“去库存”已经从一个供应链管理的目标,成为了国家在供给侧改革中重要的工作任务了。当然,在国家经济层面谈论的去库存是指化解房地产库存。而我今天想和大家聊的还是供应链的话题,深度扒一扒原材料库存的事儿,就从订货模式和前置时间开始讲起。
一、订货模式
物料计划 小沈
我该在什么时候给供应商下订单?
每次订单该下多少数量?
这是物料计划员在面对订货的时候需要考虑的问题。
关于这个问题,主要的解决方法有二种。
这种模式的原理是,事先设定一个固定的订货数量点,当库存的数量低于这个点,就需要给供应商下新的订单。设定的订货数量点,必须有足够的库存来满足未来的需求,直到下一批订单的到货。
点击图片看大图
订货点 = 前置时间内的总需求 + 安全库存
让我们来举一个例子,前置时间一共是6周,这段时间是从订单发送给供应商,直到货物送至指定地点的全部时间,简单来说这段时间包括订单处理、生产过程和运输时间。如果每周的平均需求是50,安全库存是100,那么订货点的计算如下:
订货点 = (6 X 50)+100 = 400
在固定订货数量模式下,每当库存消耗至订货点以下,物料计划员就需要立即做一个新的订单。每次下订单的时间是不固定的,但是订单的数量可以是固定的,一般都用经济订货量Economics Order Quantity,简称EOQ。
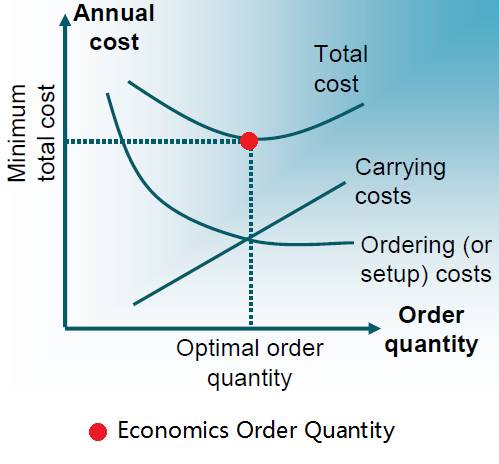
当订货成本等于库存持有成本,总成本达到最低,也就是经济订货量(EOQ)
EOQ的计算公式如下:
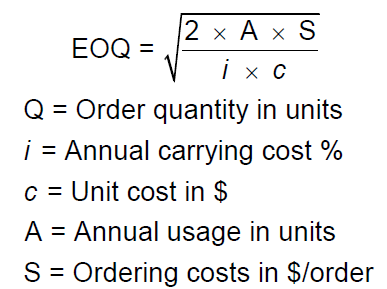
Annual Carrying cost,也就是库存的持有成本。
这里面主要包括以下这些费用,在计算的时候是取持有成本占库存成本的百分比。在不同的行业之间,这个百分比有一些差异。
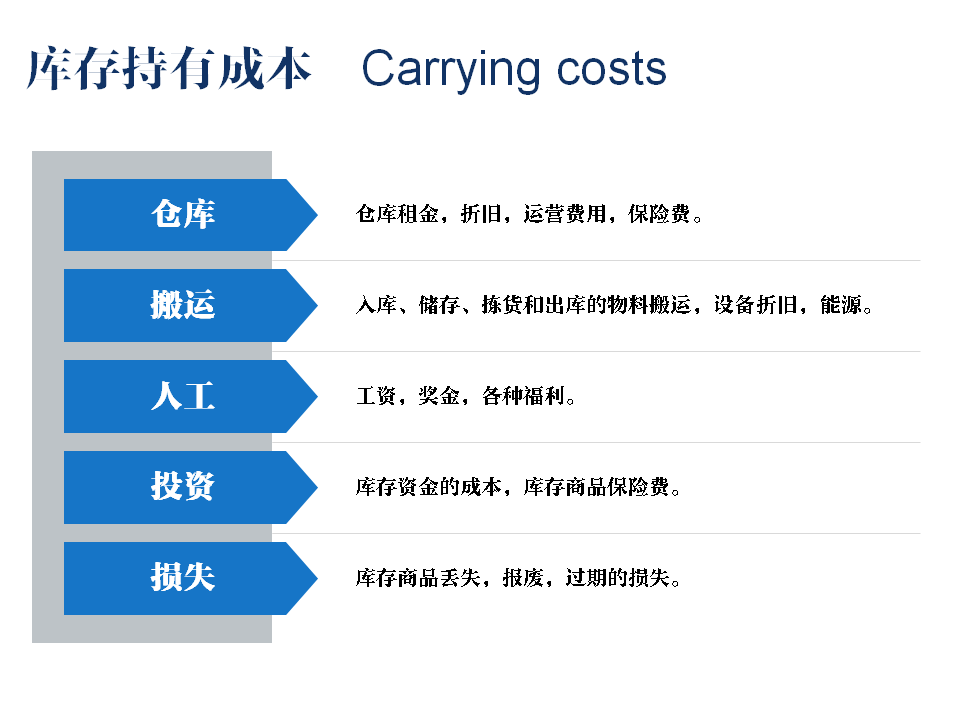
Unit cost,原材料的采购单价。
Annual usage in unit,原材料每年的使用量。
Ordering cost,订货成本。
主要是物料计划员在创建采购订单时候花费的全部时间,根据基本工资,最后换算成费用。
固定订货数量模式在操作上的有这些特点:
1、下订单的时间不固定,物料计划员的日常工作存在很大的随机性,可能无法合理安排每天的工作,工作量不均衡。
