今天就和小七一起学一下蒸发器种类、设计方法和选型标准那些事,只要是你想了解的这里都有哦!如果你也是蒸发行业的七友,希望给小七提出你宝贵的意见。
蒸发器的种类
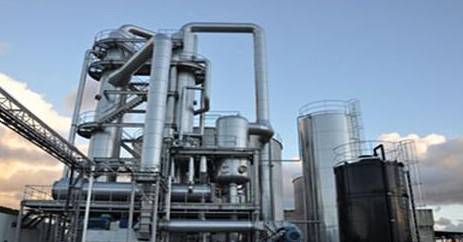
随着工业蒸发技术的不断发展,蒸发设备的结构与型式亦不断改进与创新,其种类繁多,结构各异。目前工业上实用的蒸发设备约有六十余种,其中最常用的也有十余种型式,本节仅介绍常用的几种。
常用蒸发器主要由加热室和分离室两部分组成。加热室的型式有多种,最初采用夹套式或蛇管式加热装置,其后则有横卧式短管加热室及竖式短管加热室。
继而又发明了竖式长管液膜蒸发器,以及刮板式薄膜蒸发器等等。根据溶液在蒸发器中流动的情况,大致可将工业上常用的间接加热蒸发器分为循环型与单程型两类。
1.循环型蒸发器
这类蒸发器的特点是溶液在蒸发器内作循环流动。根据造成液体循环的原理的不同,又可将其分为自然循环和强制循环两种类型。前者是藉助在加热室不同位置上溶液的受热程度不同,使溶液产生密度差而引起的自然循环;后者是依靠外加动力使溶液进行强制循环。目前常用的循环型蒸发器有以下几种:
(1)中央循环管式蒸发器
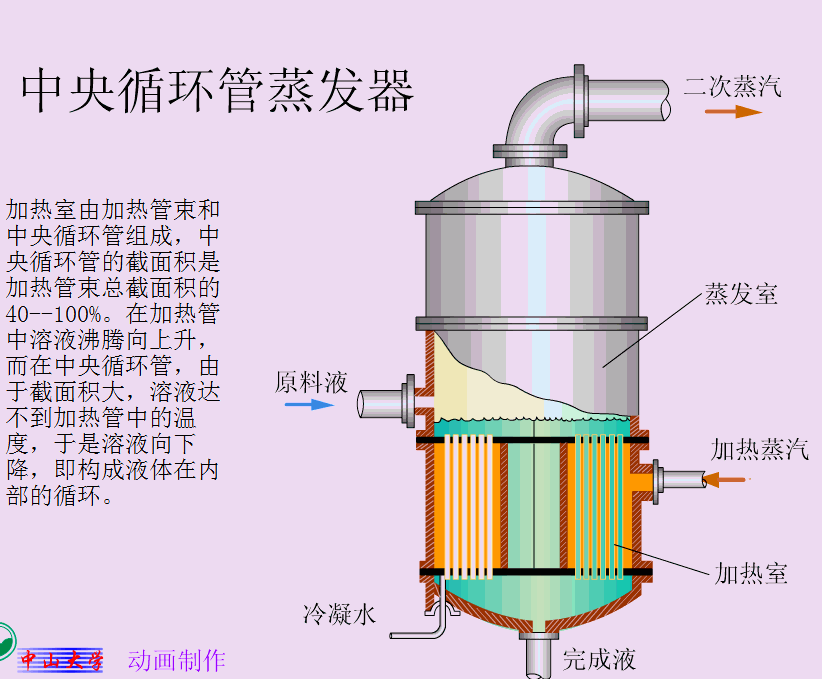
中央循环管式蒸发器的结构如图片所示,其加热室由一垂直的加热管束(沸腾管束)构成,在管束中央有一根直径较大的管子,称为中央循环管,其截面积一般为加热管束总截面积的40~100%。
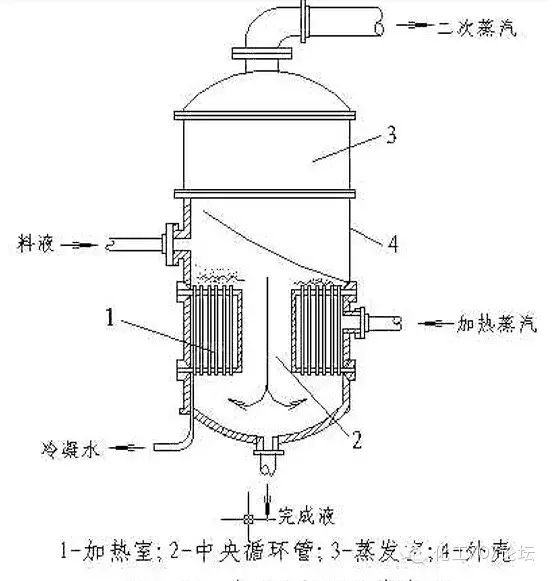
