九等”了的先进先出
批发老板满脸凝重的找到了老K,“对于某品牌奶粉,我的客户里面有的是VIP客户,我想把生产日期比较近的给他;而对于重要的大客户,我想把生产日期稍远的给他;至于那些中小批发客户,我想把生产日期最远的给他。当然啦,我仍然希望遵循先进先出原则。”
老K开始听的有点糊涂了,对于关系好的客户,你要突破先进先出规则,给他生产日期靠近的;这个我能想办法通过手工拣货来挑选;但为啥又要遵循先进先出,这不是矛盾么。批发老板后面的解释才让老K明白了要求。
简单的说,对VIP客户,执行3个月内的先进先出,也即是说,针对生产日期是3个月之内的做先进先出;对重要客户,执行6个月内的先进先出;而对于普通客户,执行标准的先进先出。
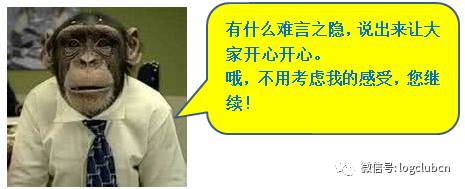
这就好理解了,因为批发商对自己的客户分了三六九等,所以对执行的业务规则也按照三六九等来处理。基本的解决方案就是:
对于VIP客户,只从生产日期是3个月以内的商品里拣取,并且遵循先进先出原则;
对于重要客户,只从生产日期是6个月以内的商品里拣取,并遵循先进先出原则(当然如果刚好库存商品都是3个月以内的,那就相当于重要客户享受了VIP客户的待遇);
对于普通客户,则按照标准先进先出处理(为啥我们去农贸市场买的东西都是生产日期靠前的,原来根源在这里呢)。