2、如果没有系统提醒的话,物料计划员可能会忽视下订单的时间点。
3、如果前置时间或这段时间内的平均需求发生变化,那么订货点和安全库存的数量也要随之变化。
4、当企业按照经济订货批量来订货时,可实现订货成本和库存持有成本的最优化。
这种模式是特点是订货间隔期的时间是固定的,物料计划员在固定的时间点来检查核对未来需求和库存情况,根据前置时间,来创建新的采购订单。订货的间隔期可以是一天、一周、甚至是一个月。每次订货的数量是变动的,除非客户的需求和生产排程非常稳定。
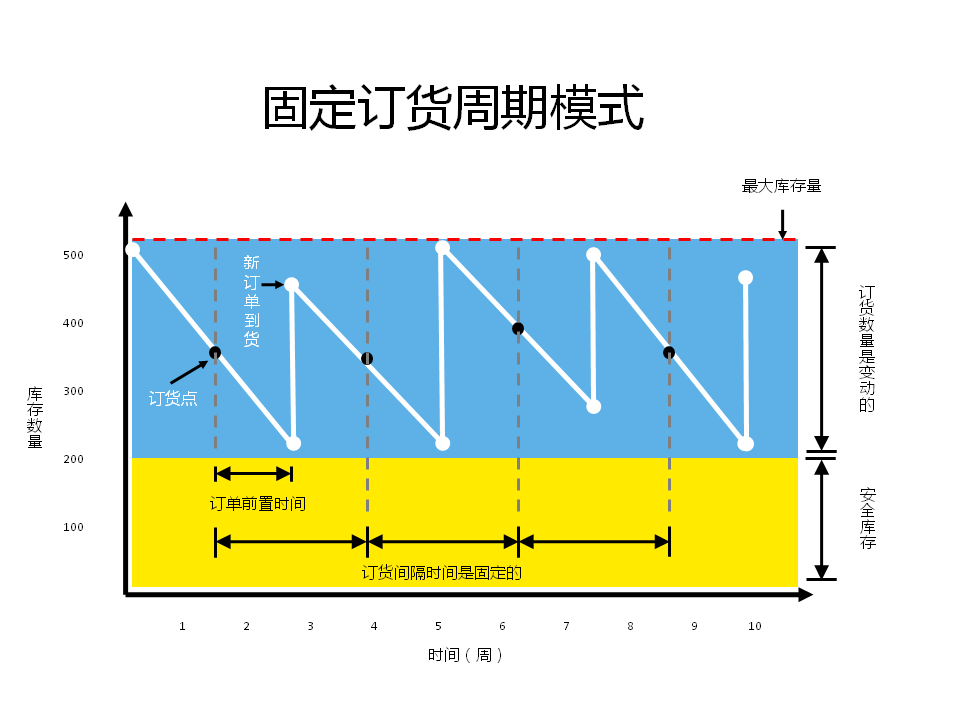
点击图片看大图
固定周期模式首先要设定一个最大库存量,计算公式如下:
最大的库存量 = (二次订货间隔天数 + 前置时间) X 平均每天的需求用量 + 安全库存
而每次需要订货的数量是在最大库存量的基础上,减去库存和在途数量,公式如下:
订货数量 = (二次订货间隔天数 + 前置时间) X 平均每天的需求用量 + 安全库存 – (库存数量 + 在途数量)
让我们也举一个例子:
二次订货间隔天数是7天,前置时间是28天,平均每天的需求量是20,安全库存200,当前库存数量是150,还有50的在途数量。那么我们需要的最大的库存数量就等于:
最大库存量 = (7 + 28)X 20 + 200 = 900
本次需要下订单的数量 = 900 - (150 + 50) = 700
固定订货周期模式有这样几个特点:
1、物料计划员需要根据预先计划好的日期,来review未来几周或是几月的需求,再结合库存的情况,就能很快地完成数据分析,创建出一张新的采购订单。
2、物料计划员可以合理分配工作量,在每个工作日都可以完成一定数量的采购订单。
3、可以有效地控制库存,因为在计算订单数量的时候,我们已经设置了一个最大库存量,同时我们也考虑库存和在途的数量,避免了过量订货。
4、灵活设定订货周期,如果供应商的SKU数量和需求量都很多,那么就可以缩短订货间隔天数,比如每天下订单;反之,就可以延长订货周期,比如每月下一次订单。
固定订货数量或是订货周期的模式各有其特色,企业可以结合自身的情况,选择合适的订货模式。
二、前置时间(Lead time)对于库存的影响

库存就像是水管子的水,前置时间就像是水管的长度,水管越长,库存也就越多。