中央循环管蒸发器具有结构紧凑、制造方便、操作可靠等优点,故在工业上的应用十分广泛,有所谓“标准蒸发器”之称。但实际上,由于结构上的限制,其循环速度较低(一般在0.5m/s以下);而且由于溶液在加热管内不断循环,使其浓度始终接近完成液的浓度,因而溶液的沸点高、有效温度差减小。此外,设备的清洗和检修也不够方便。
(2)悬筐式蒸发器
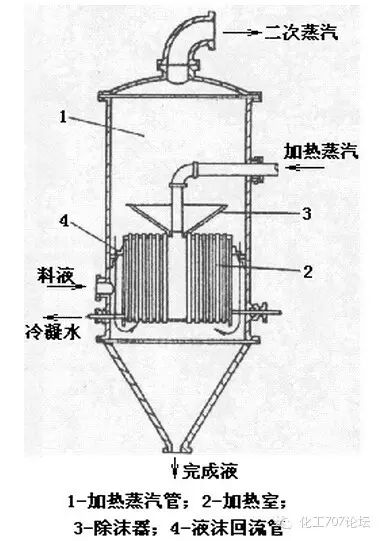
由于与蒸发器外壳接触的是温度较低的沸腾液体,故其热损失较小。悬筐式蒸发器适用于蒸发易结垢或有晶体析出的溶液。它的缺点是结构复杂,单位传热面需要的设备材料量较大。
(3)外热式蒸发器
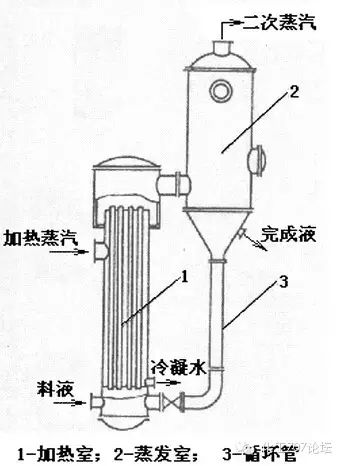
外热式蒸发器的特点是加热室与分离室分开,这样不仅便于清洗与更换,而且可以降低蒸发器的总高度。因其加热管较长(管长与管径之比为50~100),同时由于循环管内的溶液不被加热,故溶液的循环速度大,可达1.5m/s。
(4)列文蒸发器
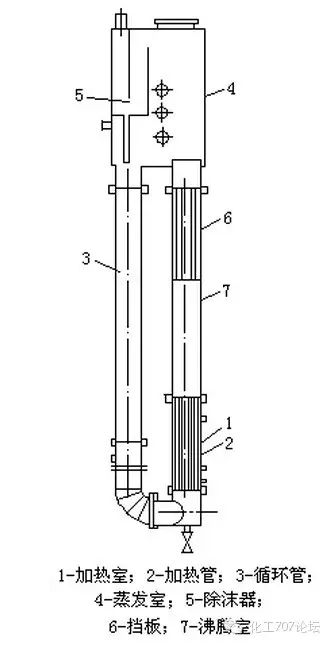
列文蒸发器的优点是循环速度大,传热效果好,由于溶液在加热管中不沸腾,可以避免在加热管中析出晶体,故适用于处理有晶体析出或易结垢的溶液。其缺点是设备庞大,需要的厂房高。此外,由于液层静压力大,故要求加热蒸汽的压力较高。
(5)强制循环蒸发器
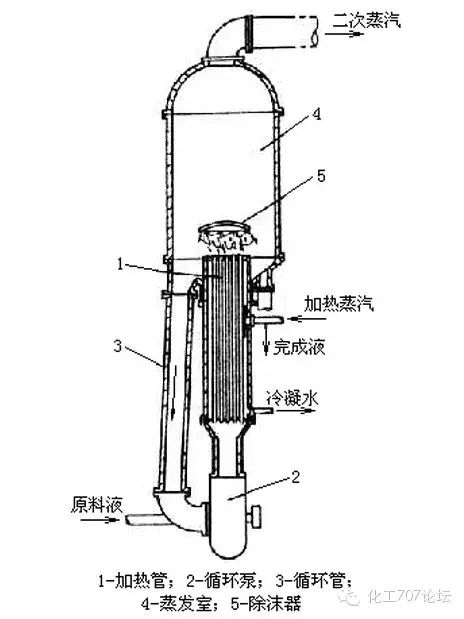
这种蒸发器的优点是传热系数大,对于粘度较大或易结晶、结垢的物料,适应性较好,但其动力消耗较大。
2.单程型蒸发器
这类蒸发器的特点是,溶液沿加热管壁成膜状流动,一次通过加热室即达到要求的浓度,而停留时间仅数秒或十几秒钟。
单程型蒸发器的主要优点是传热效率高,蒸发速度快,溶液在蒸发器内停留时间短,因而特别适用于热敏性物料的蒸发。