找到了原理,顺便也就找到了解决办法,只要WMS里能支持就行啦。如果不是批发老板提出来,可能老K怎么也想不到还有这么多“奇葩”要求。
七、先进先出与拣货效率“势不两立”了
在刚开始开展业务的时候,就有员工反映,WMS给的拣货指令单里,本来明明是一整托的,但它就是要你拆托,先从别的地方拿点零头的,剩下的从整托里拆。然后下一次发货,也是整托的,又要你从剩下的零散里拣货,再拆一托;这种做法会明显影响拣货效率的。
业务刚开始时,老K关注的是客户需求调整,还没来得及考虑这个问题。但随着业务规模越来越大,整托被拆的问题越来越多。
分析造成这种状况的原因:发现在库存里,零散部分的生产日期靠前,而整托部分的生产日期靠后;按照先进先出规则(如果不考虑其他条件约束),零散的(生产日期靠前的)要先出货,剩余的部分则从整托里拆。
如下图所示,拣货100个(一整托),如果按照标准的先进先出法,则会造成将一整托的出货拆成零散出货。
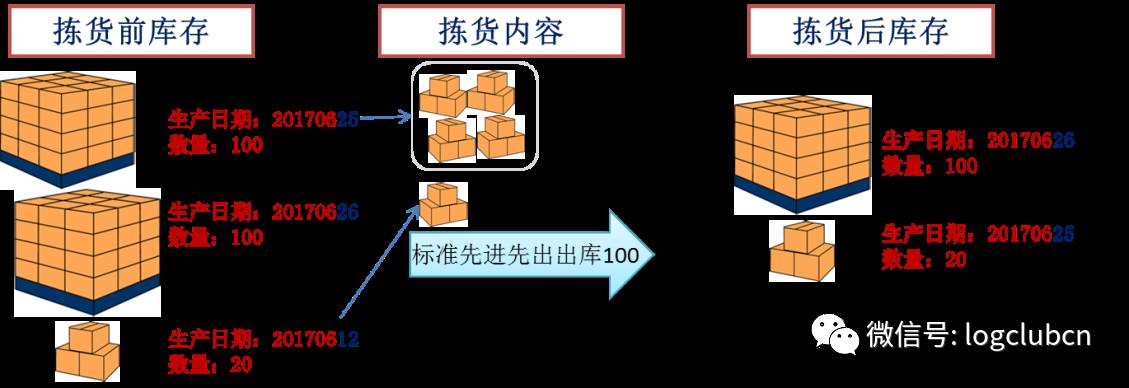
先进先出很重要,但如果遇到严重影响了作业效率的时候,能不能有两全其美的办法呢。以往的工作经验,可能会有不少服务商表示无奈:要么就严格按照先进先出,要么就按照效率优先,两者很难兼容。
天下事有难易乎,科班出身的老K是不信邪的。想出了分两条腿走的办法,既要保证先进先出的原则不打破,又要保证整托出货的拣货效率。那么这个原则是怎么约定的呢:
首先,如果出库数达到有整托的,先从库存的整托里面按照先进先出拣货。
其次,如果出库数有零散的,先从零散库存里按照先进先出拣货。
第三,如果零散拣货的库存不足,则允许再从整托库存里拆零。
第四,如果整托的库存不足,则用零散的库存来凑(这种情况就很少了)。
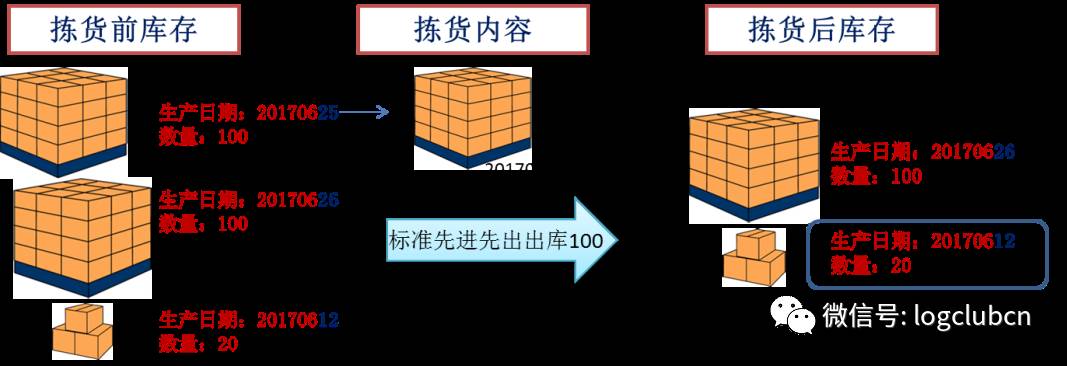
经过调整后的先进先出,既保证了先进先出的基本原则,又保证了整托出货不被拆散。解决了这个问题,员工对拣货效率的埋怨再也不存在了,老K对本次商超仓库管理越来越得心应手。
八、总结
实际上,老K遇到的问题远远不仅这几个。但任何事物都有其发展的原则和原理,只要认真分析,淡定处理,兵来将挡水来土掩,总是能找到解决的办法。有一点是可以肯定的,一个好的管理工具(比如合适的WMS),可以使管理达到事半功倍的效果。
而工具本身是死的,要想用好它,则是要靠使用者充分发挥主观能动性,积极想办法,积极和各个层次的人沟通;最终会发现,挡在面前的所有问题,都能迎刃而解。
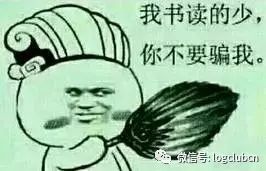
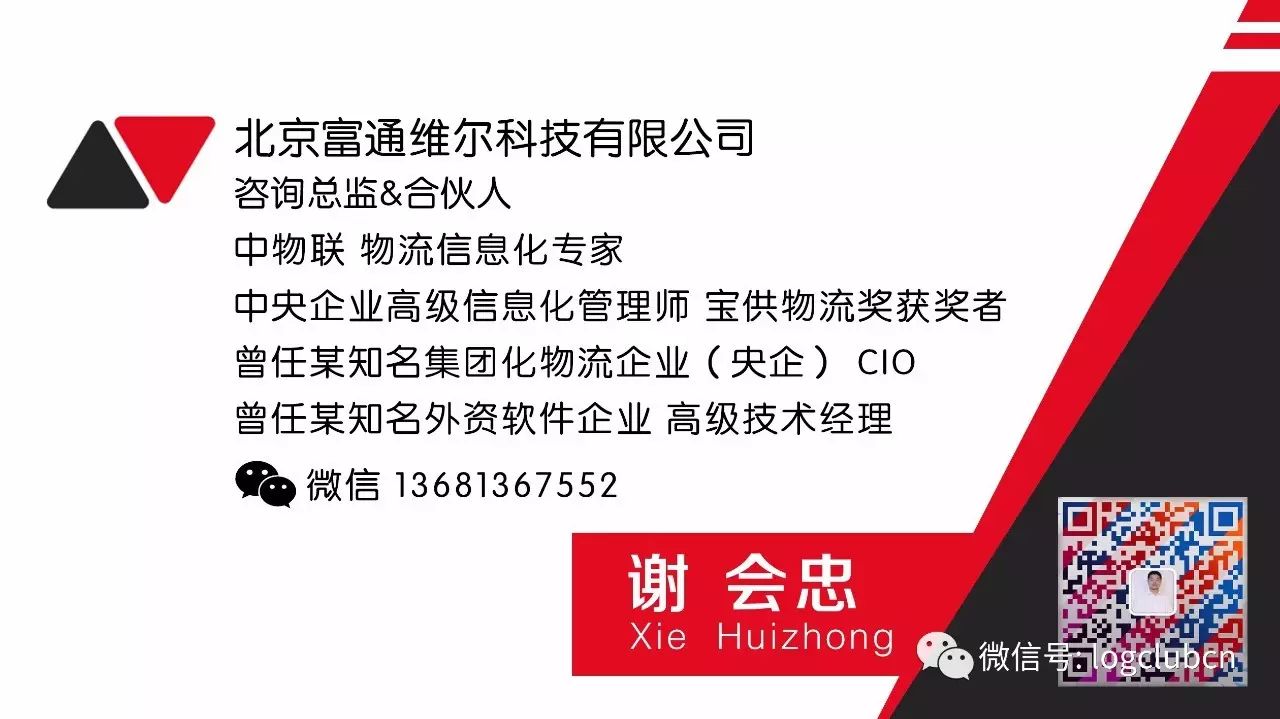
此文系作者个人观点,不代表物流沙龙立场
— END —
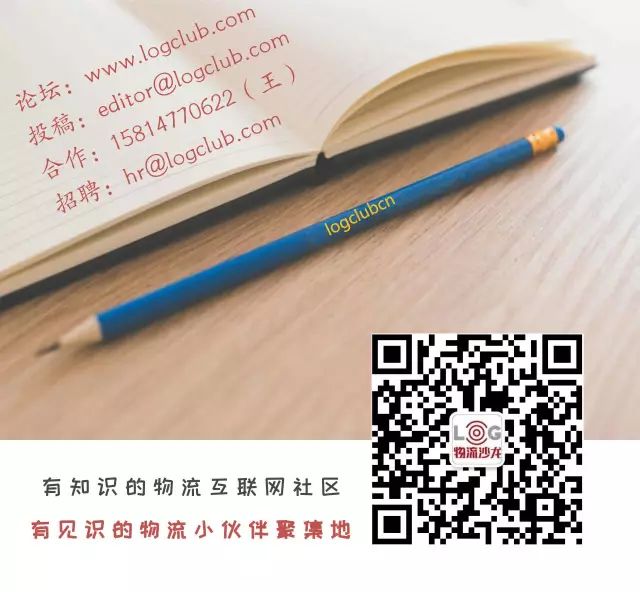