不管是在哪一种订货模式下,其中都有一个重要的因素决定着库存的水平,这就是前置时间(Lead time)。如同前文中所提到的,前置时间包含从订单发送给供应商,直到货物送至指定地点的全部时间,这段时间主要包括订单处理、生产过程和运输时间。根据订货模式的计算公式,如果可以缩短前置时间(不管是其中的任何一段),都可以有效地降低库存,而且特别适用于进口件原材料的库存控制上。
进口原材料主要有2个特点:
1、刚需价格高。
为什么会要进口原料?是因为我们还没有在国内找到替代品或是本地的资源,只能从国外进口。由于进口件在技术上普遍处在领先或者垄断的地位,商品的价格是比较高的。
2、前置时间长。
首先是交货时间长,很多海外供应商是不给客户备库存的,而是需要收到部分或是全额付款以后才会开始购买原材料,准备生产的。这样一来,从订单接收到订单完成的周期就会很长了,可能会有2-3月。
其次是运输的时间长,以海运为例,运输时间包括了从供应商仓库提货,出口报关,海上运输,进口清关,到最后的国内运输至仓库,目前从欧洲到中国的全部运输时间需要大约2个月。
这样计算的话,全部的前置时间(交货 + 运输)可能长达4-5个月之久,这对于进口件库存的影响是很大的。如果采购和供应商签订的是Ex works条款的话,买方就需要承担全部的库存的成本;如果和供应商签的是DDP条款,那么库存的成本就可以转嫁到供应商这边,但是前提条件是供应商愿意来配合。除了成本的考量以外,这里面还涉及到一些供应链深层次的思考,我之前写过一篇文章,深入探讨了Ex works和DDP条款的利与弊。
为了分析前置时间对于库存的实际影响,我用一组数据进行了模拟分析。我选取了119个进口原材料SKU,采购单价从0.04到49.68元不等。总共涉及20个海外供应商,前置时间从40天到88天不等。

点击图片看大图
我把所有SKU的前置时间都减少或者增加了10%和20%来看库存金额和天数的变化情况。毫无疑问,当前置时间减少的时候,库存也会随之减少;反之,库存就会增加。
这个模拟的结果对我们有什么启示?如果想把库存金额和天数降低,缩短前置时间(Lead time)是一个很好的切入点。想要达成这个目标,我们需要供应商的配合。如何调动供应商的积极性呢?这就是另一个需要讨论的话题了。
系统性地降低原材料库存的方法有几种,比如提高客户预测的准确性,做好需求和供应的协同,提高库存的准确性等等。同时,我们也不能忽视前置时间对于库存的影响。题图来源:全景网