按物料在蒸发器内的流动方向及成膜原因的不同,可以分为以下几种类型:
升膜蒸发器;
降膜蒸发器;
升—降膜蒸发器;
刮板薄膜蒸发器。
(1)升膜蒸发器
升膜式蒸发器其加热室由一根或数根垂直长管组成,通常加热管直径为25~50mm,管长与管径之比为100~150。
升膜蒸发器适用于蒸发量较大(即稀溶液)、热敏性及易起泡沫的溶液,但不适于高粘度、有晶体析出或易结垢的溶液。
(2)降膜蒸发器
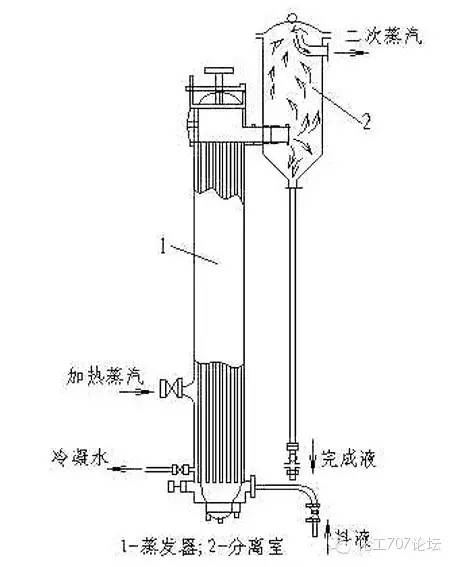
降膜蒸发器可以蒸发浓度较高的溶液,对于粘度较大的物料也能适用。但对于易结晶或易结垢的溶液不适用。此外,由于液膜在管内分布不易均匀,与升膜蒸发器相比,其传热系数较小。
(3)升—降膜蒸发器
将升膜和降膜蒸发器装在一个外壳中,即构成升—降膜蒸发器,原料液经预热后先由升膜加热室上升,然后由降膜加热器下降,再在分离室中和二次蒸汽分离后即得完成液。
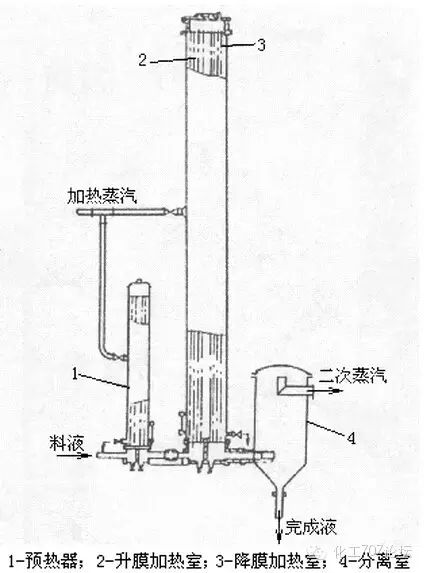
这种蒸发器多用于蒸发过程中溶液的粘度变化很大,水分蒸发量不大和厂房高度有一定限制的场合。
(4)刮板薄膜蒸发器
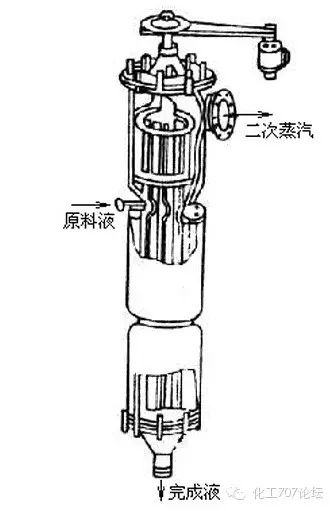
在某些情况下,可将溶液蒸干而由底部直接获得固体产物。
这类蒸发器的缺点是结构复杂,动力消耗大,传热面积小,一般为3~4m2,最大不超过20m2,故其处理量较小。
3.直接接触传热的蒸发器
在实际生产中,除上述循环型和单程型两大类间壁式传热的蒸发器外,有时还应用直接接触传热的蒸发器。
它是将燃料(通常是煤气或重油)与空气混合后燃烧产生的高温烟气直接喷入被蒸发的溶液中,高温烟气与溶液直接接触,使得溶液迅速沸腾汽化。蒸发出的水分与烟气一起由蒸发器的顶部直接排出。
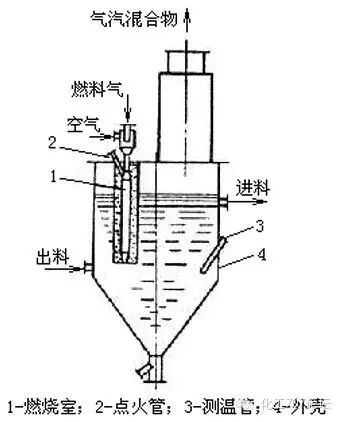
通常这种蒸发器的燃烧室在溶液中的深度为200~600mm,燃烧室内高温烟气的温度可达1000℃以上,但由于气液直接接触时传热速率快,气体离开液面时只比溶液温度高出2~4℃。燃烧室的喷嘴因在高温下使用,较易损坏,故应选用耐高温和耐腐蚀的材料制作,结构上应考虑便于更换。
浸没燃烧蒸发器的特点是结构简单,传热效率高。该蒸发器特别适用于处理易结晶、结垢或有腐蚀性的物料的蒸发。目前在废酸处理和硫酸铵盐溶液的蒸发中,已广泛采用此种蒸发器。但它不适用于不可被烟气污染物料的处理,而且它的二次蒸汽也很难利用。
由于篇幅限制本文中对于各种蒸发器的原理工作没有做详细介绍,想了解此内容可以到化工707app中搜索蒸发结晶查看更多详细内容。
这么多蒸发器那么蒸发过程到底该怎么设计计算呢?一起来学习吧!
蒸发器的设计步骤
1.多效蒸发的计算一般采用迭代计算法
(1)根据工艺要求及溶液的性质,确定蒸发的操作条件(如加热蒸汽压强及冷凝器压强)、蒸发器的形式(升膜蒸发器、降膜蒸发器、强制循环蒸发器、刮膜蒸发器)、流程和效数。
(2)根据生产经验数据,初步估计各效蒸发量和各效完成液的组成。
(3)根据经验,假设蒸汽通过各效的压强降相等,估算各效溶液沸点和有效总温差。
(4)根据蒸发器的焓衡算,求各效的蒸发量和传热量。
(5)根据传热速率方程计算各效的传热面积。若求得的各效传热面积不相等,则应按下面介绍的方法重新分配有效温度差,重复步骤(3)至(5),直到所求得的各效传热面积相等(或满足预先给出的精度要求)为止。
2.蒸发器的计算方法
下面以三效并流加料的蒸发装置为例介绍多效蒸发的计算方法。
(1)估值各效蒸发量和完成液组成

在蒸发过程中,总蒸发量为各效蒸发量之和

任何一效中料液的组成为

一般情况下,各效蒸发量可按总政发来那个的平均值估算,即

对于并流操作的多效蒸发,因有自蒸发现象,可按如下比例进行估计。例如,

以上各式中:
W — 总蒸发量,kg/h;
W1,W2 ,… ,Wn — 各效的蒸发量,kg/h;
F — 原料液流量,kg/h;
x0, x1,…, xn — 原料液及各效完成液的组成,质量分数。
(2)估值各效溶液沸点及有效总温度差
欲求各效沸点温度,需假定压强,一般加热蒸汽压强和冷凝器中的压强(或末效压强)是给定的,其他各效压强可按各效间蒸汽压强降相等的假设来确定。即

式中:
— 各效加热蒸汽压强与二次蒸汽压强之差,Pa;
p1—第一效加热蒸汽的压强,Pa;
p'k— 末效冷凝器中的二次蒸汽的压强,Pa。
多效蒸发中的有效传热总温度差可用下式计算:

式中:
— 有效总温度差,为各效有效温度差之和,℃;
T1— 第一效加热蒸汽的温度,℃;
T'k— 冷凝器操作压强下二次蒸汽的饱和温度,℃;
— 总的温度差损失,为各效温度差损失之和,℃。

式中
— 由于溶液的蒸汽压下降而引起的温度差损失,℃;
— 由于蒸发器中溶液的静压强而引起的温度差损失,℃;
— 由于管路流体阻力产生压强降而引起的温度差损失,℃。
关于
、
和
的求法,分别介绍如下:
a.由于溶液蒸汽压下降多引起的温度差损失可用校正系数法和杜林规则求得。

式中
— 常压下由于溶液蒸汽压下降引起的温度差损失,℃;
某些溶液在常压下的沸点tA值可从手册差得;
— 校正系数,量纲为一。

式中 :
T'1— 操作压强下水的沸点,亦即二次蒸汽的饱和温度,℃;
r'— 操作压强下二次蒸汽的汽化热,kJ/kg.
杜林规则:某种溶液的沸点和相同压强下标准液体(一般为水)的沸点呈线性关系。在以水的沸点为横坐标,该溶液的沸点为纵坐标并以溶液的组成为参数的直角坐标图上,可得一组直线,称为杜林直线。利用杜林线图,可根据溶液的组成及世纪压强下水的沸点查出相同压强下溶液的沸点,从而得出
值。
根据杜林规则也可计算液体在各种压强下沸点的近似值。此法的依据是:某液体在两种不同压强下两沸点之差 与水同样压强下两沸点之差 ,其比值为一常数,即
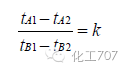
求得k 值,其他任一压强下的沸点t'A就可由下式求得,即
(1-11)
所以不用杜林线图也可计算出溶液的
值。
b.由于蒸发器中溶液静压强引起的温度差损失
某些蒸汽器在操作室,器内溶液需维持一定的液位,因而蒸发器中溶液内部的压强大于液面的压强,致使溶液内部的沸点较液面处高,二者之差即为因溶液静压强引起的温度差损失
。为简便起见,溶液内部的沸点可按液面和底层的平均压强来查取。平均压强近似按静力学方程估算:
(1-12)
式中:
pm — 蒸发器中液面和底部间的平均压强,Pa;
p'— 二次蒸汽的压强,即液面处的压强,Pa;
ρ— 溶液的平均密度,kg/m3;
L— 液层高度,m;
g— 重力加速度,m/s2。
(1-13)
式中:
tpm— 根据平局压强 求得水的沸点,℃;
tp— 根据二次蒸汽压强 求得水的沸点,℃。
由于管道流动阻力产生的压强降所引起的温度差损失
在多效蒸发中,末效以前各效的二次蒸汽流到次一效的加热室的过程中,由于管道阻力使其压强降低,蒸汽的饱和温度也相应降低,由此而引起的温度插损失即为
。根据经验,取各效间因管道阻力引起的温度差损失为1℃.根据已估算的各效二次蒸汽压强 及温度差损失 ,即可由下式估算各效溶液的沸点t。
(1-14)
3.加热蒸汽消耗量和各效蒸发水量的初步计算
第一效的焓衡算式为

由式(1-15)可求得第I 效的蒸发量Wi。若在焓衡算式中计入溶液的浓缩热及蒸发器的热损失,尚需考虑热利用系数η 。一般溶液的蒸发,可取η为0.98-0.7 (式中△X为溶液的组成变化,以质量分数表示)。

式中:
Di — 第i 效的加热蒸汽量,kg/h,当无额外蒸汽抽出时,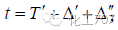
ri— 第i 效加热蒸汽的汽化热,kJ/kg;
r'i— 第i 效二次蒸汽的汽化热,kJ/kg;
cPO— 原料液的比热容,kJ/(kg·℃);
cPW— 水的比热容,kJ/(kg·℃);
ti、 ti - 1—第i 效及第(i-1)效溶液的沸点,℃;
ηi— 第i 效的热利用系数,量纲为一。
对于加热蒸汽(生蒸汽)的消耗量,可列出各效焓衡算式并与式(1-2)联解而求得。
4.蒸发器的传热面积和有效温度差在各效中的分配
任一效的传热速率方程为
(1-17)
式中:
Qi— 第i 效的传热速率,W;
Ki— 第i 效的传热系数,W;
Si— 第i 效的传热面积,m2;
△ti— 第i 效的传热温度差,℃。
有效温度分配的目的是为了求取蒸发的传热面积Si,现以三效为例,即
(1-18)
式中
(1-19)
(1-20)
在多效蒸发中,为了便于制造和安装,通常采用各效传热面积相等的蒸发器,即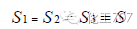
若由式(1-18)求得的传热面积不相等,应依据各效面积的原则重新分配各
效的有效温度差。方法如下:
设以△t'表示各效面相等时的有效温度差,则

与(1-18)式相比可得

将式(1-22)中三式相加,得

式中 ∑△t— 各效的有效温度差之和,称为有效总温度差,℃。
由式(1-23)求得传热面积S 后,即可由式(1-22)重新分配各效的有效温度差。重复上述步骤,直至求得的各效传热面积相等,该面积即为所求。
蒸发器的选型
如前所述,蒸发器的结构型式很多,在选择蒸发器的型式或设计蒸发器时,在满足生产任务要求、保证产品质量的前提下,还要兼顾所用蒸发器的结构简单、易于制造,操作和维修方便,传热效果好等等。除此而外,还要对被蒸发物料的工艺特性有良好的适应性,包括物料的粘性、热敏性、腐蚀性以及是否结晶或结垢等因素。
常用蒸发设备选型准则表
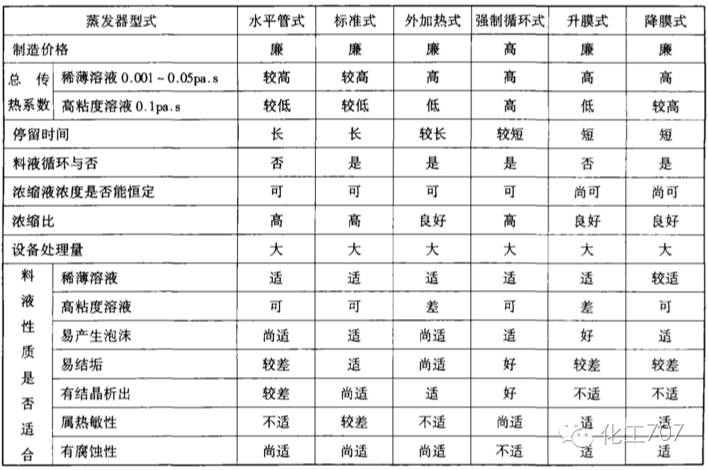
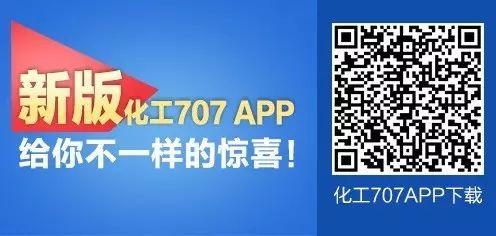
小七云盘使用方法,前点击“阅读原文”